Thermal activation of activated carbon is a process that involves the use of high temperatures (typically between 800 to 1100 ºC) and an oxidizing gas such as CO2, steam, or air to enhance the porosity and surface area of carbonized material. This process is crucial for creating the highly porous structure that makes activated carbon effective for adsorption applications. The thermal activation process not only increases the surface area but also modifies the surface chemistry of the carbon, making it more suitable for specific adsorption tasks. This method is widely used in various industries, including water purification, air filtration, and chemical recovery, due to its ability to produce high-quality activated carbon with tailored properties.
Key Points Explained:
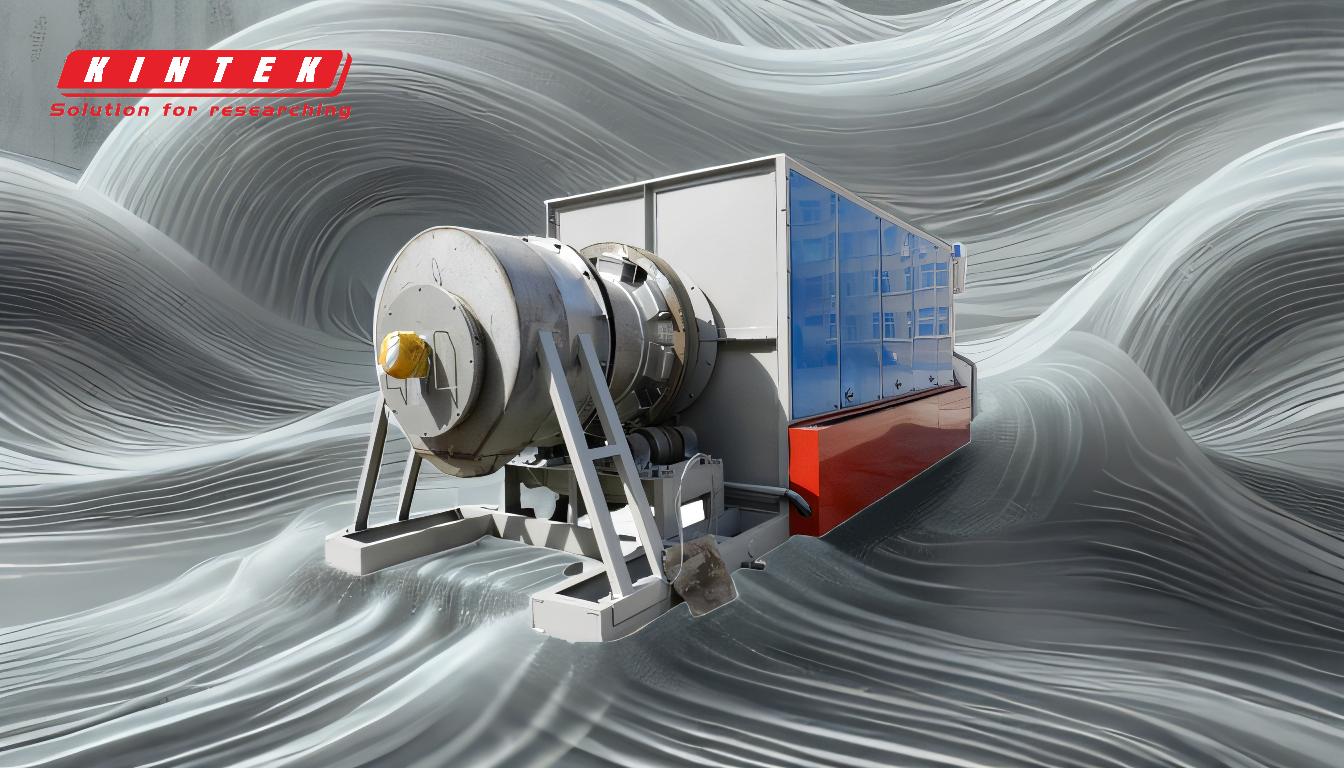
-
Definition of Thermal Activation:
- Thermal activation is a process that enhances the porosity and surface area of carbonized materials by exposing them to high temperatures in the presence of an oxidizing gas.
- This process is essential for creating activated carbon, which is widely used for adsorption due to its high surface area and porosity.
-
Temperature Range:
- The process typically occurs within a temperature range of 800 to 1100 ºC.
- This high temperature is necessary to break down the carbon structure and create a network of pores.
-
Role of Oxidizing Gases:
- Oxidizing gases such as CO2, steam, or air are used during the activation process.
- These gases react with the carbon at high temperatures, creating and enlarging pores within the carbon structure.
-
Impact on Surface Area and Porosity:
- The primary goal of thermal activation is to increase the surface area and porosity of the carbon.
- A higher surface area allows for more adsorption sites, making the activated carbon more effective for capturing impurities.
-
Modification of Surface Chemistry:
- Thermal activation also alters the surface chemistry of the carbon.
- This modification can make the carbon more suitable for specific applications, such as the removal of certain pollutants from water or air.
-
Applications of Thermally Activated Carbon:
- Activated carbon produced through thermal activation is used in various industries, including water purification, air filtration, and chemical recovery.
- Its high adsorption capacity makes it ideal for removing contaminants from liquids and gases.
-
Advantages of Thermal Activation:
- Produces activated carbon with a high degree of porosity and surface area.
- Allows for the customization of carbon properties to suit specific applications.
- Effective in creating carbon with a high adsorption capacity.
-
Considerations for the Process:
- The choice of oxidizing gas and temperature can significantly impact the final properties of the activated carbon.
- Careful control of the activation conditions is necessary to achieve the desired carbon characteristics.
In summary, thermal activation is a critical step in the production of activated carbon, transforming carbonized material into a highly porous and effective adsorbent through the application of high temperatures and oxidizing gases. This process not only enhances the physical properties of the carbon but also tailors its chemical properties to meet specific industrial needs.
Summary Table:
Key Aspect | Details |
---|---|
Definition | Enhances porosity and surface area of carbonized material using high heat. |
Temperature Range | 800 to 1100 ºC |
Oxidizing Gases | CO2, steam, or air |
Impact on Porosity | Increases surface area and creates a porous structure for better adsorption. |
Surface Chemistry | Modifies carbon's surface to suit specific adsorption tasks. |
Applications | Water purification, air filtration, chemical recovery. |
Advantages | High porosity, customizable properties, and superior adsorption capacity. |
Process Considerations | Controlled temperature and gas selection are critical for desired results. |
Discover how thermal activation can optimize your activated carbon—contact our experts today!