Hydrogen annealing is a specialized process conducted in a hydrogen atmosphere at elevated temperatures, typically ranging between 200°C and 300°C. This method is primarily used to relieve internal stresses in materials caused by fabrication processes like casting, welding, or coating. The process also helps remove hydrogen atoms responsible for embrittlement, improving the material's mechanical properties. The temperature range is critical, as it allows hydrogen atoms to diffuse out of the material while preventing oxidation and decarburization. Hydrogen annealing is often referred to as "bright annealing" due to its ability to clean oxidized surfaces, but it requires careful control to avoid adverse effects on the material.
Key Points Explained:
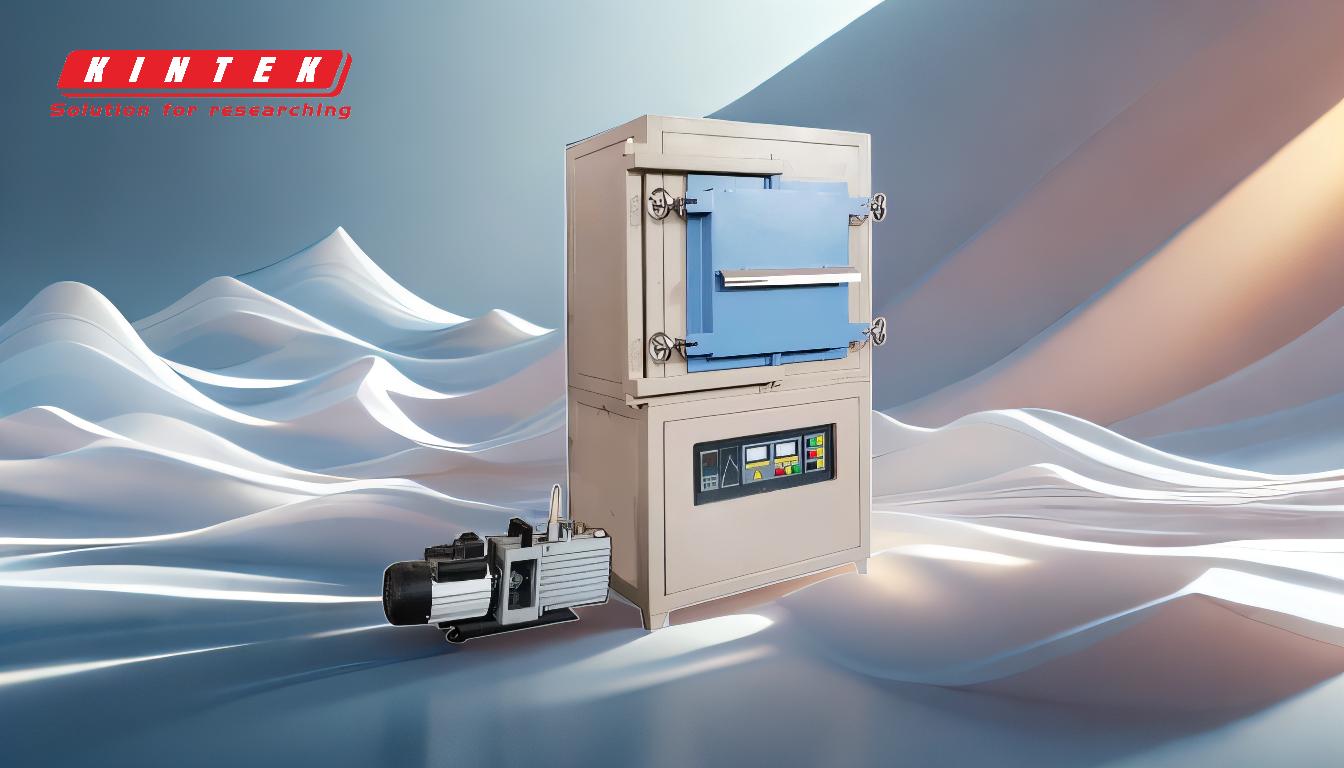
-
Temperature Range for Hydrogen Annealing
- Hydrogen annealing is typically performed at temperatures between 200°C and 300°C.
- This range is chosen because:
- At 200°C, hydrogen atoms begin to diffuse out of materials like iron and certain stainless steels, which is the minimum temperature required for the process.
- Higher temperatures (up to 300°C) enhance the diffusion rate, ensuring efficient removal of hydrogen atoms and internal stresses.
- The temperature range also aids in eliminating vacancies in the material, which can improve mechanical properties.
-
Purpose of Hydrogen Annealing
- Hydrogen annealing is primarily used to:
- Relieve internal stresses induced during fabrication processes such as casting, welding, or galvanizing.
- Remove hydrogen embrittlement, a phenomenon where hydrogen atoms trapped in the material weaken its structural integrity.
- Improve the material's mechanical properties by reducing defects and enhancing uniformity.
- Hydrogen annealing is primarily used to:
-
Hydrogen Atmosphere
- The process is carried out in a 100% hydrogen atmosphere to:
- Prevent oxidation and discoloration of the material.
- Promote surface cleaning by reducing oxides on the material, a process often referred to as "bright annealing."
- Ensure a controlled environment that facilitates the diffusion of hydrogen atoms out of the material.
- The process is carried out in a 100% hydrogen atmosphere to:
-
Challenges and Precautions
- While hydrogen annealing offers significant benefits, it comes with challenges:
- Decarburization: Hydrogen can decarburize steel parts, leading to a loss of carbon content and potential weakening of the material. Precautions must be taken to minimize this effect.
- Cost: Hydrogen is the most expensive annealing atmosphere. To reduce costs, nitrogen-hydrogen blends are sometimes used as an alternative.
- While hydrogen annealing offers significant benefits, it comes with challenges:
-
Applications of Hydrogen Annealing
- Hydrogen annealing is commonly used in industries where material integrity is critical, such as:
- Welding: To relieve stresses and remove hydrogen introduced during the welding process.
- Coating and Galvanizing: To improve the adhesion and durability of coatings.
- Casting: To eliminate internal stresses and improve the mechanical properties of cast parts.
- Hydrogen annealing is commonly used in industries where material integrity is critical, such as:
-
Process Duration
- The material is typically kept in the hydrogen annealing oven for several hours.
- The duration depends on factors such as:
- The type of material being annealed.
- The thickness and size of the material.
- The desired level of stress relief and hydrogen removal.
-
Benefits of Hydrogen Annealing
- Key benefits include:
- Improved mechanical properties of the material.
- Enhanced surface quality through oxide reduction.
- Reduced risk of hydrogen embrittlement, ensuring greater material reliability.
- Key benefits include:
-
Alternative Atmospheres
- While 100% hydrogen is the most effective atmosphere, nitrogen-hydrogen blends are often used as a cost-effective alternative.
- These blends still provide many of the benefits of hydrogen annealing while reducing overall process costs.
In summary, hydrogen annealing is a precise and controlled process that relies on a specific temperature range (200-300°C) and a hydrogen-rich atmosphere to achieve its goals. It is widely used in industries where material integrity and performance are critical, but it requires careful management to avoid potential drawbacks like decarburization.
Summary Table:
Key Aspect | Details |
---|---|
Temperature Range | 200°C to 300°C, optimized for hydrogen diffusion and stress relief. |
Purpose | Relieves internal stresses, removes hydrogen embrittlement, enhances mechanical properties. |
Atmosphere | 100% hydrogen or nitrogen-hydrogen blends for cost efficiency. |
Applications | Welding, coating, galvanizing, and casting industries. |
Benefits | Improved mechanical properties, enhanced surface quality, reduced embrittlement. |
Challenges | Risk of decarburization and higher costs with pure hydrogen. |
Learn how hydrogen annealing can optimize your material performance—contact our experts today!