The time required for plasma nitriding, also known as the holding time, typically ranges between 12 to 50 hours. This duration depends on factors such as the type of material being treated and the desired depth of hardness. Plasma nitriding is a more efficient process compared to gas nitriding, requiring approximately half the holding time to achieve similar results. This efficiency is due to the use of plasma, which enhances the diffusion of nitrogen into the material surface, leading to faster and more controlled nitriding.
Key Points Explained:
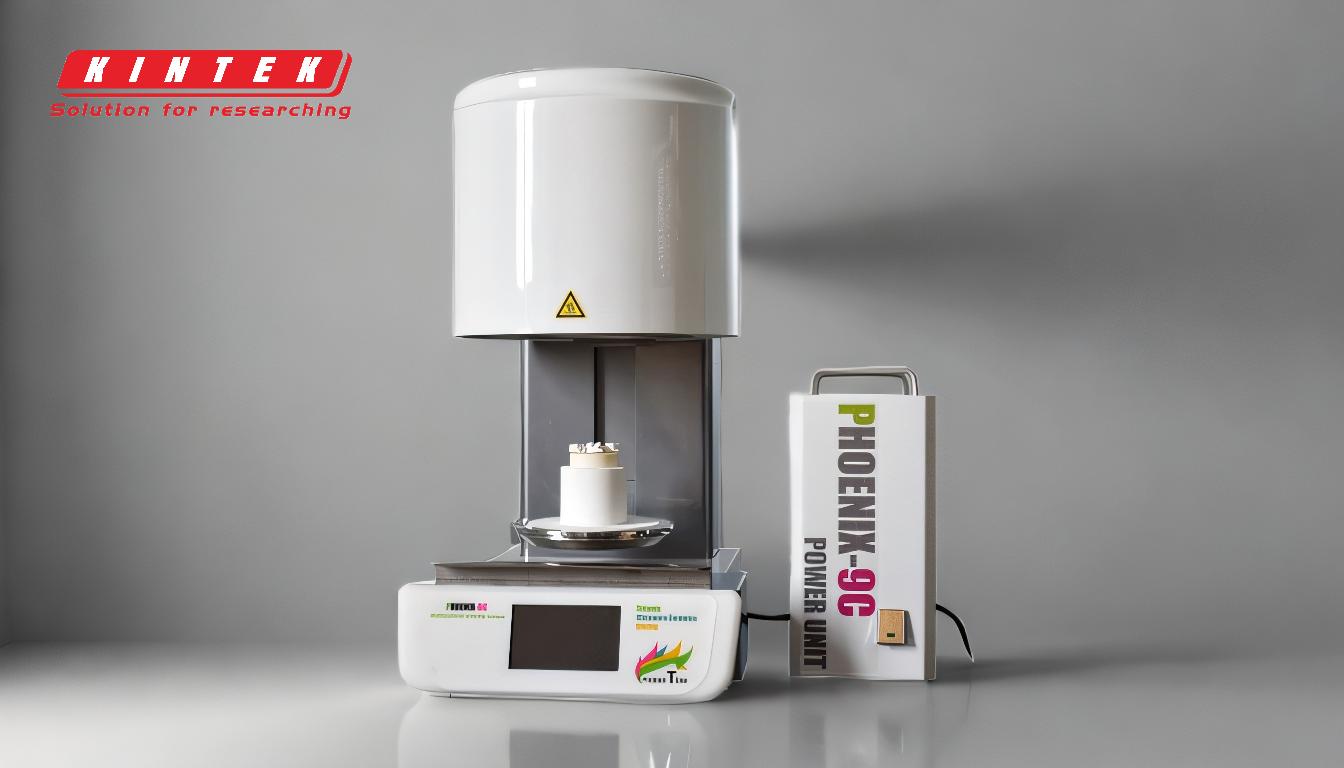
-
Typical Holding Time Range:
- Plasma nitriding generally requires a holding time between 12 to 50 hours.
- This range is influenced by the material type and the desired hardness depth. For example, harder materials or deeper hardness requirements may necessitate longer holding times.
-
Factors Influencing Holding Time:
- Material Type: Different materials have varying affinities for nitrogen diffusion. For instance, alloy steels may require shorter times compared to stainless steels due to their microstructure.
- Hardness Depth Requirements: Deeper hardness layers require longer nitriding times to allow sufficient nitrogen diffusion into the material.
-
Comparison with Gas Nitriding:
- Plasma nitriding is approximately twice as fast as gas nitriding. For example, if gas nitriding takes 24 hours, plasma nitriding might only take 12 hours for a similar result.
- This efficiency is due to the use of plasma, which accelerates the nitriding process by enhancing nitrogen diffusion and surface reactivity.
-
Process Efficiency:
- The plasma nitriding process involves a low-pressure environment and the generation of a high ionization glow discharge (plasma) around the component.
- This plasma creates a highly reactive environment, enabling faster and more uniform nitrogen diffusion into the material surface.
-
Practical Implications for Purchasers:
- For equipment or consumable purchasers, the shorter holding time of plasma nitriding translates to reduced energy consumption and faster turnaround times.
- This makes plasma nitriding a cost-effective and time-efficient option for surface hardening applications.
-
Applications and Benefits:
- Plasma nitriding is widely used in industries requiring high wear resistance, such as automotive, aerospace, and tool manufacturing.
- The process not only improves surface hardness but also enhances corrosion resistance and fatigue strength, making it suitable for critical components.
By understanding these key points, purchasers and engineers can make informed decisions about the suitability of plasma nitriding for their specific applications, balancing time, cost, and performance requirements.
Summary Table:
Aspect | Details |
---|---|
Typical Holding Time | 12 to 50 hours, depending on material and hardness depth requirements. |
Key Influencing Factors | Material type, desired hardness depth, and surface reactivity. |
Comparison with Gas Nitriding | Plasma nitriding is ~2x faster, reducing energy consumption and turnaround times. |
Process Efficiency | Low-pressure environment with plasma enhances nitrogen diffusion. |
Applications | Automotive, aerospace, tool manufacturing—improves wear and corrosion resistance. |
Discover how plasma nitriding can enhance your surface hardening process—contact our experts today!