Vacuum deposition, also known as vacuum thermal evaporation (VTE), is a physical vapor deposition (PVD) technique used to create thin films of materials on substrates. This process involves heating a source material in a high-vacuum environment until it evaporates or sublimates, forming a vapor that condenses onto a substrate to form a thin film. VTE is widely used in industries for applications such as corrosion-resistant coatings, optical films, semiconductor devices, solar cells, and more. The process is favored for its simplicity, precision, and ability to produce high-quality coatings with minimal contamination.
Key Points Explained:
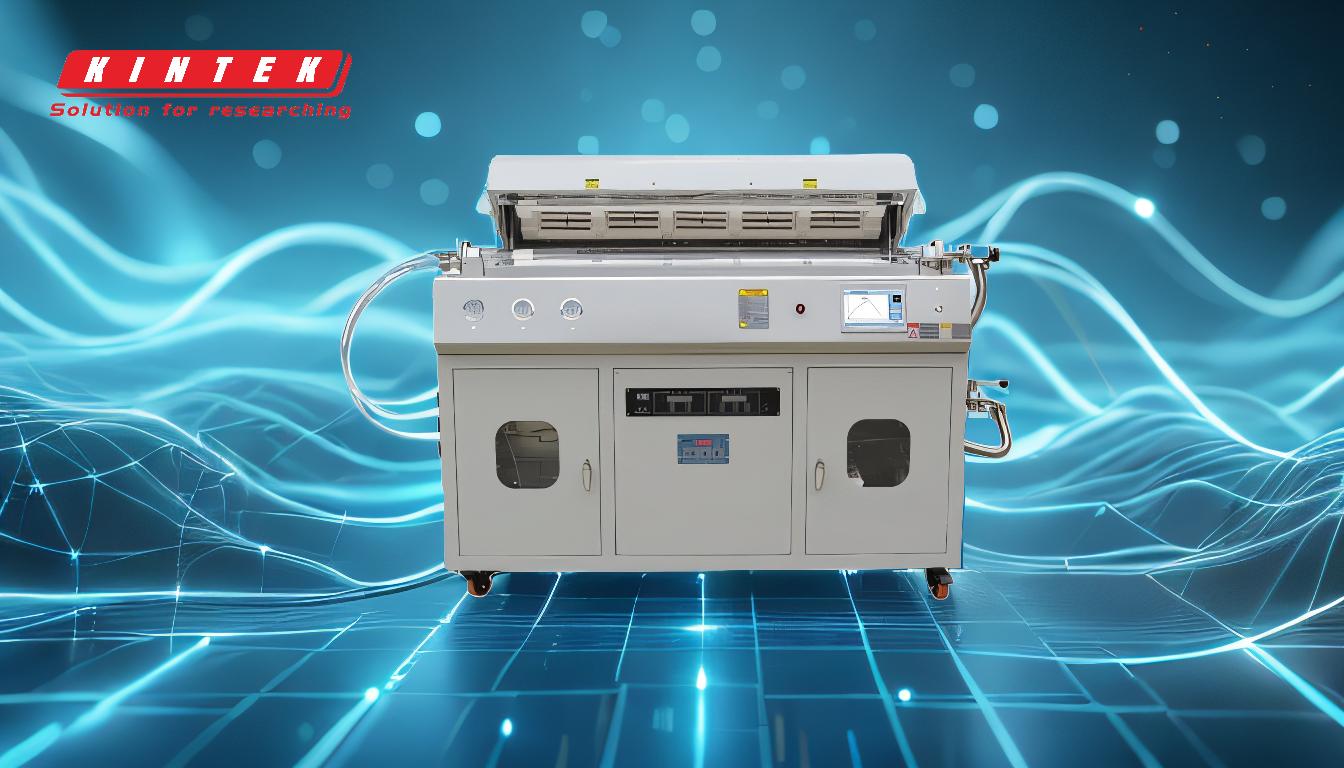
-
Definition and Process of Vacuum Deposition (VTE):
- Vacuum deposition, or vacuum thermal evaporation (VTE), is a physical vapor deposition (PVD) method where a source material is heated in a high-vacuum environment to produce a vapor. This vapor then condenses onto a substrate, forming a thin film.
- The process involves two main steps: evaporation of the source material and subsequent condensation onto the substrate. The high-vacuum environment minimizes gas collisions and unwanted reactions, ensuring a clean and precise deposition.
-
Applications of Vacuum Deposition:
- Vacuum deposition is used in a wide range of industries for various applications, including:
- Corrosion-resistant coatings: Protects substrates from environmental degradation.
- Optical films: Used in lenses, mirrors, and other optical components.
- Semiconductor devices: Essential for creating thin films in electronic components.
- Solar cells: Enhances efficiency and durability of photovoltaic cells.
- Decorative coatings: Provides aesthetic finishes on consumer products.
- Wear-resistant coatings: Improves the durability of mechanical parts.
- The versatility of vacuum deposition makes it a critical technology in modern manufacturing and material science.
- Vacuum deposition is used in a wide range of industries for various applications, including:
-
Advantages of Vacuum Deposition:
- High purity: The high-vacuum environment reduces contamination, resulting in high-quality films.
- Precision: Allows for precise control over film thickness and composition.
- Versatility: Can deposit a wide range of materials, including metals, alloys, and compounds.
- Scalability: Suitable for both small-scale laboratory research and large-scale industrial production.
-
Vacuum Heat Treatment in Deposition:
- The process relies heavily on vacuum heat treatment to evaporate the source material. Heating the material to high temperatures causes it to melt and then evaporate or sublimate, forming a vapor that can be deposited onto the substrate.
- The vacuum environment is crucial as it prevents oxidation and other chemical reactions that could degrade the quality of the deposited film.
-
Types of Coatings Produced:
- Vacuum deposition is used to create various types of coatings, including:
- Optical interference coatings: Used in anti-reflective coatings and filters.
- Mirror coatings: Enhances reflectivity for optical and decorative purposes.
- Permeation barrier films: Protects flexible packaging materials from moisture and gases.
- Electrically conducting films: Essential for electronic and semiconductor applications.
- Corrosion-protective coatings: Extends the lifespan of metallic components.
- Vacuum deposition is used to create various types of coatings, including:
-
Process Considerations:
- Line of sight deposition: The process coats everything within the line of sight of the source material, which can limit uniformity on complex geometries.
- Material selection: The choice of source material depends on the desired properties of the final film, such as conductivity, reflectivity, or durability.
- Vacuum level: Maintaining a high vacuum is critical to ensure minimal gas collisions and high-quality film deposition.
In summary, vacuum deposition or vacuum thermal evaporation (VTE) is a versatile and precise method for creating thin films with a wide range of applications. Its reliance on vacuum heat treatment ensures high-quality, contamination-free coatings, making it a cornerstone of modern material science and industrial manufacturing.
Summary Table:
Aspect | Details |
---|---|
Definition | Physical vapor deposition (PVD) method to create thin films in a vacuum. |
Process | Heating a source material to evaporate, then condensing it onto a substrate. |
Applications | Corrosion-resistant coatings, optical films, semiconductors, solar cells. |
Advantages | High purity, precision, versatility, and scalability. |
Key Considerations | Line of sight deposition, material selection, and vacuum level. |
Interested in leveraging vacuum deposition for your projects? Contact us today to learn more!