The vacuum coating process is a sophisticated thin-film deposition technique used to apply protective or functional layers to various substrates. It involves creating a vacuum environment to eliminate air and gases, preparing the substrate, and depositing a thin layer of material through evaporation, sputtering, or chemical reactions. This process is widely used in industries such as automotive, electronics, and optics to enhance properties like hardness, wear resistance, and corrosion protection. The key steps include vacuum creation, substrate preparation, material deposition, and post-deposition cooling. Common methods include physical vapor deposition (PVD) and chemical vapor deposition (CVD), each offering unique advantages for specific applications.
Key Points Explained:
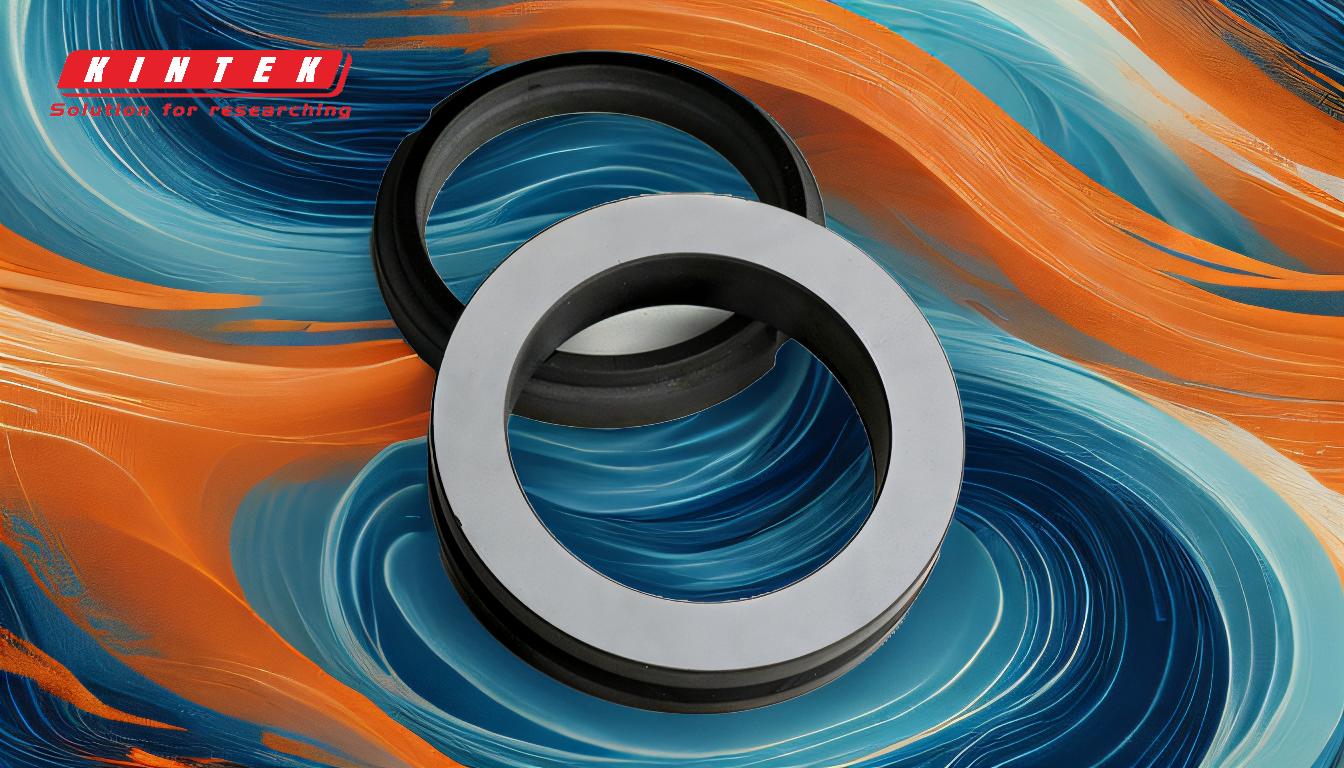
-
Vacuum Environment Creation:
- The process begins by creating a vacuum in a specialized chamber to remove air and gases that could interfere with the deposition process. This ensures a clean environment for the coating material to adhere uniformly to the substrate.
-
Substrate Preparation:
- The substrate, or the object to be coated, is thoroughly cleaned and treated to remove any contaminants. This step is crucial for ensuring strong adhesion and a high-quality coating.
-
Coating Material Deposition:
- The coating material is either evaporated or sputtered onto the substrate. In evaporation, the material is heated until it turns into vapor, which then condenses on the substrate. In sputtering, ions are used to knock atoms off a target material, which then deposit onto the substrate.
-
Physical Vapor Deposition (PVD):
- PVD is a common vacuum coating method where the coating material is vaporized or ionized in the vacuum chamber using thermal energy or plasma. This method is particularly effective for creating thin, durable layers of metallic or ceramic materials.
-
Chemical Vapor Deposition (CVD):
- CVD involves chemical reactions to deposit a solid material from a gas phase. This method is used for more complex coatings and can produce films with excellent uniformity and conformality.
-
Post-Deposition Process:
- After the coating is applied, the chamber is cooled down and vented. This step ensures the coating solidifies properly and adheres well to the substrate.
-
Applications and Benefits:
- Vacuum coating is used in various industries to enhance the properties of materials. For example, it can improve hardness, wear resistance, and corrosion protection. Common applications include coatings for automotive parts, electronic components, and optical lenses.
-
Components of a Vacuum Coating Machine:
- A vacuum coating machine consists of several key components, including the vacuum chamber, vacuum obtaining part, vacuum measurement part, power supply part, process gas input system, mechanical transmission part, heating and temperature measurement equipment, ion evaporation and sputtering source, and water cooling system. Each component plays a vital role in the efficient operation of the machine.
By understanding these key points, one can appreciate the complexity and precision involved in the vacuum coating process, making it a valuable technology for a wide range of industrial applications.
Summary Table:
Key Steps | Description |
---|---|
Vacuum Environment Creation | Removes air and gases for a clean deposition environment. |
Substrate Preparation | Cleans and treats the substrate for strong adhesion and high-quality coatings. |
Coating Material Deposition | Deposits material via evaporation, sputtering, or chemical reactions. |
PVD (Physical Vapor Deposition) | Vaporizes or ionizes materials for thin, durable metallic/ceramic layers. |
CVD (Chemical Vapor Deposition) | Uses chemical reactions for uniform, conformal coatings. |
Post-Deposition Process | Cools and vents the chamber to solidify and adhere the coating. |
Applications | Enhances properties in automotive, electronics, and optics industries. |
Discover how vacuum coating can transform your materials—contact our experts today!