MOCVD (Metal-Organic Chemical Vapor Deposition) is a critical process in semiconductor manufacturing, particularly for depositing thin films of materials like gallium nitride (GaN) or other compound semiconductors. The process involves the use of metal-organic precursors and is typically conducted at high temperatures to ensure proper decomposition of these precursors and high-quality film deposition. The temperature range for MOCVD is generally between 500°C and 1500°C, depending on the specific materials being deposited and the desired film properties. This high-temperature environment ensures efficient precursor decomposition and promotes the formation of high-quality, uniform films. Additionally, factors such as substrate rotation, optical channel dimensions, and deposition pressure play a role in optimizing the process.
Key Points Explained:
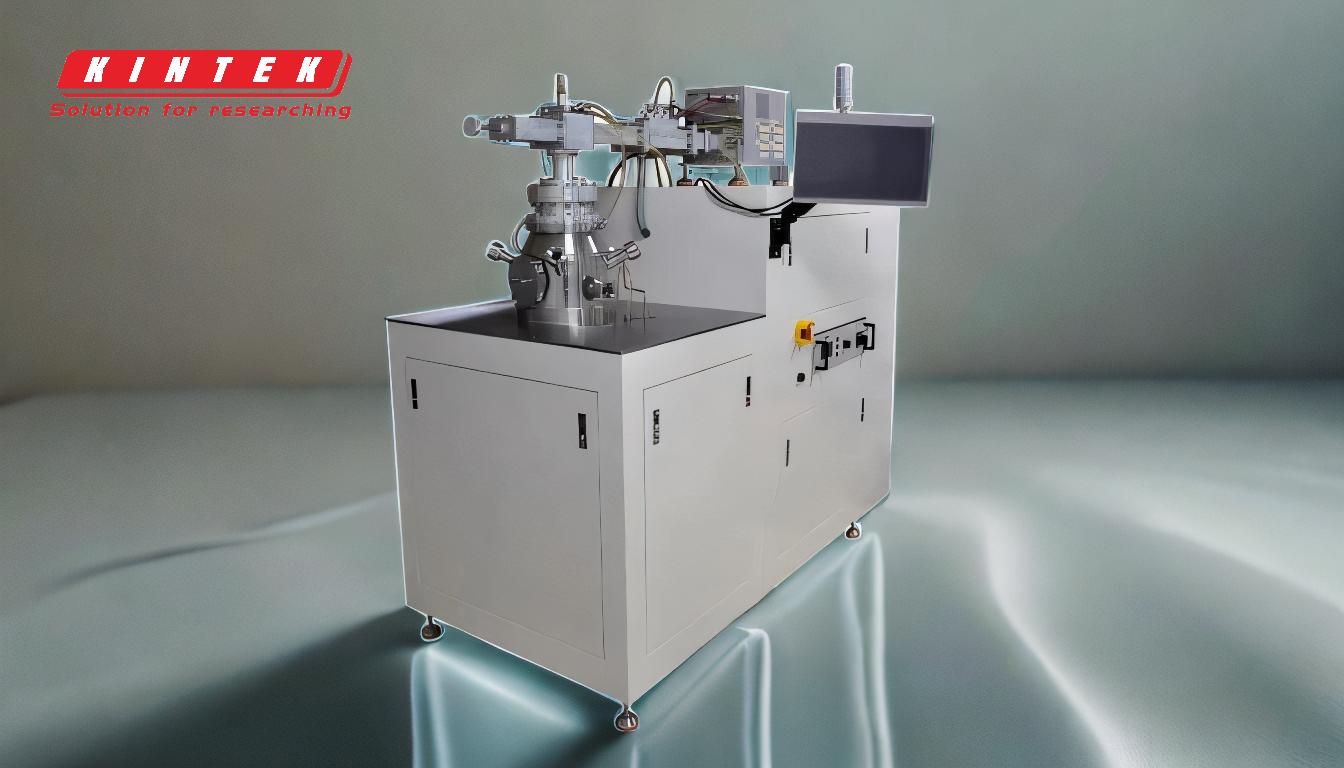
-
Temperature Range of MOCVD:
- MOCVD is performed at substrate temperatures ranging from 500°C to 1500°C. This wide range accommodates the deposition of various materials, such as GaN, GaAs, and other compound semiconductors.
- The high temperature is necessary to ensure the decomposition of metal-organic precursors and to promote the formation of high-quality crystalline films.
-
Role of Substrate Temperature:
- The substrate temperature is a critical parameter in MOCVD. It directly affects the sticking coefficient of the precursors, which determines how well the material adheres to the substrate.
- Optimal temperature ensures efficient deposition and minimizes defects in the film, leading to better electrical and optical properties.
-
Substrate Rotation:
- During MOCVD, the substrate is often rotated at speeds up to 1500 RPM. This rotation improves the uniformity of the deposited film by ensuring even exposure of the substrate to the precursor gases.
- Uniformity is crucial for applications in optoelectronics and semiconductor devices, where consistent film thickness and composition are required.
-
Optical Channel and Path Distance:
- The optical channel in MOCVD systems is typically limited to less than 10 mm, with a short optical path distance (e.g., 250 mm or less). This design minimizes interference and ensures precise control over the deposition process.
- A short optical path also helps in maintaining the stability of the precursor flow and temperature distribution.
-
Deposition Pressure:
- MOCVD is usually performed at pressures close to atmospheric pressure. This pressure range is chosen to balance precursor delivery efficiency and film quality.
- Operating near atmospheric pressure simplifies the system design and reduces the complexity of maintaining vacuum conditions.
-
Substrate Compatibility and Precursor Selection:
- The choice of substrate and its surface preparation are critical for successful MOCVD. Substrates must be compatible with the precursors used and withstand the high temperatures of the process.
- Knowledge of the optimal temperature for efficient deposition of specific materials is essential for achieving the desired film properties.
By understanding these key points, equipment and consumable purchasers can make informed decisions about the MOCVD systems and materials they select, ensuring optimal performance and high-quality film deposition.
Summary Table:
Parameter | Details |
---|---|
Temperature Range | 500°C to 1500°C, depending on material and film properties. |
Substrate Rotation | Up to 1500 RPM for uniform film deposition. |
Optical Channel | Less than 10 mm, with a short optical path (≤250 mm) for precise control. |
Deposition Pressure | Near atmospheric pressure for balanced efficiency and film quality. |
Substrate Compatibility | Must withstand high temperatures and match precursor requirements. |
Optimize your MOCVD process for superior thin film deposition—contact our experts today!