Heating elements can fail due to a variety of reasons, primarily related to their exposure to high temperatures and the resulting physical and chemical changes. The main causes include the formation of hot spots, oxidation from intermittent operation, embrittlement due to grain growth, and contamination or corrosion from the surrounding environment. Additionally, overheating from excessive current or poor airflow can lead to failure. Understanding these factors is crucial for both preventing failures and selecting the right heating elements for specific applications.
Key Points Explained:
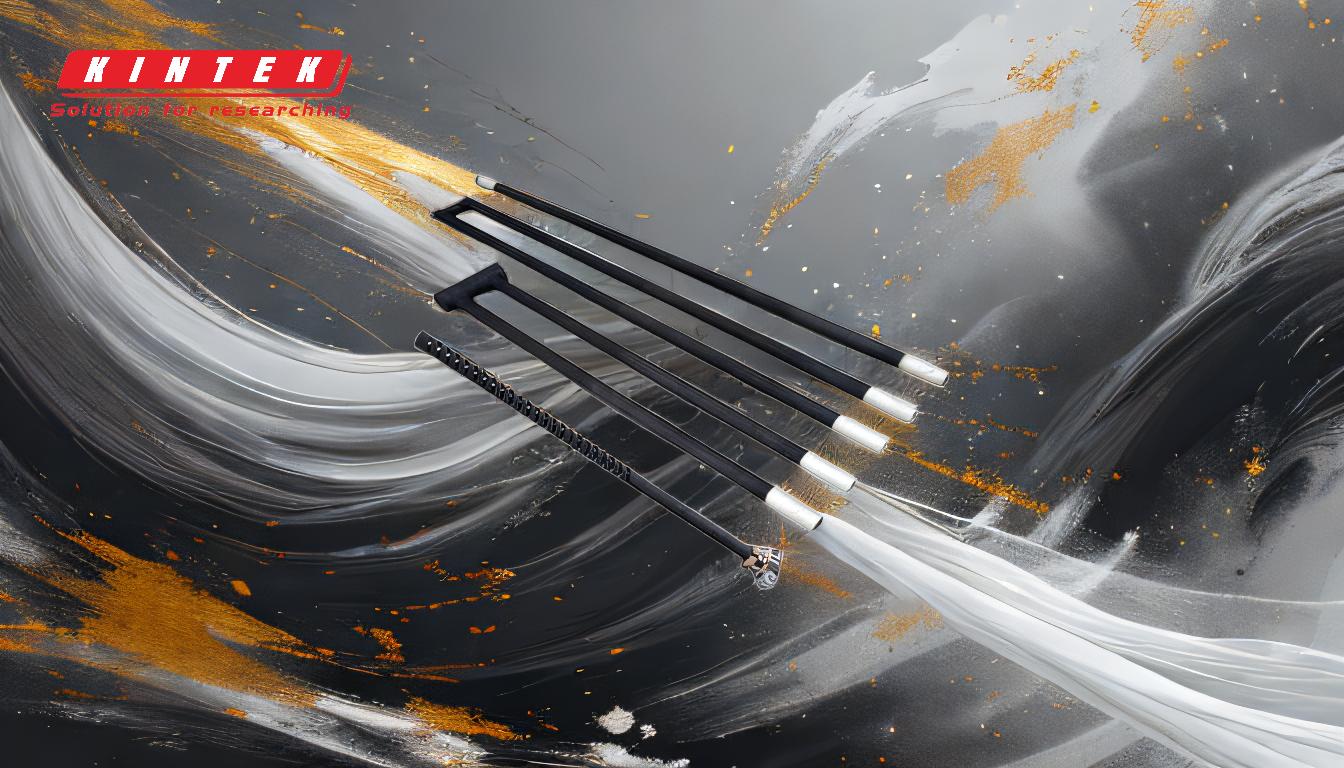
-
Formation of Hot Spots:
- Explanation: Hot spots occur when certain areas of the heating element become significantly hotter than the rest. This can be due to localized oxidation or shielding by supports, which disrupts uniform heat distribution.
- Impact: These hot spots can lead to accelerated degradation in those areas, causing the element to fail prematurely. The uneven temperature distribution can also cause mechanical stress, further exacerbating the problem.
-
Oxidation and Intermittency of Operation:
- Explanation: Frequent heating and cooling cycles cause the oxide layer on the heating element to crack and flake off. This exposes fresh metal to oxidation, accelerating the degradation process.
- Impact: The repeated exposure and oxidation weaken the element over time, making it more susceptible to failure. This is particularly problematic in applications where the heating element is cycled on and off frequently.
-
Embrittlement Due to Grain Growth:
- Explanation: At high temperatures, heating alloys containing iron can undergo grain growth, leading to the formation of large, brittle grains. This makes the material more prone to cracking and breaking.
- Impact: The embrittlement reduces the mechanical strength of the heating element, making it more likely to fail under thermal stress. This is a common issue in high-temperature applications where the element is exposed to prolonged heat.
-
Contamination and Corrosion:
- Explanation: Gases or fumes in the furnace environment can contaminate the heating elements, leading to dry corrosion. This can be particularly aggressive in environments with high levels of reactive gases.
- Impact: Contamination and corrosion can significantly reduce the lifespan of the heating element by causing surface degradation and material loss. This is especially critical in industrial settings where the furnace atmosphere is not tightly controlled.
-
Overheating Due to Excessive Current or Poor Airflow:
- Explanation: Overheating can occur if the heating element is subjected to excessive current or if there is insufficient airflow to dissipate the heat. This can cause the element to expand and contract excessively, leading to mechanical stress.
- Impact: The repeated thermal cycling can cause fatigue in the material, leading to cracks and eventual failure. Ensuring proper current levels and adequate airflow is essential to prevent this type of failure.
Understanding these key points can help in selecting the right heating elements for specific applications and in implementing maintenance practices that extend their lifespan. For example, choosing materials that resist oxidation and grain growth, ensuring uniform heat distribution, and controlling the furnace environment can all contribute to longer-lasting heating elements.
Summary Table:
Cause of Failure | Explanation | Impact |
---|---|---|
Formation of Hot Spots | Localized oxidation or shielding disrupts uniform heat distribution. | Accelerated degradation, mechanical stress, and premature failure. |
Oxidation and Intermittency | Frequent heating/cooling cycles crack the oxide layer, exposing fresh metal. | Weakened element, increased susceptibility to failure. |
Embrittlement Due to Grain Growth | High temperatures cause grain growth, making the material brittle. | Reduced mechanical strength, prone to cracking and breaking. |
Contamination and Corrosion | Gases or fumes cause dry corrosion, leading to surface degradation. | Shortened lifespan, material loss, and failure in uncontrolled environments. |
Overheating | Excessive current or poor airflow causes thermal stress and fatigue. | Cracks and eventual failure due to repeated thermal cycling. |
Need help selecting or maintaining heating elements? Contact our experts today for tailored solutions!