Rolling mills operate on the principle of reducing the thickness of metal ingots or other materials by passing them between two rotating rollers. The gap between these rollers is set to be smaller than the initial thickness of the material, which ensures that the material is compressed and elongated as it passes through. This process is driven by the friction generated between the rollers and the material, with the rollers rotating in opposite directions. In some cases, such as in mixing mills, one roller may rotate faster than the other to create additional shearing forces, which are useful for mixing materials like rubber.
Key Points Explained:
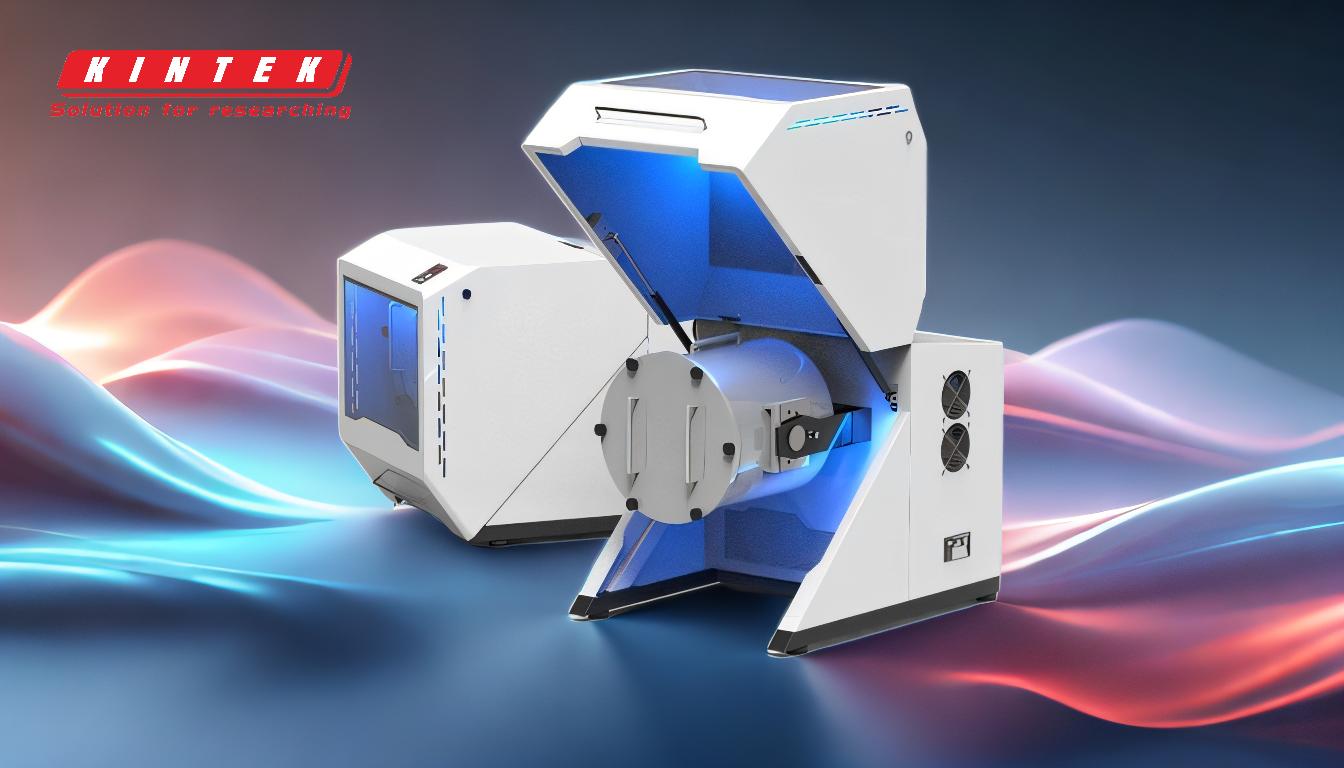
-
Basic Working Principle:
- Rolling mills function by passing a material, typically a metal ingot, between two rotating rollers.
- The gap between the rollers is intentionally set to be smaller than the initial thickness of the material, ensuring that the material is compressed and elongated as it passes through.
-
Role of Rollers:
- The two rollers rotate in opposite directions, which helps in pulling the material through the gap.
- The friction between the rollers and the material is crucial for the forward motion of the material.
-
Material Compression and Elongation:
- As the material passes through the smaller gap, it undergoes compression, which reduces its thickness.
- Simultaneously, the material is elongated, which increases its length while maintaining its volume.
-
Shearing Forces in Mixing Mills:
- In some applications, such as mixing mills used for rubber, one roller rotates faster than the other.
- This speed difference generates shearing forces in the nip (the gap between the rollers), which are essential for mixing and homogenizing the material.
-
Applications of Rolling Mills:
- Rolling mills are widely used in the metal industry for shaping and reducing the thickness of metal sheets, bars, and other forms.
- They are also used in the rubber and plastic industries for mixing and homogenizing materials.
-
Importance of Friction:
- Friction between the rollers and the material is a critical factor in the rolling process.
- It ensures that the material is pulled through the rollers and undergoes the necessary deformation.
-
Adjustability of Roller Gap:
- The gap between the rollers can be adjusted to achieve different levels of thickness reduction.
- This adjustability allows for precise control over the final dimensions of the material.
-
Energy Efficiency:
- Rolling mills are designed to be energy-efficient, as the process relies on the mechanical energy of the rollers rather than additional heat or chemical energy.
-
Material Properties:
- The effectiveness of the rolling process depends on the properties of the material being rolled, such as its ductility and yield strength.
- Materials with higher ductility are more easily deformed by the rolling process.
-
Safety Considerations:
- Rolling mills must be operated with safety precautions, as the high forces involved can pose risks to operators.
- Proper maintenance and safety protocols are essential to prevent accidents.
By understanding these key points, one can appreciate the intricate working principles of rolling mills and their applications in various industries.
Summary Table:
Key Aspect | Description |
---|---|
Working Principle | Material passes through two rotating rollers with a smaller gap for compression. |
Role of Rollers | Rotate in opposite directions, using friction to pull and deform the material. |
Compression & Elongation | Material thickness reduces while length increases, maintaining volume. |
Shearing Forces | Mixing mills use differing roller speeds to create shearing for homogenization. |
Applications | Used in metal, rubber, and plastic industries for shaping and mixing materials. |
Adjustable Roller Gap | Allows precise control over material thickness reduction. |
Energy Efficiency | Relies on mechanical energy, making it energy-efficient. |
Material Properties | Effectiveness depends on ductility and yield strength of the material. |
Safety Considerations | High forces require proper maintenance and safety protocols. |
Ready to optimize your material processing? Contact our experts today to learn more about rolling mills!