Vacuum arc melting (VAM), also known as vacuum arc remelting (VAR), is an advanced metallurgical process used to refine and produce high-quality metal alloys. This technique involves melting a metal electrode under a vacuum or inert gas atmosphere using a direct current (DC) electric arc. The molten metal droplets solidify in a water-cooled copper mold, resulting in a refined ingot with improved purity, microstructure, and mechanical properties. The process is particularly valued for its ability to remove dissolved gases, reduce impurities, and achieve directional solidification, making it ideal for producing materials used in aerospace, medical, and energy industries.
Key Points Explained:
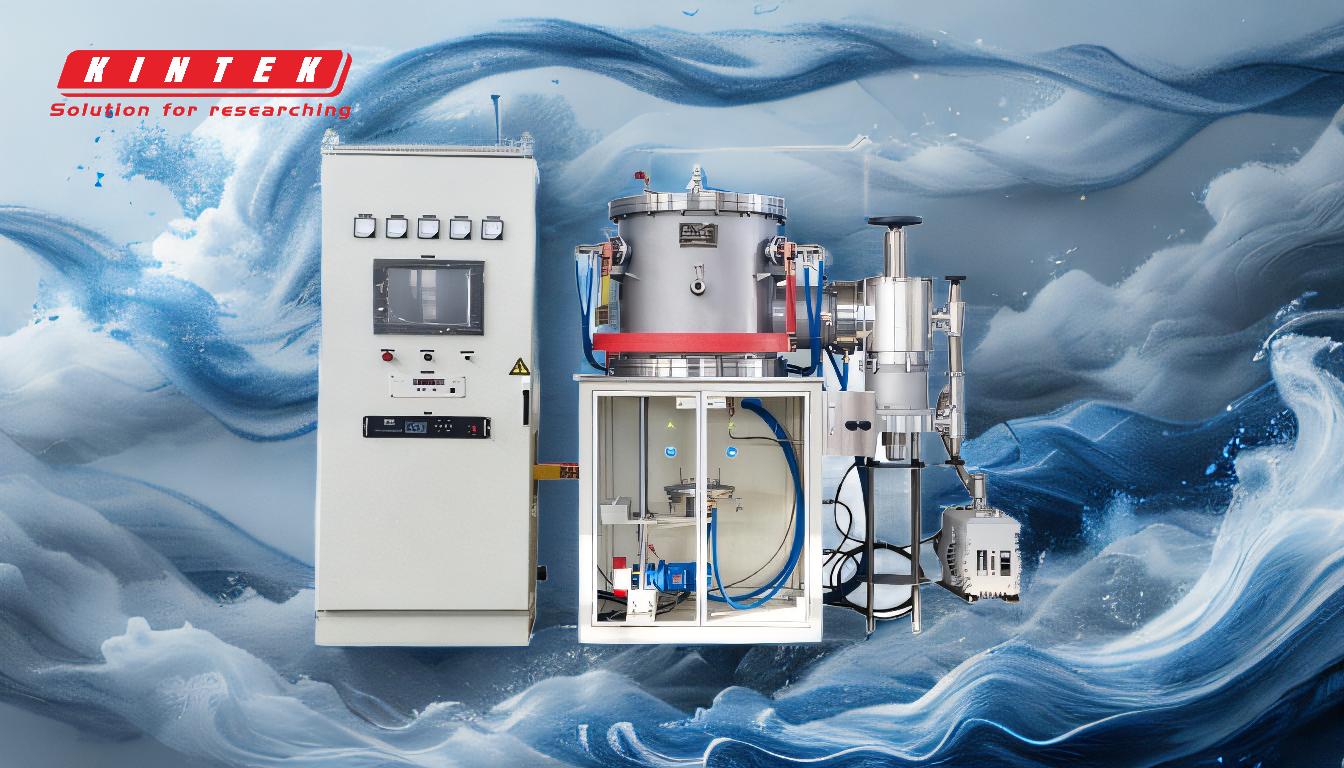
-
Process Overview:
- Vacuum arc melting involves melting a metal electrode using a DC electric arc in a vacuum or inert gas environment.
- The molten metal droplets solidify in a water-cooled copper mold, ensuring controlled solidification and refining.
-
Key Advantages:
- Removal of Dissolved Gases: The vacuum environment eliminates gases like hydrogen, nitrogen, and carbon dioxide, which can degrade material properties.
- Reduction of Trace Elements: High vapor pressure elements are removed, improving the purity of the final product.
- Improved Oxide Cleanliness: Non-metallic inclusions are reduced, enhancing the material's mechanical performance.
- Directional Solidification: Solidification occurs from the bottom up, minimizing macro-segregation and reducing micro-segregation, leading to a more uniform microstructure.
- Low Energy Input: VAR is energy-efficient compared to other remelting processes.
- Ceramic-Free Melting: The absence of ceramic materials eliminates potential contamination.
-
Applications:
- VAR is widely used in industries requiring high-performance materials, such as aerospace (turbine blades, engine components), medical (implants, surgical tools), and energy (nuclear reactor components).
- It is particularly suited for producing superalloys, titanium alloys, and specialty steels.
-
Comparison with Other Melting Techniques:
- Vacuum Induction Melting (VIM): While VIM also operates under a vacuum or inert gas, it uses induction heating rather than an electric arc. VIM offers precise control over alloy composition and microstructure but may not achieve the same level of directional solidification as VAR.
- Electroslag Remelting (ESR): ESR uses a slag layer to refine the metal, but it lacks the vacuum environment of VAR, making it less effective at removing dissolved gases.
-
Technical Details:
- The DC arc generates temperatures of up to 5000K, enabling the removal of impurities and refining the metal.
- The water-cooled copper mold ensures rapid solidification, which helps in achieving a fine-grained microstructure.
- The process allows for precise control over the solidification and crystallization process, resulting in high-quality ingots with low segregation and high density.
-
Economic and Operational Considerations:
- VAR is cost-effective for producing high-value materials due to its energy efficiency and ability to produce high-quality ingots.
- The process is stable, reliable, and suitable for both research and large-scale production.
-
Future Trends:
- Ongoing advancements in VAR technology focus on improving process control, reducing energy consumption, and expanding the range of alloys that can be processed.
- The integration of automation and real-time monitoring systems is enhancing the precision and efficiency of the process.
In summary, vacuum arc melting is a sophisticated and highly effective technique for producing high-quality metal alloys with superior purity, microstructure, and mechanical properties. Its ability to operate under vacuum or inert gas, combined with precise control over solidification, makes it indispensable in industries requiring advanced materials.
Summary Table:
Aspect | Details |
---|---|
Process Overview | Melting a metal electrode under vacuum/inert gas using a DC electric arc. |
Key Advantages | Removes dissolved gases, reduces impurities, and ensures directional solidification. |
Applications | Aerospace, medical, and energy industries; superalloys, titanium alloys. |
Comparison with VIM/ESR | Superior to VIM in directional solidification; better than ESR in gas removal. |
Technical Details | DC arc up to 5000K; water-cooled copper mold for rapid solidification. |
Economic Benefits | Cost-effective, energy-efficient, and suitable for large-scale production. |
Learn how vacuum arc melting can transform your material production—contact our experts today!