Isostatic pressing, particularly cold isostatic pressing (CIP), is a versatile manufacturing process used to produce a wide range of products across various industries. This method is especially beneficial for creating large, complex, or high-integrity components that require uniform density and strength. The process involves applying uniform pressure from all directions to a powder-filled mold, resulting in minimal distortion or cracking. This makes CIP ideal for applications in powder metallurgy, refractory metals, ceramics, and advanced materials. The technology enhances product performance, quality, and economic efficiency, making it a preferred choice for industries requiring precision and durability. Below, we explore the key products and applications of isostatic pressing in detail.
Key Points Explained:
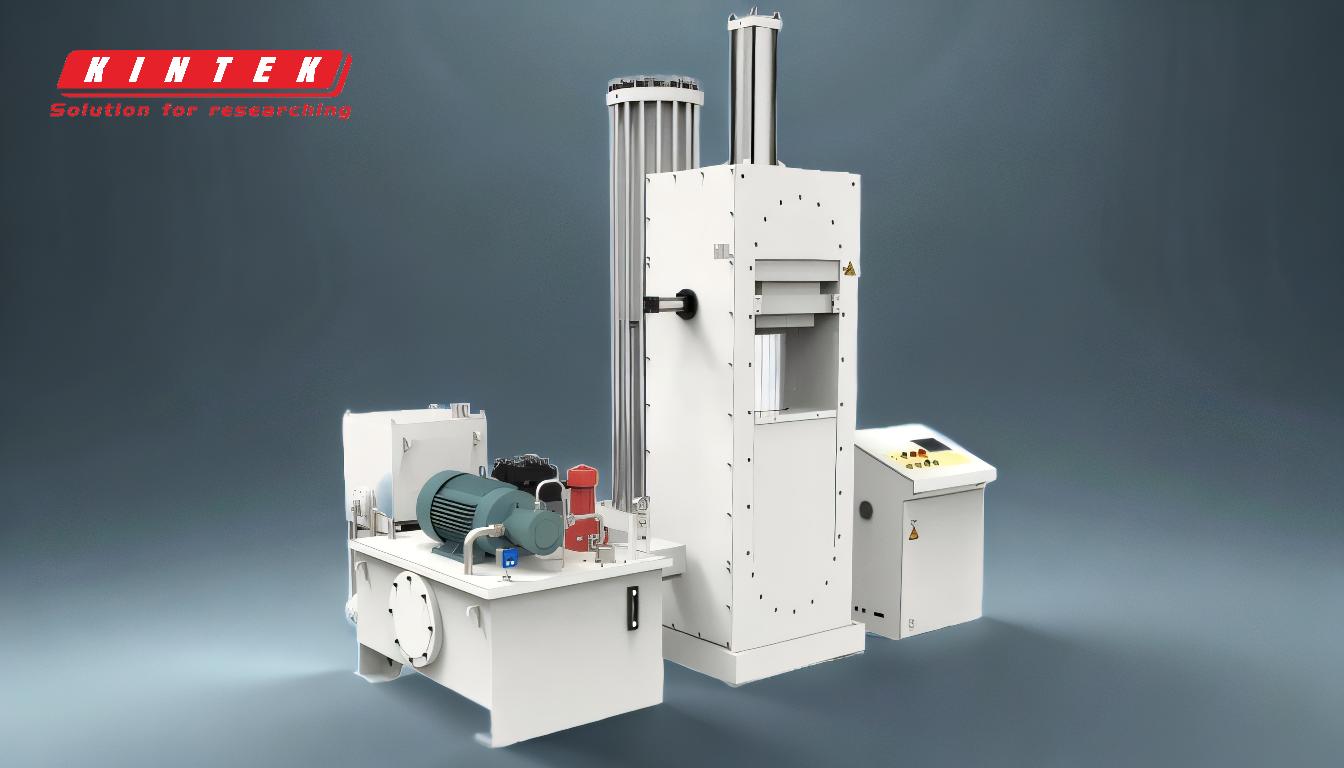
-
Large-Sized and Complex Components:
- Cold isostatic pressing is particularly advantageous for producing large or complex parts where traditional pressing dies are impractical or too costly. This includes components like turbine blades, large ceramic insulators, and complex aerospace parts. The uniform pressure application ensures that even intricate geometries are formed without defects.
-
Powder Metallurgy Products:
- CIP is widely used in powder metallurgy to produce high-density, near-net-shape components. These include gears, bearings, and other mechanical parts that require high strength and wear resistance. The process ensures uniform density, which is critical for the performance of these components.
-
Refractory Metals and Ceramics:
- The production of refractory metals such as tungsten, molybdenum, and tantalum often relies on CIP. These materials are used in high-temperature applications, such as furnace components, aerospace parts, and electrical contacts. Similarly, advanced ceramics for industrial, medical, and electronic applications are manufactured using this technology.
-
Medical and Dental Implants:
- Cold isostatic pressing is employed to create biocompatible materials like titanium and zirconia for medical and dental implants. The process ensures high precision and uniformity, which are essential for the safety and effectiveness of these implants.
-
Energy and Aerospace Applications:
- In the energy sector, CIP is used to produce components for nuclear reactors, fuel cells, and batteries. In aerospace, it is utilized to manufacture lightweight, high-strength parts such as turbine discs and engine components. The uniform density and strength achieved through CIP are critical for these high-performance applications.
-
Preparation for Sintering:
- CIP is often a preparatory step for sintering, where the pressed powder is heated to form a solid mass. This is common in the production of advanced materials like silicon carbide and alumina, which are used in cutting tools, abrasives, and electronic substrates.
-
Economic and Performance Benefits:
- The use of cold isostatic pressing machines improves product performance and quality while reducing material waste. This leads to significant economic benefits, especially in industries where material costs are high. The technology also allows for the production of multiple compactions in a single cycle, further enhancing efficiency.
By leveraging the unique advantages of cold isostatic pressing, industries can produce high-quality, durable, and complex components that meet the demanding requirements of modern applications. This technology continues to expand its reach, driven by its ability to deliver superior results in a cost-effective manner.
Summary Table:
Category | Examples |
---|---|
Large-Sized Components | Turbine blades, large ceramic insulators, aerospace parts |
Powder Metallurgy Products | Gears, bearings, mechanical parts |
Refractory Metals & Ceramics | Tungsten, molybdenum, tantalum, advanced ceramics |
Medical & Dental Implants | Titanium, zirconia implants |
Energy & Aerospace Components | Nuclear reactor parts, fuel cells, turbine discs |
Preparation for Sintering | Silicon carbide, alumina for cutting tools and electronic substrates |
Economic Benefits | Reduced material waste, improved efficiency, cost-effective production |
Learn how isostatic pressing can revolutionize your production process—contact our experts today!