Brazing is a metal-joining process that involves heating a filler metal above its melting point and distributing it between two or more close-fitting parts by capillary action. The primary equipment used to heat the joint during brazing is a furnace, particularly in furnace brazing processes. Furnaces provide controlled heating environments, ensuring uniform temperature distribution and high-quality brazed joints. The choice of filler metal, such as silver, copper, nickel, or gold, depends on the materials being joined and the desired properties of the joint. Proper cleaning of materials before brazing is crucial to remove contaminants and ensure strong, reliable joints.
Key Points Explained:
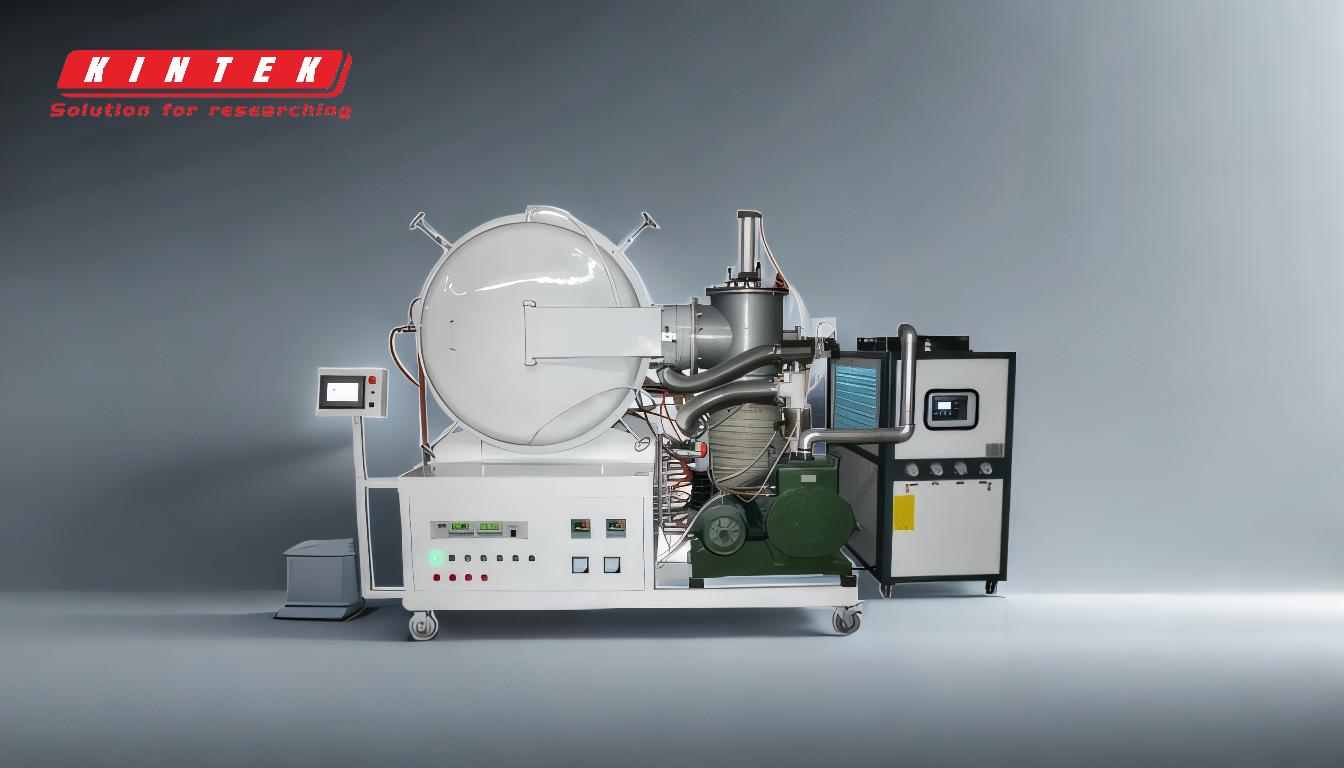
-
Furnace Brazing Equipment:
- Furnaces are the primary equipment used in brazing to heat the joint. They provide a controlled environment with uniform temperature distribution, which is essential for achieving high-quality brazed joints.
- Furnace brazing is particularly suitable for large-scale production or when joining complex assemblies, as it allows for precise temperature control and consistent results.
-
Types of Furnaces Used in Brazing:
- Batch Furnaces: These are used for smaller production runs and allow for flexibility in processing different materials and geometries.
- Continuous Furnaces: Ideal for high-volume production, these furnaces allow parts to move through different temperature zones, ensuring efficient and consistent heating.
- Vacuum Furnaces: Used for brazing materials that are sensitive to oxidation, such as stainless steels and heat-resistant alloys. Vacuum furnaces prevent oxidation by creating a low-pressure environment.
-
Filler Metals in Brazing:
- The most commonly used filler metals in brazing include silver, copper, nickel, and gold. Each filler metal has specific properties that make it suitable for different applications:
- Silver-based fillers: Offer excellent flow characteristics and are widely used for joining a variety of materials.
- Copper-based fillers: Ideal for high-temperature applications and are often used in furnace brazing of steel and other alloys.
- Nickel and gold fillers: Particularly suitable for stainless steels and heat- and corrosion-resistant alloys due to their high strength and resistance to oxidation.
- The most commonly used filler metals in brazing include silver, copper, nickel, and gold. Each filler metal has specific properties that make it suitable for different applications:
-
Importance of Material Cleaning:
- Before brazing, all materials must be thoroughly cleaned to remove surface contaminants such as grease, oil, and scale. Contaminants can interfere with the wetting and flow of the filler metal, leading to weak or defective joints.
- Cleaning methods include chemical cleaning, mechanical abrasion, or ultrasonic cleaning, depending on the material and the type of contaminants.
-
Advantages of Furnace Brazing:
- Uniform Heating: Furnaces provide consistent and uniform heating, reducing the risk of thermal distortion and ensuring strong joints.
- Scalability: Suitable for both small and large production runs, making it a versatile choice for various industries.
- Controlled Atmosphere: Furnaces can operate in controlled atmospheres (e.g., inert gases or vacuum), preventing oxidation and ensuring high-quality joints.
By understanding the role of furnaces in brazing and the importance of proper material preparation, manufacturers can achieve reliable and high-quality brazed joints for a wide range of applications.
Summary Table:
Aspect | Details |
---|---|
Primary Equipment | Furnaces provide controlled heating for uniform temperature distribution. |
Types of Furnaces | Batch, Continuous, and Vacuum furnaces for different production needs. |
Common Filler Metals | Silver, Copper, Nickel, and Gold for various material applications. |
Material Cleaning | Essential for removing contaminants to ensure strong, reliable joints. |
Advantages | Uniform heating, scalability, and controlled atmosphere for high-quality results. |
Ready to achieve high-quality brazed joints? Contact our experts today for tailored solutions!