A rotary furnace, also known as a rotating furnace, is a versatile and efficient piece of equipment used in various industrial and research applications. Its primary function is to heat materials uniformly while ensuring consistent exposure to the atmosphere, which enhances gas diffusion, reduces gas consumption, and improves heat treatment efficiency. The furnace's ability to rotate and tilt allows for precise material handling and placement, making it suitable for processes like sintering, annealing, chemical reactions, and coating preparation. Its uniform heating, wide applicability, and accurate temperature control make it indispensable in industries such as metallurgy, material science, electronics, and chemical processing.
Key Points Explained:
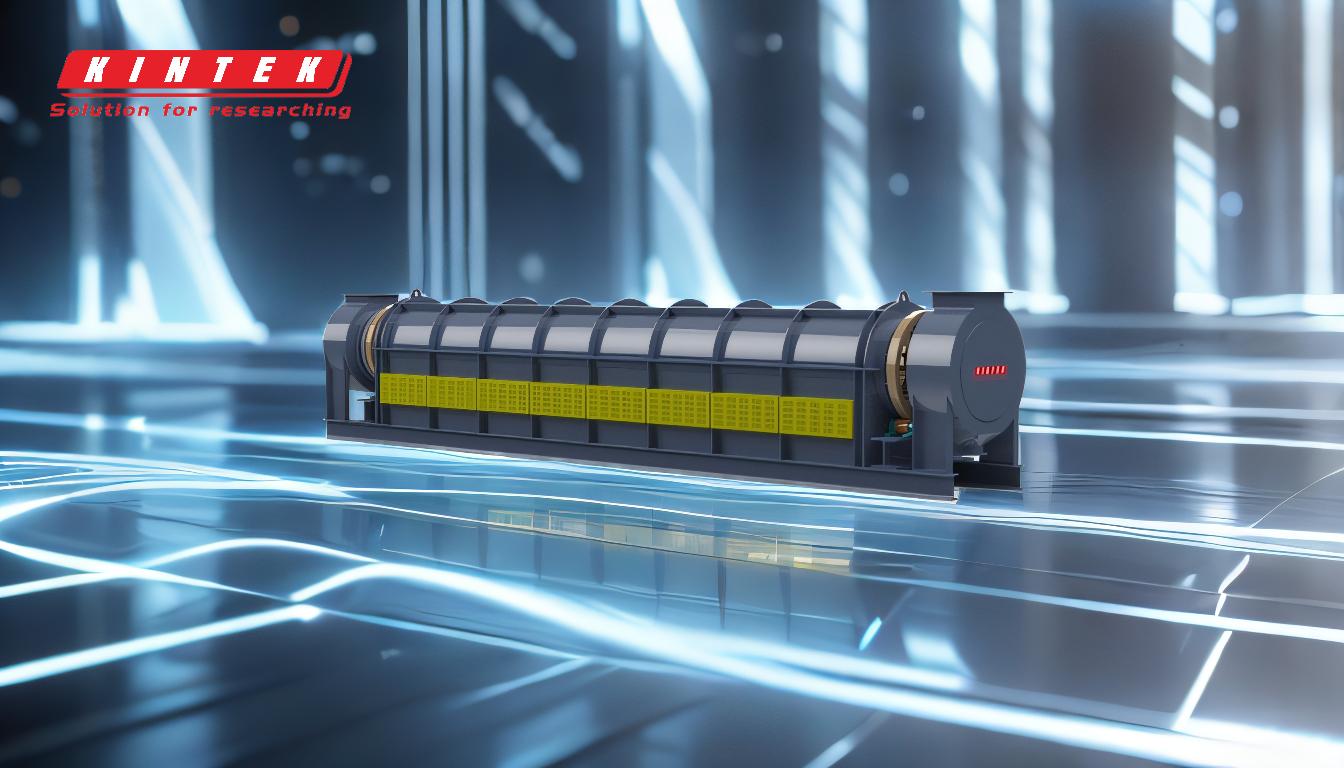
-
Uniform Heating and Material Mixing
- The rotational motion of the rotary furnace ensures that materials are fully mixed, reducing temperature gradients and improving heat treatment effects.
- This uniform heating is critical for processes like sintering, where consistent temperature distribution is necessary to achieve desired material properties such as density, strength, and corrosion resistance.
-
Flexible Tilt and Rotation Mechanism
- The furnace can tilt between 0 and 30 degrees and rotate 360 degrees, allowing operators to adjust the material's position based on experimental or operational needs.
- This flexibility enhances material handling and operational efficiency, making it easier to achieve precise material placement and processing.
-
Improved Gas Diffusion and Heat Treatment Efficiency
- The continuous movement of materials in the furnace ensures that the entire surface area is exposed to the atmosphere, improving gas diffusion and reducing gas consumption.
- This feature is particularly beneficial for processes like oxidation, reduction, and chemical reactions, where consistent exposure to reactive gases is essential.
-
Wide Range of Applications
- Rotary furnaces are used for sintering ceramics and metal powders, preparing coatings, conducting chemical reactions, and performing heat treatment and annealing of metal materials.
- They are also employed in high-temperature oxidation and reduction reactions, as well as for calcining granular or powder materials at temperatures up to 1100 ℃.
-
Accurate Temperature Control
- Equipped with advanced computer control systems, rotary furnaces provide precise temperature regulation, ensuring high-quality heating and consistent product outcomes.
- This accuracy is crucial for applications like catalyst preparation and material synthesis, where temperature stability directly impacts the final product's properties.
-
Enhanced Product Homogeneity
- The consistent temperature profile maintained in rotary furnaces improves product uniformity, which is vital for achieving desired material characteristics in industrial and research settings.
- This homogeneity is particularly important in processes like coating preparation and chemical synthesis, where even slight variations can affect performance.
-
Key Components and Design Features
- The main components of a rotary furnace include the furnace body, furnace lining, drive gear, and internal heat source.
- These components work together to ensure efficient heat transfer, durability, and operational reliability, making the furnace suitable for demanding industrial environments.
In summary, the rotary furnace is a highly adaptable and efficient tool for a wide range of thermal processing applications. Its ability to provide uniform heating, precise temperature control, and consistent material exposure makes it invaluable in industries requiring high-quality material modification and preparation.
Summary Table:
Feature | Benefits |
---|---|
Uniform Heating & Mixing | Reduces temperature gradients, improves heat treatment effects |
Flexible Tilt & Rotation | Enhances material handling and precise placement |
Improved Gas Diffusion | Ensures consistent exposure to atmosphere, reduces gas consumption |
Wide Range of Applications | Suitable for sintering, annealing, chemical reactions, and coating prep |
Accurate Temperature Control | Ensures high-quality heating and consistent product outcomes |
Enhanced Product Homogeneity | Improves material uniformity for better performance |
Durable Design & Components | Ensures reliability and efficiency in demanding industrial environments |
Ready to enhance your material processing? Contact us today to find the perfect rotary furnace for your needs!