Brazing copper requires careful temperature control to ensure a strong and reliable joint. The optimal temperature range for brazing copper in a hydrogen atmosphere is typically between 1,100 and 1,500℉. This range ensures proper flow of the filler metal and strong bonding without overheating the base material. The process also involves considerations like the atmosphere (e.g., hydrogen) and the type of filler metal used, which can influence the final quality of the joint.
Key Points Explained:
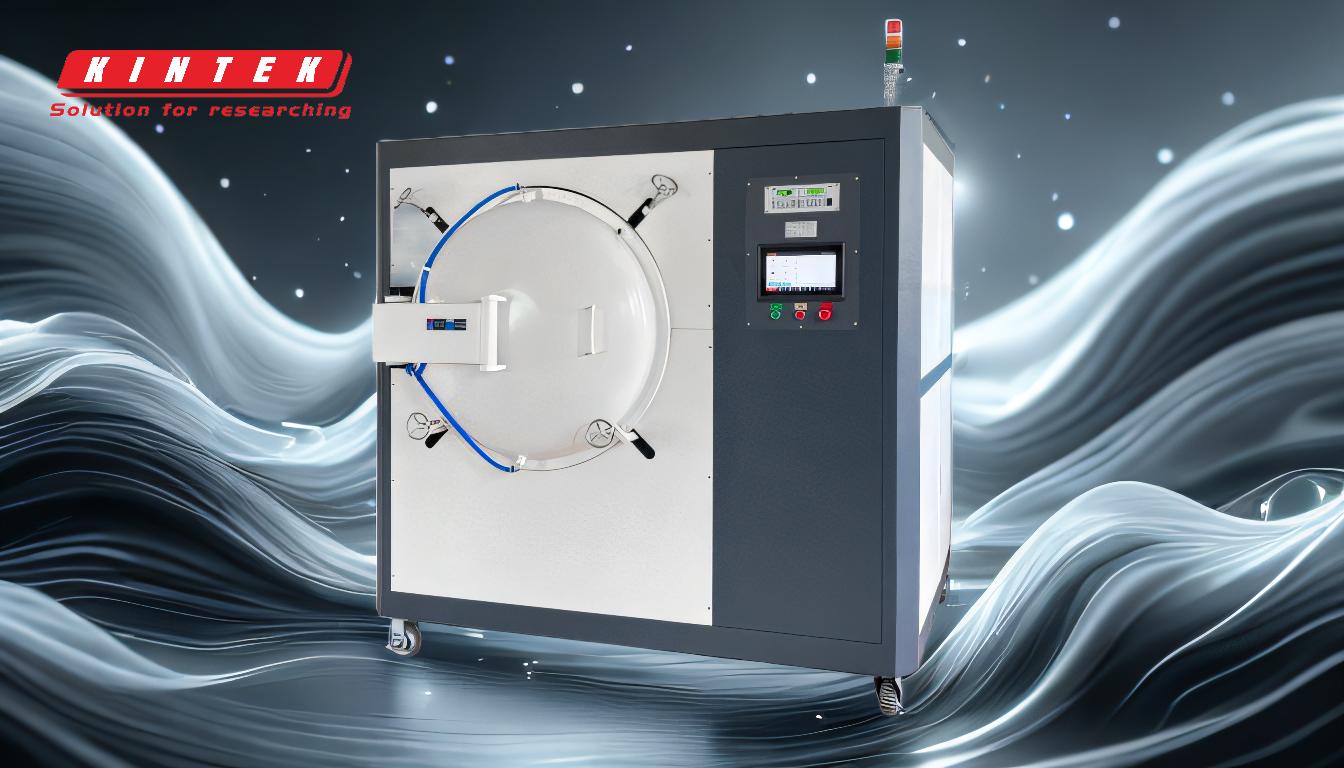
-
Optimal Temperature Range for Brazing Copper
- The ideal temperature for brazing copper in a hydrogen atmosphere is between 1,100 and 1,500℉.
- This range ensures that the filler metal flows properly and bonds effectively with the copper base material.
- Temperatures below 1,100℉ may result in incomplete bonding, while temperatures above 1,500℉ risk overheating and damaging the copper.
-
Role of Hydrogen Atmosphere
- A hydrogen atmosphere is often used in brazing copper because it helps remove oxides from the surface of the metal, ensuring a clean and strong joint.
- Hydrogen acts as a reducing agent, preventing oxidation during the brazing process.
- The dew point of the hydrogen atmosphere must be carefully controlled to avoid introducing moisture, which can lead to oxidation.
-
Considerations for Brazing Copper with Other Metals
- When brazing copper with stainless steel, additional factors come into play. For example, chromium in stainless steel can form chromium oxide, which may affect the brazing process.
- Nickel plating or other suitable metals can be used to improve wet hydrogen brazing when working with stainless steel and copper.
- The choice of filler metal is critical and should be compatible with both copper and the other metal being joined.
-
Importance of Filler Metal Selection
- The filler metal used in brazing must have a melting point lower than the base metals but high enough to ensure a strong bond.
- Common filler metals for copper brazing include silver-based alloys, which flow well and provide excellent joint strength.
- The filler metal should also be compatible with the hydrogen atmosphere to avoid contamination or oxidation.
-
Practical Tips for Successful Brazing
- Ensure the surfaces to be joined are clean and free of contaminants before brazing.
- Use proper fixtures to hold the parts in place during the brazing process.
- Monitor the temperature closely to avoid overheating or underheating, which can compromise the joint quality.
- Allow the joint to cool slowly to minimize thermal stress and ensure a durable bond.
By following these guidelines, you can achieve high-quality brazed joints in copper, whether working with pure copper or in combination with other metals like stainless steel. Proper temperature control, atmosphere management, and filler metal selection are key to success.
Summary Table:
Key Factor | Details |
---|---|
Optimal Temperature Range | 1,100–1,500℉ for proper filler metal flow and strong bonding. |
Hydrogen Atmosphere Role | Removes oxides, prevents oxidation, and ensures clean joints. |
Filler Metal Selection | Silver-based alloys are common; must be compatible with hydrogen atmosphere. |
Brazing with Other Metals | Nickel plating may be required for stainless steel and copper combinations. |
Practical Tips | Clean surfaces, monitor temperature, and allow slow cooling for durability. |
Need expert advice on brazing copper? Contact us today for tailored solutions!