A vacuum furnace is a specialized piece of equipment designed to operate in a vacuum environment, which eliminates oxidation and contamination during high-temperature processes. The materials used in its construction are critical to its performance, as they must withstand extreme temperatures, maintain structural integrity, and ensure efficient heat transfer. Key materials include heating elements like graphite, molybdenum, and tungsten, which are chosen for their high-temperature stability and low vapor pressure. Insulation materials such as graphite wafers, ceramic fiber panels, and reflective shields made of molybdenum or tungsten are also essential for maintaining temperature uniformity and minimizing heat loss. Additionally, the vacuum system, hot zone, and other components are constructed from materials that ensure durability, thermal efficiency, and operational precision.
Key Points Explained:
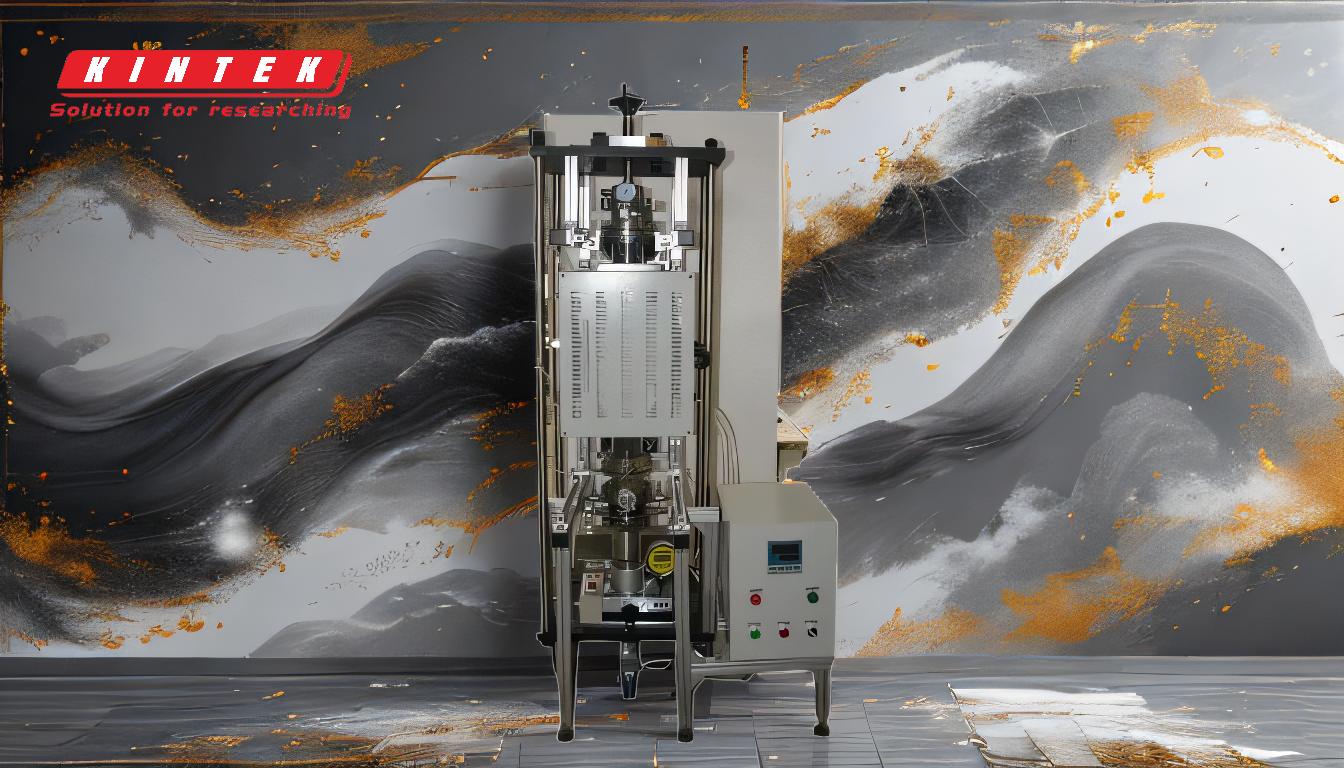
-
Heating Elements in Vacuum Furnaces
- Heating elements are critical for generating and maintaining high temperatures in a vacuum furnace.
- Commonly used materials include:
- Graphite: Known for its durability, low cost, and ability to withstand temperatures up to 2200°C.
- Molybdenum: Offers excellent high-temperature stability (up to 1600°C) and is suitable for clean environments.
- Tungsten: Capable of withstanding temperatures up to 2200°C, making it ideal for extremely high-temperature applications.
- These materials are chosen because they exhibit low vapor pressure, ensuring minimal contamination in the vacuum environment.
-
Insulation Materials
- Insulation is crucial for maintaining temperature uniformity and reducing heat loss.
- Common insulation materials include:
- Graphite Wafers or Ceramic Fiber Panels: These materials provide excellent thermal insulation and are often used in graphite-based hot zones.
- Reflective Shields: Made of molybdenum or tungsten, these shields reflect heat back into the furnace, improving energy efficiency.
- All-metal hot zones use multiple layers of sheet metal with gaps to minimize heat transfer, while graphite-based insulation uses layers of blanket or board with graphite foil for enhanced reflectivity.
-
Hot Zone Construction
- The hot zone is the core area where heating occurs. It is typically made of:
- Graphite: The most common material due to its cost-effectiveness and durability.
- Refractory Metals: Such as molybdenum or tungsten, preferred for applications requiring a clean, contamination-free environment.
- The choice of material depends on the specific application and temperature requirements.
- The hot zone is the core area where heating occurs. It is typically made of:
-
Vacuum System Components
- The vacuum system is essential for creating and maintaining the vacuum environment. Key components include:
- Vacuum Pumps: Used to evacuate air from the chamber.
- Vacuum Valves: Control the flow of gases within the system.
- Vacuum Measuring Instruments: Monitor pressure levels to ensure optimal conditions.
- Pipelines and Other Parts: Ensure the system operates efficiently and reliably.
- The vacuum system is essential for creating and maintaining the vacuum environment. Key components include:
-
Other Key Components
- Furnace Body and Door: Constructed from materials that can withstand high temperatures and maintain a vacuum seal.
- Temperature Control Systems: Advanced computer-controlled systems ensure precise temperature regulation, critical for achieving consistent results.
- Cooling Systems: Water cooling systems prevent overheating and ensure the furnace operates safely.
-
Materials for Gas Quenching
- Certain materials are suitable for gas quenching in a vacuum furnace, including:
- High-Speed Steels: Known for their hardness and wear resistance.
- High Carbon and High Chromium Steels: These materials have a low critical cooling rate for martensite, making them ideal for quenching processes.
- Certain materials are suitable for gas quenching in a vacuum furnace, including:
-
Overall Design and Functionality
- A vacuum furnace is designed to provide precise control over temperature, pressure, and atmosphere.
- The integration of high-quality materials and advanced systems ensures durability, efficiency, and reliability in high-temperature applications.
For more detailed information on vacuum furnaces, visit /topic/vacuum-furnace.
Summary Table:
Component | Materials | Key Properties |
---|---|---|
Heating Elements | Graphite, Molybdenum, Tungsten | High-temperature stability, low vapor pressure, durability |
Insulation Materials | Graphite wafers, ceramic fiber panels, molybdenum/tungsten reflective shields | Thermal insulation, heat reflection, energy efficiency |
Hot Zone Construction | Graphite, molybdenum, tungsten | Cost-effectiveness, durability, contamination-free environment |
Vacuum System | Vacuum pumps, valves, measuring instruments, pipelines | Efficient air evacuation, pressure control, reliable operation |
Other Components | Furnace body, temperature control systems, cooling systems | High-temperature resistance, precise temperature regulation, overheating prevention |
Learn more about how vacuum furnace materials can enhance your high-temperature processes—contact our experts today!