The thermal regeneration process of activated carbon involves heating the spent carbon to high temperatures in a controlled environment to remove adsorbed contaminants and restore its adsorption capacity. This process, also known as reactivation, effectively destroys the adsorbed components on the carbon's surface, allowing it to be reused. The regenerated carbon retains its porous structure and adsorption properties, making it a cost-effective and sustainable solution for industries requiring repeated use of activated carbon. Below, the key aspects of the thermal regeneration process are explained in detail.
Key Points Explained:
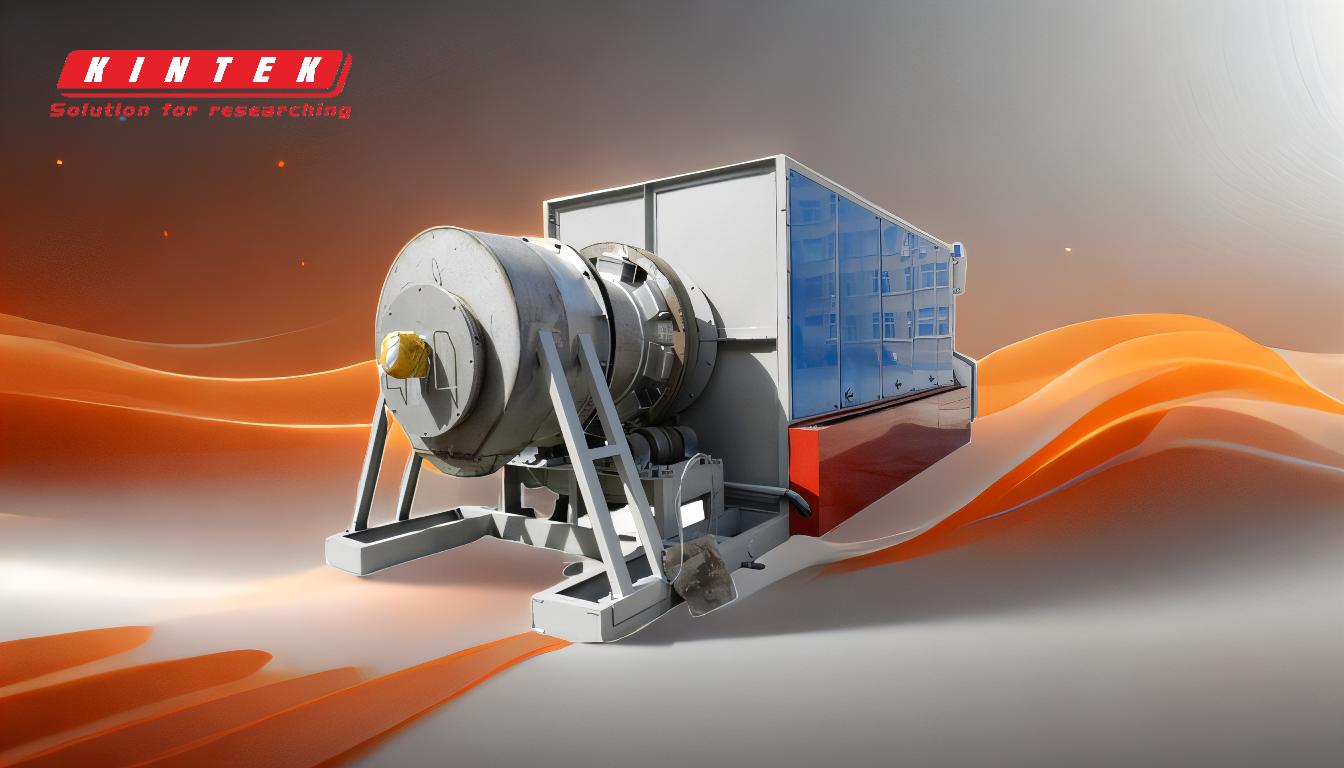
-
Definition and Purpose of Thermal Regeneration:
- Thermal regeneration is a process designed to restore the adsorption capacity of spent activated carbon by removing adsorbed contaminants through high-temperature treatment.
- The primary goal is to recycle activated carbon, reducing waste and operational costs while maintaining environmental sustainability.
-
Stages of Thermal Regeneration:
- Drying: The spent activated carbon is heated to around 100–150°C to remove moisture and volatile compounds. This step prepares the carbon for higher-temperature treatment.
- Pyrolysis: The temperature is increased to 400–700°C in an oxygen-free or low-oxygen environment. During this stage, organic contaminants are thermally decomposed into smaller molecules or gases, such as carbon dioxide and water vapor.
- Activation: The temperature is further raised to 700–900°C, often in the presence of steam or carbon dioxide. This step removes residual carbonized deposits and restores the carbon's porous structure, enhancing its adsorption capacity.
-
Mechanism of Contaminant Removal:
- Adsorbed contaminants are either volatilized or decomposed into gaseous byproducts during the high-temperature treatment.
- The carbon's porous structure is cleaned, and its surface area is restored, allowing it to adsorb new contaminants effectively.
-
Equipment Used for Thermal Regeneration:
- Rotary Kilns: Commonly used for large-scale regeneration, these cylindrical furnaces rotate to ensure uniform heating of the activated carbon.
- Multiple Hearth Furnaces: Feature stacked trays that move the carbon through different temperature zones for controlled regeneration.
- Fluidized Bed Reactors: Use gas to suspend the carbon particles, ensuring efficient heat transfer and uniform regeneration.
-
Advantages of Thermal Regeneration:
- Cost-Effectiveness: Reusing activated carbon reduces the need for frequent replacements, lowering operational expenses.
- Environmental Benefits: Minimizes waste generation and reduces the carbon footprint associated with producing new activated carbon.
- Efficiency: Restores the carbon's adsorption capacity to near-original levels, ensuring consistent performance.
-
Challenges and Considerations:
- Energy Consumption: High temperatures require significant energy input, making the process energy-intensive.
- Carbon Loss: A small percentage of carbon may be lost during regeneration due to oxidation or mechanical wear.
- Contaminant Type: Some contaminants, such as heavy metals, may not be fully removed through thermal regeneration and can accumulate over time.
-
Applications of Regenerated Activated Carbon:
- Water Treatment: Used in municipal and industrial water purification systems to remove organic pollutants, chlorine, and odors.
- Air Purification: Employed in air filters to capture volatile organic compounds (VOCs) and other airborne contaminants.
- Industrial Processes: Utilized in chemical, pharmaceutical, and food industries for solvent recovery and purification.
-
Sustainability and Future Trends:
- Thermal regeneration aligns with circular economy principles by extending the lifecycle of activated carbon.
- Advances in regeneration technology aim to reduce energy consumption and improve efficiency, making the process even more sustainable.
By understanding the thermal regeneration process, industries can make informed decisions about managing their activated carbon usage, balancing cost, performance, and environmental impact.
Summary Table:
Aspect | Details |
---|---|
Purpose | Restores adsorption capacity by removing contaminants via high-temperature treatment. |
Stages | 1. Drying (100–150°C) 2. Pyrolysis (400–700°C) 3. Activation (700–900°C) |
Equipment | Rotary Kilns, Multiple Hearth Furnaces, Fluidized Bed Reactors |
Advantages | Cost-effective, environmentally friendly, efficient restoration of capacity |
Challenges | High energy consumption, minor carbon loss, limited removal of heavy metals |
Applications | Water treatment, air purification, industrial processes |
Sustainability | Aligns with circular economy principles; advances aim to reduce energy use. |
Discover how thermal regeneration can optimize your activated carbon usage—contact our experts today for tailored solutions!