Brazing is a process that involves joining metals by melting and flowing a filler metal into the joint, which has a lower melting point than the adjoining metals. While many metals can be brazed, certain metals present challenges due to their properties. For instance, cast iron, chromium, and tungsten are difficult to braze because of their brittleness and high melting points. This summary will explore why these metals are problematic for brazing and provide a detailed explanation of the key factors involved.
Key Points Explained:
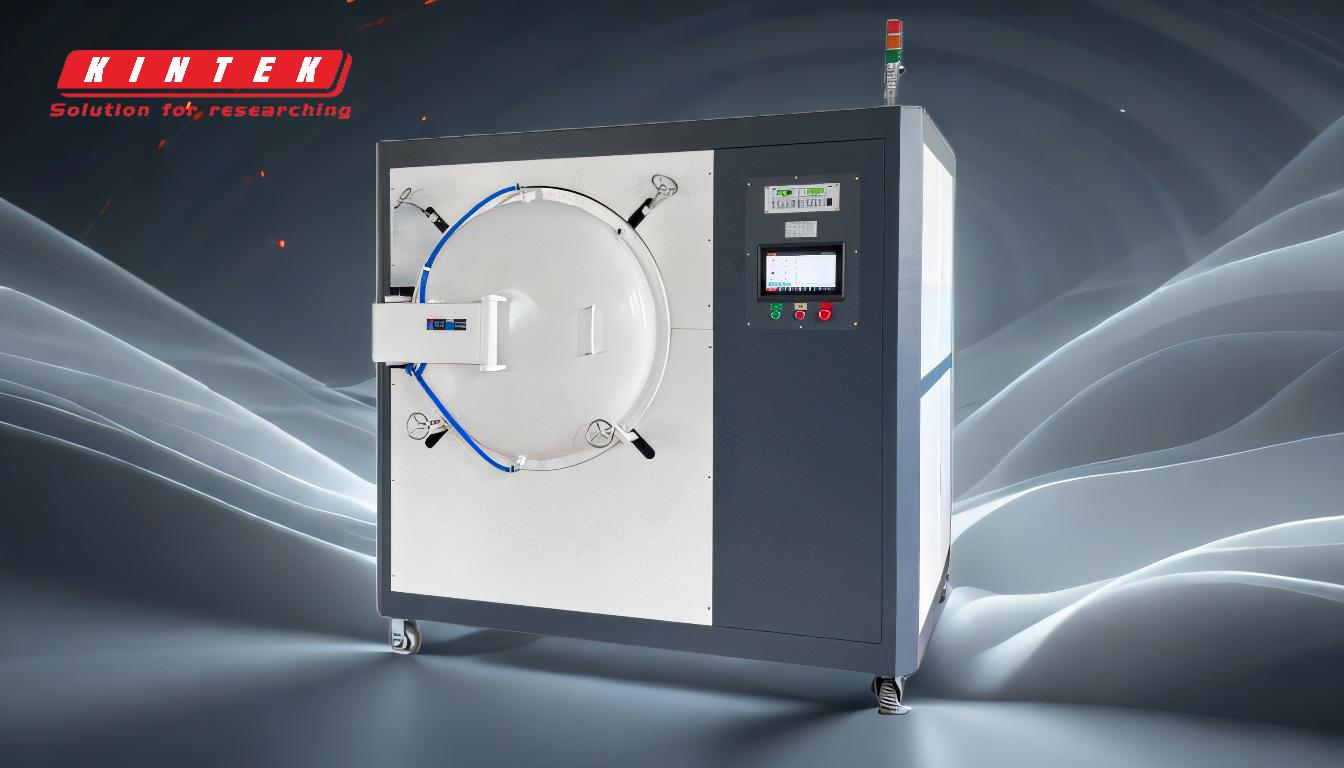
-
Cast Iron:
- Brittleness: Cast iron is inherently brittle, which makes it prone to cracking under the thermal stresses induced during the brazing process.
- High Carbon Content: The high carbon content in cast iron can lead to the formation of brittle phases at the joint, further complicating the brazing process.
- Thermal Expansion: The significant thermal expansion and contraction of cast iron during heating and cooling can cause joint failure.
-
Chromium:
- Oxide Formation: Chromium forms a stable oxide layer on its surface, which is difficult to remove and can prevent the filler metal from wetting the surface properly.
- High Melting Point: Chromium has a high melting point, which requires higher temperatures for brazing, increasing the risk of thermal damage to the base metal.
- Brittleness: Similar to cast iron, chromium's brittleness can lead to cracking under thermal stress.
-
Tungsten:
- Extremely High Melting Point: Tungsten has one of the highest melting points of all metals, making it challenging to achieve the necessary temperatures for brazing without damaging the base metal.
- Brittleness: Tungsten is also brittle, which can lead to cracking during the brazing process.
- Oxide Layer: Like chromium, tungsten forms a stable oxide layer that can hinder the wetting and bonding of the filler metal.
In conclusion, while brazing is a versatile joining method for many metals, cast iron, chromium, and tungsten present significant challenges due to their brittleness, high melting points, and oxide formation. These factors make them unsuitable for conventional brazing processes, and alternative joining methods are often required for these materials.
Summary Table:
Metal | Key Challenges for Brazing |
---|---|
Cast Iron | Brittleness, high carbon content, thermal expansion |
Chromium | Oxide formation, high melting point, brittleness |
Tungsten | Extremely high melting point, brittleness, oxide layer |
Need help with brazing challenging metals? Contact our experts today for tailored solutions!