Pellet mill die sizes are critical for the efficiency and durability of the pelletizing process. The total thickness of the die ensures structural integrity to prevent breakage, while the inlet depth facilitates the smooth entry of feed into the compression area. The lifespan of a pellet mill die, typically ranging from 600 to 800 hours under optimal conditions, is influenced by various factors such as feed formulation, raw material properties, and maintenance practices. Proper handling, regular maintenance, and understanding the interaction between material properties and die design are essential for maximizing die life and performance.
Key Points Explained:
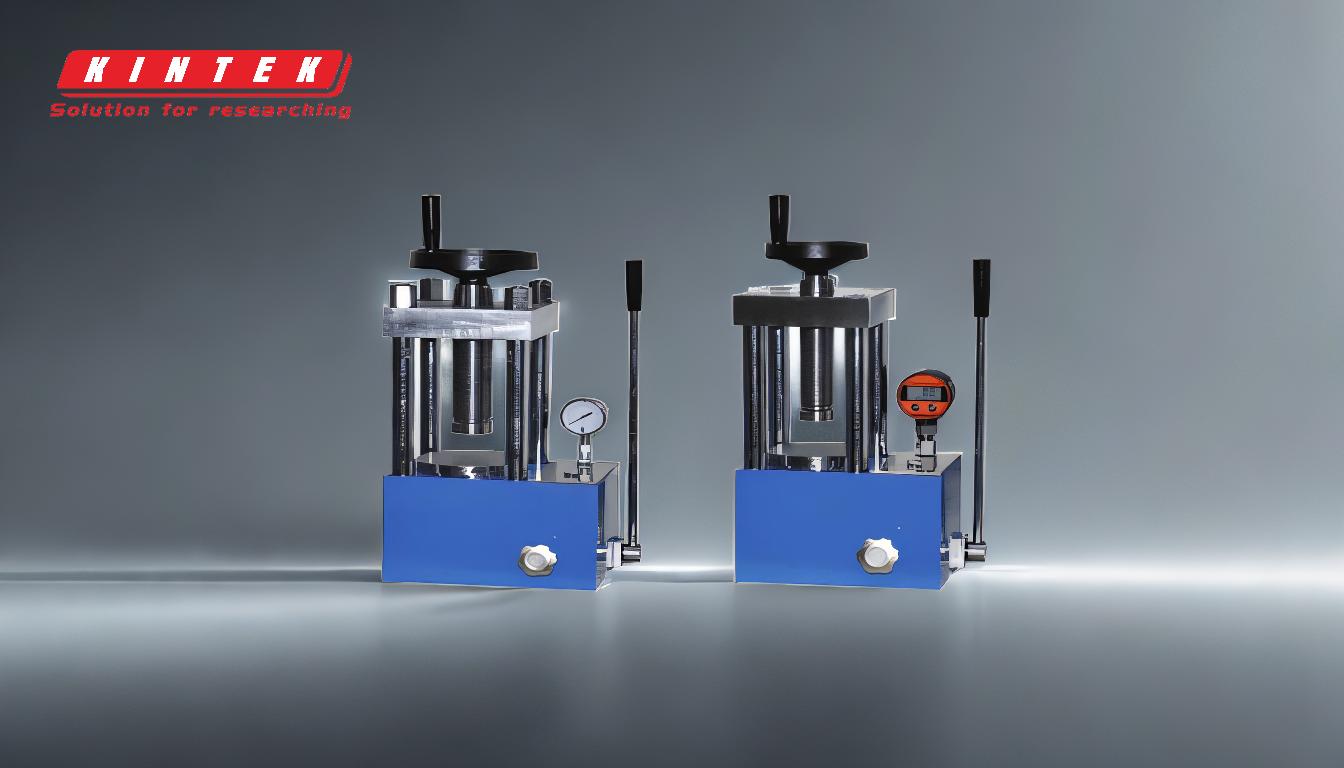
-
Total Thickness of the Die:
- The total thickness (T) of a pellet mill die is crucial for its durability. It provides the necessary structural strength to withstand the pressures and stresses during the pelletizing process, thereby preventing breakage.
-
Inlet Depth:
- The inlet depth refers to the depth of the countersink where the feed material enters the compression area of the die. This design feature ensures a smooth and efficient transition of the feed into the pelletizing zone, which is essential for consistent pellet quality.
-
Lifespan of Pellet Mill Dies:
- Under standard conditions, pellet mill dies are expected to last between 600 to 800 hours. However, this lifespan can vary significantly based on several factors:
- Feed Formulation and Composition: High fiber content in the feed can reduce die life due to increased wear.
- Raw Material Properties: Fibrous, spongy, or abrasive materials can accelerate die wear.
- Fat Content: Higher fat content in the feed acts as a lubricant, reducing friction and potentially extending die life.
- Particle Size: Consistent particle size in the mash can help extend die life by reducing uneven wear.
- Moisture Content: Proper conditioning of the feed to achieve optimal moisture levels is crucial; poor conditioning can lead to premature die wear.
- Operator Skill and Maintenance: Regular checks on wear, timely maintenance, and proper handling can significantly impact die longevity.
- Under standard conditions, pellet mill dies are expected to last between 600 to 800 hours. However, this lifespan can vary significantly based on several factors:
-
Maintenance Practices:
- Effective maintenance practices are essential for maximizing the lifespan of pellet mill dies:
- Uniform Wear: Regularly changing the side of the die can help achieve uniform wear, thereby extending its life.
- Cleaning Magnets: Cleaning magnets every 6 hours helps remove metal contaminants that could damage the die.
- Roll Shell Maintenance: Timely changing of roll shells and tightening roll shell support stud bolts are necessary to maintain optimal die performance.
- Die Optimization: Using separate dies for different types of feed (e.g., broiler and layer feed) can optimize performance and extend die life.
- Effective maintenance practices are essential for maximizing the lifespan of pellet mill dies:
Understanding these key points helps in selecting the appropriate die size and implementing practices that enhance the efficiency and longevity of pellet mill operations.
Summary Table:
Key Aspect | Details |
---|---|
Total Thickness (T) | Ensures structural integrity, prevents breakage under pressure. |
Inlet Depth | Facilitates smooth feed entry into the compression area for consistent quality. |
Lifespan | 600-800 hours under optimal conditions, influenced by feed and maintenance. |
Factors Affecting Lifespan | Feed formulation, raw material properties, fat content, particle size, moisture, and operator skill. |
Maintenance Practices | Uniform wear, cleaning magnets, roll shell maintenance, and die optimization. |
Maximize your pellet mill die performance—contact our experts today for tailored solutions!