When it comes to casting, the type of furnace used depends on the specific requirements of the casting process, the metal being melted, and the desired quality of the final product. Furnaces used in casting must provide precise temperature control, efficient energy use, and the ability to handle the specific properties of the metal being cast. Common types include induction furnaces, crucible furnaces, reverberatory furnaces, and muffle furnaces, each suited to different applications and scales of operation.
Key Points Explained:
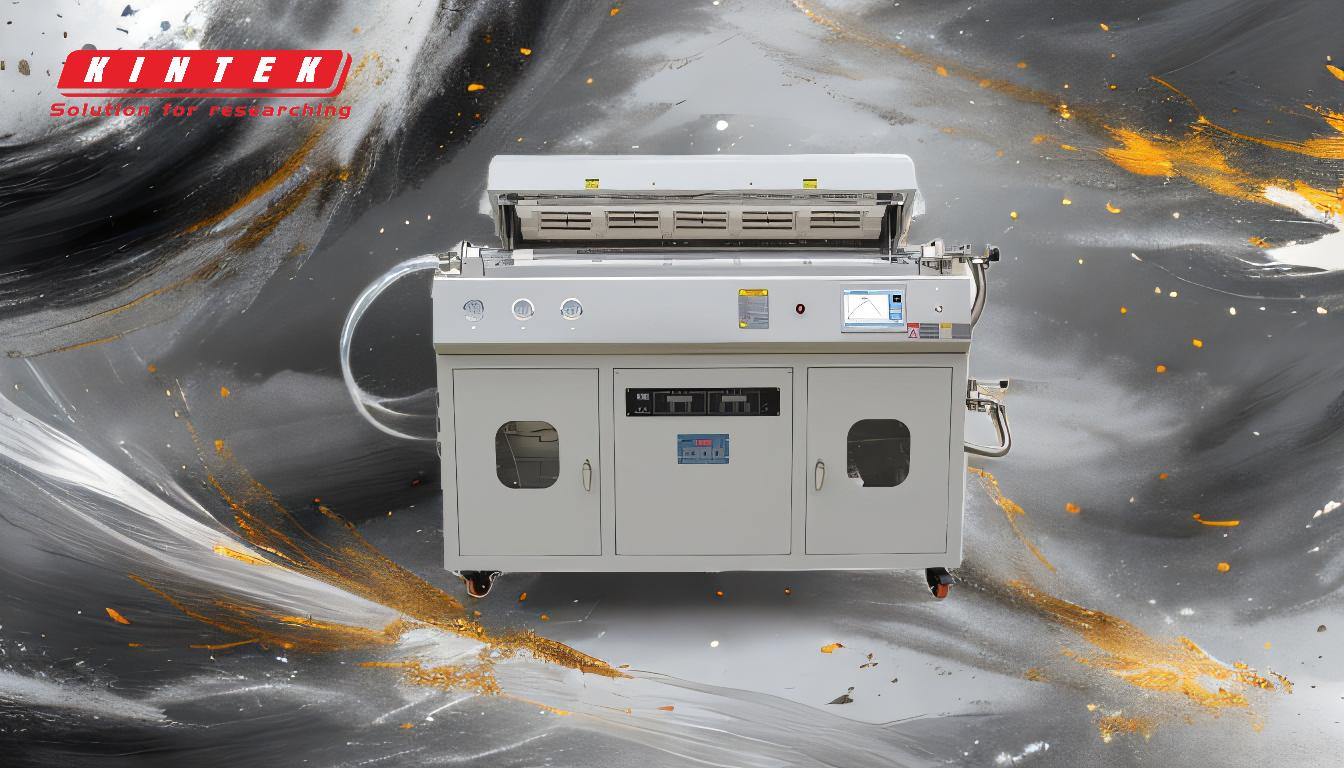
-
Induction Furnaces:
- Induction furnaces, such as the channel induction furnace, are widely used in casting due to their ability to provide controlled heating and stirring action. These furnaces consist of a refractory-lined upper case for holding molten metal and a lower case with an induction coil that generates heat and a magnetic field. The molten metal circulates within the upper case, ensuring uniform heating and alloy mixing, which is ideal for melting or holding various alloys. This type of furnace is particularly beneficial for processes requiring precise temperature control and minimal contamination.
-
Crucible Furnaces:
- Crucible furnaces are commonly used in permanent mould casting and high-pressure die casting. They are available in gas-fired or electric resistance heated configurations. These furnaces are versatile, making them suitable for small to medium-sized operations or jobbing shops where frequent alloy changes are required. For applications demanding high metal quality, such as in electric motor rotor casting, electric resistance heated 'globar' aluminum wet bath reverberatory furnaces are preferred due to their high energy efficiency (60-65%) and low melt losses (less than 3%).
-
Reverberatory Furnaces:
- Reverberatory furnaces, particularly the central reverberatory melting furnaces, are used in high-pressure die casting and other large-scale operations. These furnaces are designed for efficient melting and holding of large quantities of metal. They are often gas-fired or electrically heated and are known for their ability to maintain consistent temperatures, making them suitable for applications where metal quality is critical.
-
Muffle Furnaces:
- While muffle furnaces are not typically used for casting, they are worth mentioning for their specialized applications. These furnaces are equipped with ceramic fiber insulation, allowing for faster heating ramp rates. They are primarily used for gravimetric analysis, sintering, and sample volatility studies, rather than for melting metals.
-
Atmosphere Furnaces:
- Atmosphere furnaces combine features of box and tube furnaces and are ideal for experiments requiring specific atmospheric conditions. Although not directly used for casting, they are relevant in research and development settings where controlled environments are necessary for material testing and large-scale sample manufacturing.
-
Selection Criteria:
- The choice of furnace for casting depends on factors such as the type of metal, scale of operation, energy efficiency, and required metal quality. For example, induction furnaces are preferred for their stirring action and precise temperature control, while crucible and reverberatory furnaces are chosen for their versatility and efficiency in handling specific alloys.
By understanding the unique features and applications of each furnace type, purchasers can make informed decisions that align with their casting needs, ensuring optimal performance and quality in their operations.
Summary Table:
Furnace Type | Key Features | Applications |
---|---|---|
Induction Furnaces | Precise temperature control, stirring action, minimal contamination | Melting or holding various alloys, processes requiring uniform heating |
Crucible Furnaces | Versatile, gas-fired or electric resistance heated, high energy efficiency | Permanent mould casting, high-pressure die casting, small to medium operations |
Reverberatory Furnaces | Efficient melting, consistent temperatures, gas-fired or electrically heated | High-pressure die casting, large-scale operations |
Muffle Furnaces | Ceramic fiber insulation, faster heating ramp rates | Gravimetric analysis, sintering, sample volatility studies |
Atmosphere Furnaces | Controlled atmospheric conditions, combines box and tube furnace features | Research and development, material testing, large-scale sample manufacturing |
Need help selecting the right furnace for your casting process? Contact our experts today for personalized advice!