A rotary furnace is a versatile thermal equipment used for various industrial processes, including melting, calcining, roasting, drying, and heat treatment of materials. It is particularly effective for recycling cast iron and aluminum scraps, with capacities ranging from 10kg to 1 ton. The furnace's design includes a rotating barrel with a slight inclination, ensuring uniform heat distribution and consistent radial temperature. Rotary furnaces are also used in optical manufacturing for creating lenses and mirrors, as well as in lead recovery processes. Additionally, they are employed in small-scale experiments and production for processes like sintering, coating, and pyrolysis. Their applications span industries such as metallurgy, ceramics, electronics, and environmental recycling.
Key Points Explained:
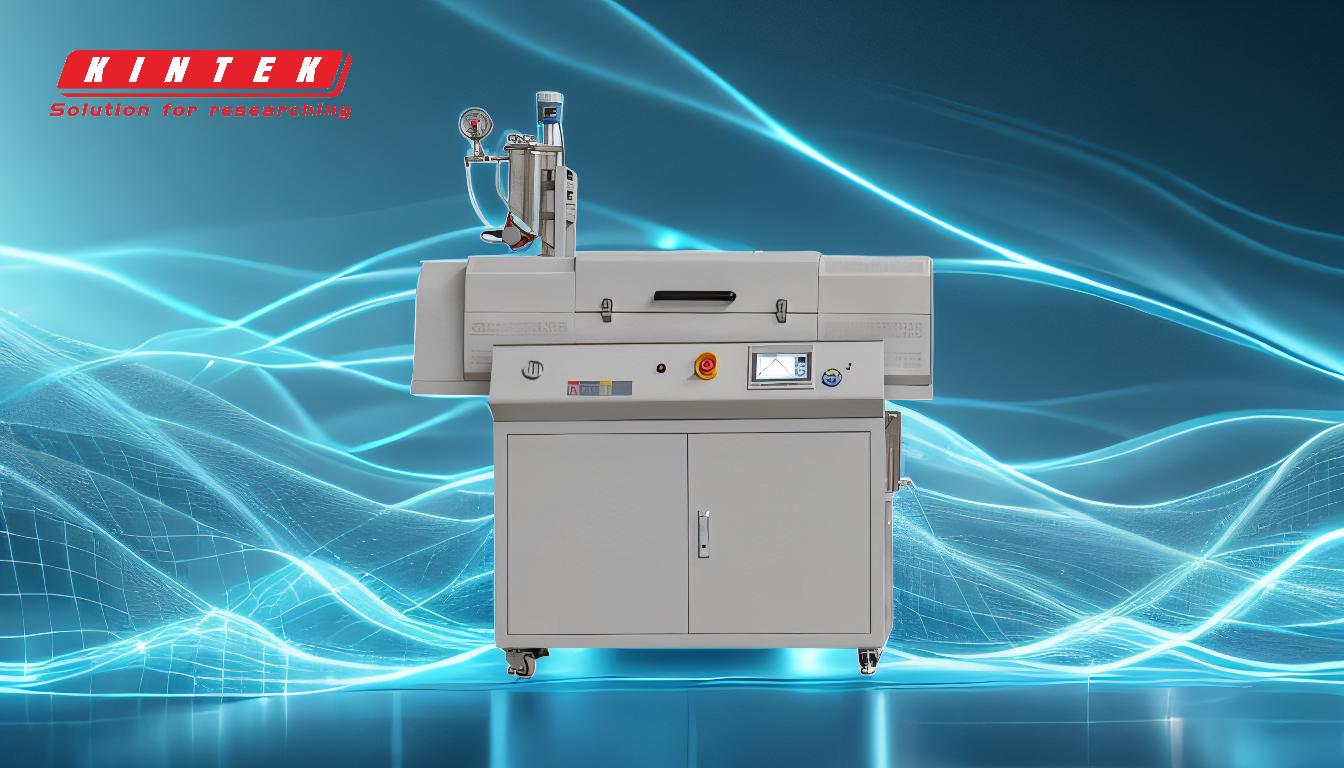
-
Primary Uses of Rotary Furnaces:
- Melting and Recycling: Rotary furnaces are widely used for melting cast iron and aluminum scraps, making them essential in recycling processes. Their flexible design allows for batch processing of materials ranging from 10kg to 1 ton.
- Heat Treatment: These furnaces are used for processes like oxidation and calcination, which involve thermal decomposition and electron reduction in materials. This makes them valuable in metallurgical and chemical industries.
- Optical Manufacturing: Rotary furnaces play a critical role in creating lenses and primary mirrors for optical telescopes, ensuring precision and high-quality outputs.
-
Design and Functionality:
- Rotating Barrel: The furnace features a long barrel that rotates slightly with an inclination. This design ensures continuous mixing and heating of materials as they move through the furnace.
- Uniform Heat Distribution: Heat is typically provided by electric heating outside the barrel, ensuring consistent radial temperature and efficient material processing.
-
Applications in Various Industries:
- Metallurgy: Rotary furnaces are used for melting and recycling metals like cast iron and aluminum. They are also employed in lead recovery processes, treating lead acid battery scrap, lead oxides, and other lead-containing materials.
- Ceramics and Electronics: Small rotary furnaces are used in universities and research institutes for processes like sintering, coating, and chemical vapor deposition (CVD), which are critical in powder, electronics, and ceramics industries.
- Environmental Recycling: The furnace is instrumental in recycling lead from batteries and other lead-containing waste, contributing to environmental sustainability.
-
Small-Scale and Experimental Uses:
- Research and Development: Small rotary furnaces are ideal for experiments and small batch production in academic and industrial settings. They are used for pre-sintering, sintering, high-temperature pyrolysis, and low-temperature deposition processes.
- Versatility: These furnaces are adaptable to various materials and processes, making them a valuable tool in scientific research and small-scale industrial production.
-
Advantages of Rotary Furnaces:
- Flexibility: The ability to handle a wide range of materials and processes makes rotary furnaces highly versatile.
- Efficiency: The rotating design ensures thorough mixing and uniform heating, leading to consistent and high-quality outputs.
- Scalability: Rotary furnaces are available in various sizes, from small experimental units to large industrial-scale models, catering to different production needs.
In summary, rotary furnaces are indispensable in multiple industries due to their versatility, efficiency, and ability to handle a wide range of materials and processes. Whether for recycling metals, manufacturing optical components, or conducting research, rotary furnaces provide reliable and consistent performance.
Summary Table:
Key Aspect | Details |
---|---|
Primary Uses | Melting, recycling, heat treatment, optical manufacturing, lead recovery |
Design Features | Rotating barrel, uniform heat distribution, electric heating |
Industries Served | Metallurgy, ceramics, electronics, environmental recycling |
Small-Scale Uses | Research, sintering, coating, pyrolysis, chemical vapor deposition (CVD) |
Advantages | Flexibility, efficiency, scalability, consistent performance |
Learn how a rotary furnace can enhance your industrial or research processes—contact our experts today!