Thermal deposition in a vacuum is a process used to deposit thin films of material onto a substrate by heating the source material in a vacuum environment. This method relies on the principle of evaporation, where the source material is heated to its vaporization point, causing it to evaporate and then condense onto the cooler substrate. The vacuum environment is crucial as it minimizes contamination and allows for precise control over the deposition process. This technique is widely used in industries such as electronics, optics, and coatings, where high-quality, uniform thin films are required. The process is versatile, allowing for the deposition of a wide range of materials, including metals, semiconductors, and insulators.
Key Points Explained:
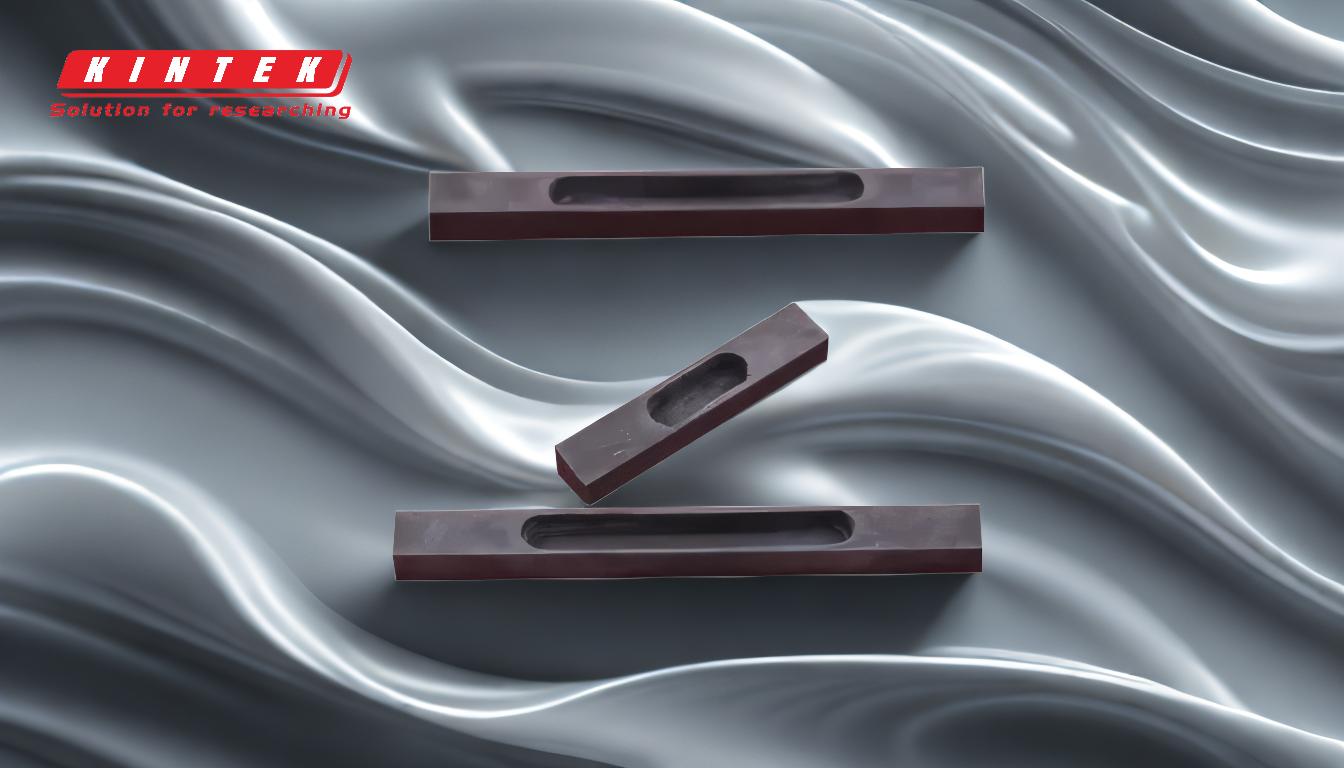
-
Definition and Purpose of Thermal Deposition in a Vacuum:
- Thermal deposition in a vacuum involves heating a material until it evaporates and then condensing the vapor onto a substrate to form a thin film.
- The primary purpose is to create high-quality, uniform thin films that are essential in various applications, such as semiconductor manufacturing, optical coatings, and protective layers.
-
The Role of the Vacuum Environment:
- The vacuum environment is critical in thermal deposition because it reduces the presence of contaminants, such as oxygen and water vapor, which can interfere with the deposition process.
- A vacuum also allows for better control over the deposition rate and the properties of the deposited film, such as thickness and uniformity.
-
Heating Methods in Thermal Deposition:
- The source material is typically heated using methods such as resistive heating, electron beam heating, or laser heating.
- Resistive heating involves passing an electric current through a filament or crucible containing the source material, causing it to heat up and evaporate.
- Electron beam heating uses a focused beam of high-energy electrons to directly heat and vaporize the source material, which is particularly useful for materials with high melting points.
- Laser heating employs a high-power laser to rapidly heat and vaporize the material, offering precise control over the deposition process.
-
Deposition Process and Film Formation:
- Once the source material is vaporized, the atoms or molecules travel through the vacuum chamber and deposit onto the substrate.
- The substrate is usually positioned at a specific distance from the source to ensure uniform deposition.
- The deposited atoms or molecules condense on the substrate, forming a thin film with the desired properties, such as thickness, uniformity, and adhesion.
-
Applications of Thermal Deposition in a Vacuum:
- Electronics: Used to deposit thin films of metals, semiconductors, and insulators in the fabrication of integrated circuits, transistors, and other electronic components.
- Optics: Applied in the production of anti-reflective coatings, mirrors, and optical filters.
- Coatings: Utilized for creating protective and decorative coatings on various materials, including metals, glass, and plastics.
-
Advantages of Thermal Deposition in a Vacuum:
- High Purity: The vacuum environment ensures that the deposited films are free from contaminants, resulting in high-purity coatings.
- Precision Control: The process allows for precise control over film thickness, composition, and uniformity.
- Versatility: A wide range of materials can be deposited using thermal deposition, making it suitable for various applications.
-
Challenges and Limitations:
- Material Limitations: Some materials may be difficult to deposit using thermal deposition due to their high melting points or chemical reactivity.
- Complexity: The process requires specialized equipment and a controlled environment, which can be costly and complex to maintain.
- Scalability: While thermal deposition is effective for small-scale applications, scaling up the process for large-scale production can be challenging.
In summary, thermal deposition in a vacuum is a versatile and precise method for depositing thin films of various materials onto substrates. The vacuum environment plays a crucial role in ensuring the purity and quality of the deposited films, making this technique essential in industries that require high-performance coatings and thin films. Despite some challenges, thermal deposition remains a widely used and effective method for creating high-quality materials in a controlled and precise manner.
Summary Table:
Aspect | Details |
---|---|
Definition | Heating material in a vacuum to evaporate and condense it onto a substrate. |
Purpose | Create high-quality, uniform thin films for various industrial applications. |
Vacuum Role | Minimizes contamination and ensures precise control over deposition. |
Heating Methods | Resistive, electron beam, or laser heating. |
Applications | Electronics, optics, and protective coatings. |
Advantages | High purity, precision control, and versatility. |
Challenges | Material limitations, complexity, and scalability issues. |
Discover how thermal deposition in a vacuum can enhance your projects—contact our experts today!