Annealing is a heat treatment process used to alter the physical and sometimes chemical properties of a material, typically metals, to increase its ductility and reduce its hardness, making it more workable. The process involves heating the material to a specific temperature, holding it at that temperature for a certain period, and then cooling it slowly. The temperature range for annealing varies depending on the type of metal and its specific properties, but it generally involves heating the metal to a temperature where its crystalline structure becomes fluid while remaining solid. This allows for the repair of defects and the formation of a more ductile structure upon slow cooling.
Key Points Explained:
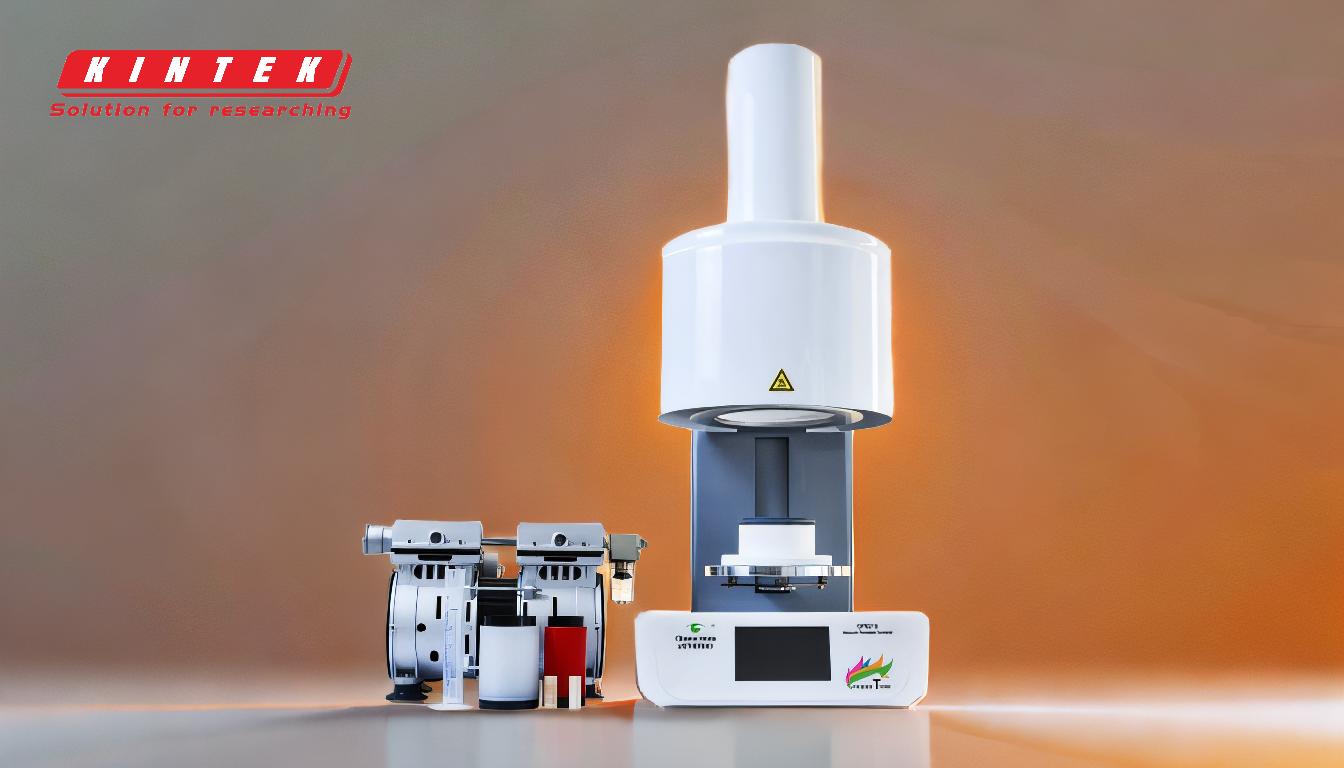
-
Definition of Annealing:
- Annealing is a heat treatment process aimed at increasing the ductility and reducing the hardness of metals. This is achieved by heating the metal to a specific temperature, maintaining that temperature, and then allowing it to cool slowly.
-
Temperature Range for Annealing:
- The temperature at which annealing occurs is critical and varies depending on the type of metal. Generally, the metal is heated to a temperature where its crystalline structure becomes fluid but remains in a solid state. This temperature is typically between 50% to 75% of the metal's melting point.
- For example, steel is often annealed at temperatures between 700°C to 900°C, while aluminum might be annealed at lower temperatures around 300°C to 400°C.
-
Importance of Holding Temperature:
- Once the metal reaches the desired annealing temperature, it is held at that temperature for a specific duration. This holding period allows for the diffusion of atoms within the metal, which helps in the repair of any defects in the crystalline structure.
- The duration of this holding period can vary from a few minutes to several hours, depending on the material and the desired outcome.
-
Cooling Process:
- After the metal has been held at the annealing temperature, it is allowed to cool slowly. The cooling rate is crucial because it determines the final properties of the metal.
- Slow cooling, often in a furnace or by burying the metal in an insulating material, allows the crystalline structure to reform in a more ductile and less stressed state.
-
Effects of Annealing:
- The primary effects of annealing are the reduction of hardness and the increase in ductility. This makes the metal easier to machine, form, or weld.
- Annealing also relieves internal stresses within the metal, which can improve its mechanical properties and reduce the likelihood of cracking or failure during subsequent processing or use.
-
Applications of Annealing:
- Annealing is widely used in various industries, including manufacturing, automotive, aerospace, and construction. It is particularly important in the production of steel, where it is used to improve the workability of the metal before further processing.
- In the electronics industry, annealing is used to improve the electrical properties of metals used in wiring and components.
In summary, the temperature range for annealing is a critical factor that depends on the type of metal being treated. The process involves heating the metal to a specific temperature, holding it there to allow for structural changes, and then cooling it slowly to achieve the desired properties. Understanding and controlling these parameters is essential for achieving the desired outcomes in material processing and manufacturing.
Summary Table:
Aspect | Details |
---|---|
Definition | Heat treatment to increase ductility and reduce hardness in metals. |
Temperature Range | 50% to 75% of the metal's melting point (e.g., steel: 700°C–900°C). |
Holding Temperature | Critical for structural changes; duration varies (minutes to hours). |
Cooling Process | Slow cooling to reform crystalline structure for ductility and stress relief. |
Effects | Reduces hardness, increases ductility, and relieves internal stresses. |
Applications | Used in manufacturing, automotive, aerospace, and electronics industries. |
Discover how annealing can improve your metal processing—contact our experts today!