Heating elements in high-temperature furnaces are critical components designed to withstand extreme temperatures while maintaining efficiency and durability. These elements are typically made from a variety of exotic materials, including metals like platinum, tungsten, molybdenum, and tantalum, as well as non-metallic materials like silicon carbide and graphite. The choice of material depends on the specific temperature requirements of the furnace, with different materials being suitable for different temperature ranges. For instance, resistance wires are used for temperatures below 1200°C, silicon carbon rods for 1300°C to 1400°C, and silicon molybdenum rods for 1400°C to 1700°C. Additionally, industrial furnaces often use iron-chrome aluminum or nickel chrome alloys, which are shaped into various forms like cylindrical, semi-circular, or flat panels.
Key Points Explained:
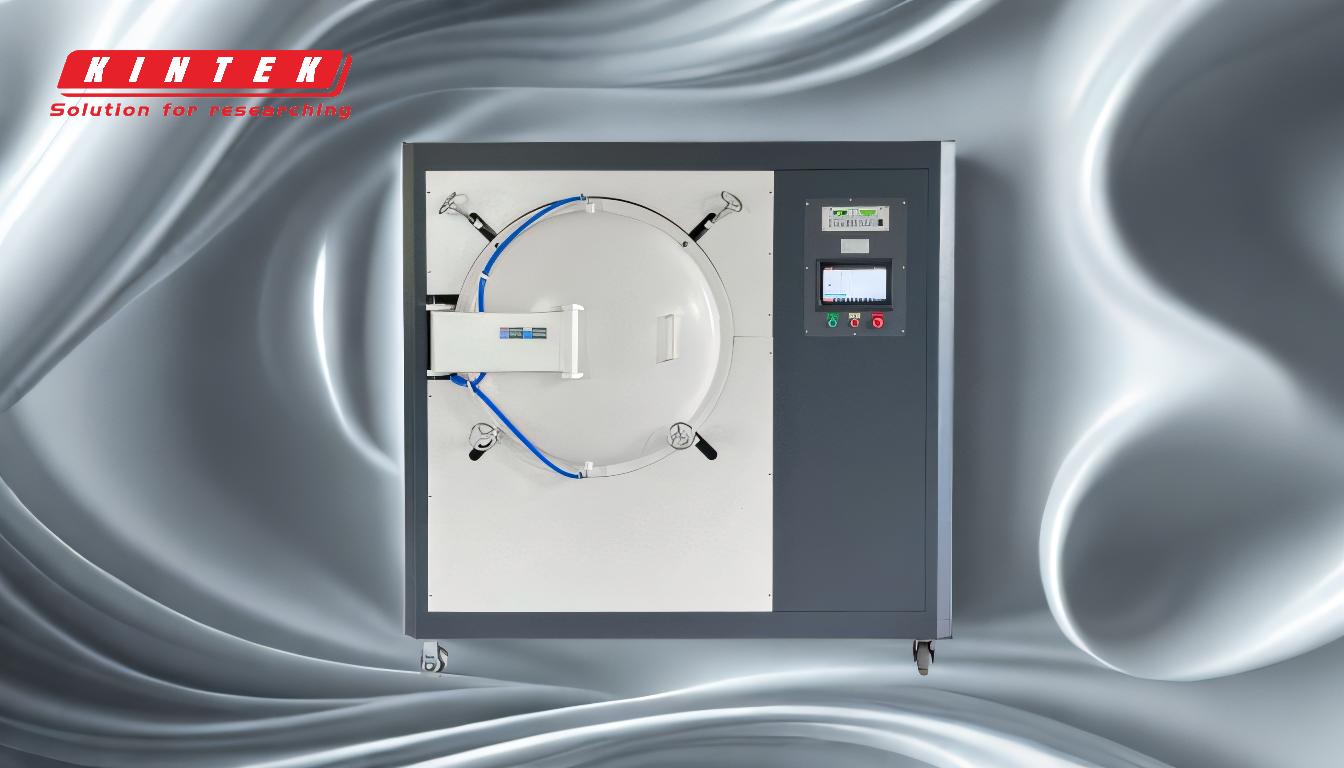
-
Materials Used for Heating Elements:
-
Metallic Alloys:
- Nickel-Chromium Alloys: Commonly used for temperatures below 1200°C due to their good oxidation resistance and high electrical resistivity.
- Iron-Chrome Aluminum Alloys: These are also used for lower temperature ranges and are known for their durability and resistance to oxidation.
- Molybdenum and Tungsten: These metals are used for higher temperature applications, typically above 1200°C, due to their high melting points and excellent thermal conductivity.
- Tantalum and Platinum: These are used in specialized applications where extreme temperatures and corrosion resistance are required.
-
Non-Metallic Materials:
- Silicon Carbide (SiC): Used for temperatures up to 1400°C, silicon carbide offers excellent thermal shock resistance and high thermal conductivity.
- Graphite: Suitable for very high temperatures, especially in vacuum furnaces, graphite is lightweight and has excellent thermal properties.
- Molybdenum Disilicide (MoSi2): This material is used for temperatures up to 1700°C and is known for its high oxidation resistance at elevated temperatures.
-
Metallic Alloys:
-
Temperature Ranges and Material Suitability:
- Below 1200°C: Resistance wires made from nickel-chromium or iron-chrome aluminum alloys are typically used. These materials are cost-effective and provide sufficient performance for lower temperature applications.
- 1300°C to 1400°C: Silicon carbon rods are commonly used. These rods are made from silicon carbide and are ideal for this temperature range due to their thermal stability and resistance to thermal shock.
- 1400°C to 1700°C: Silicon molybdenum rods are employed. These rods are made from molybdenum disilicide and are capable of withstanding very high temperatures while maintaining structural integrity.
-
Forms and Shapes of Heating Elements:
- Cylindrical, Semi-Circular, or Flat Panels: Industrial furnaces often use heating elements shaped into these forms to ensure even heat distribution and efficient energy use. The shape can also affect the heating element's lifespan and performance.
- Lightweight Curved Graphite or Molybdenum Strip: These forms are particularly useful in vacuum furnaces where weight and thermal efficiency are critical considerations.
-
Special Considerations for Vacuum Furnaces:
- Pure Metals: In high-temperature vacuum furnaces, especially those operating above 1200°C, heating elements are often made from pure metals like tungsten, tantalum, and molybdenum. These materials are chosen for their high melting points and ability to maintain performance in a vacuum environment.
- Graphite: Graphite is also a popular choice for vacuum furnaces due to its excellent thermal properties and lightweight nature.
-
Oxidation and Corrosion Resistance:
- Oxidation Resistance: Materials like molybdenum disilicide and silicon carbide are chosen for their ability to resist oxidation at high temperatures, which is crucial for maintaining the longevity and efficiency of the heating elements.
- Corrosion Resistance: In environments where corrosive gases or chemicals are present, materials like platinum and tantalum are preferred due to their superior corrosion resistance.
-
Thermal Conductivity and Shock Resistance:
- Thermal Conductivity: High thermal conductivity is essential for efficient heat transfer. Materials like graphite and silicon carbide are excellent in this regard.
- Thermal Shock Resistance: The ability to withstand rapid temperature changes without cracking or degrading is crucial. Silicon carbide and molybdenum disilicide are known for their excellent thermal shock resistance.
In summary, the selection of heating elements for high-temperature furnaces involves a careful consideration of the operating temperature, material properties, and the specific requirements of the application. The choice of material and form can significantly impact the performance, efficiency, and lifespan of the furnace.
Summary Table:
Material Type | Common Materials | Temperature Range | Key Properties |
---|---|---|---|
Metallic Alloys | Nickel-Chromium, Iron-Chrome Aluminum | Below 1200°C | Oxidation resistance, high electrical resistivity, durability |
Metallic Alloys | Molybdenum, Tungsten | Above 1200°C | High melting points, excellent thermal conductivity |
Specialized Metals | Tantalum, Platinum | Extreme temperatures | Corrosion resistance, high-temperature performance |
Non-Metallic | Silicon Carbide (SiC) | Up to 1400°C | Thermal shock resistance, high thermal conductivity |
Non-Metallic | Graphite | Very high temperatures | Lightweight, excellent thermal properties |
Non-Metallic | Molybdenum Disilicide (MoSi2) | Up to 1700°C | High oxidation resistance, thermal stability |
Need help selecting the right heating elements for your furnace? Contact our experts today for personalized advice!