The temperature of an annealing furnace depends on the material being processed, as it must heat the material above its recrystallization temperature. The recrystallization temperature varies significantly between materials, typically ranging from 400°C to 1200°C (752°F to 2192°F) or higher. For example, copper and its alloys are annealed at around 400°C to 700°C, while stainless steel may require temperatures between 900°C and 1200°C. The furnace maintains this temperature for a specific duration to allow the material's internal structure to reorganize, improving ductility, reducing hardness, and relieving internal stresses. Cooling is then done at a controlled rate to achieve the desired material properties.
Key Points Explained:
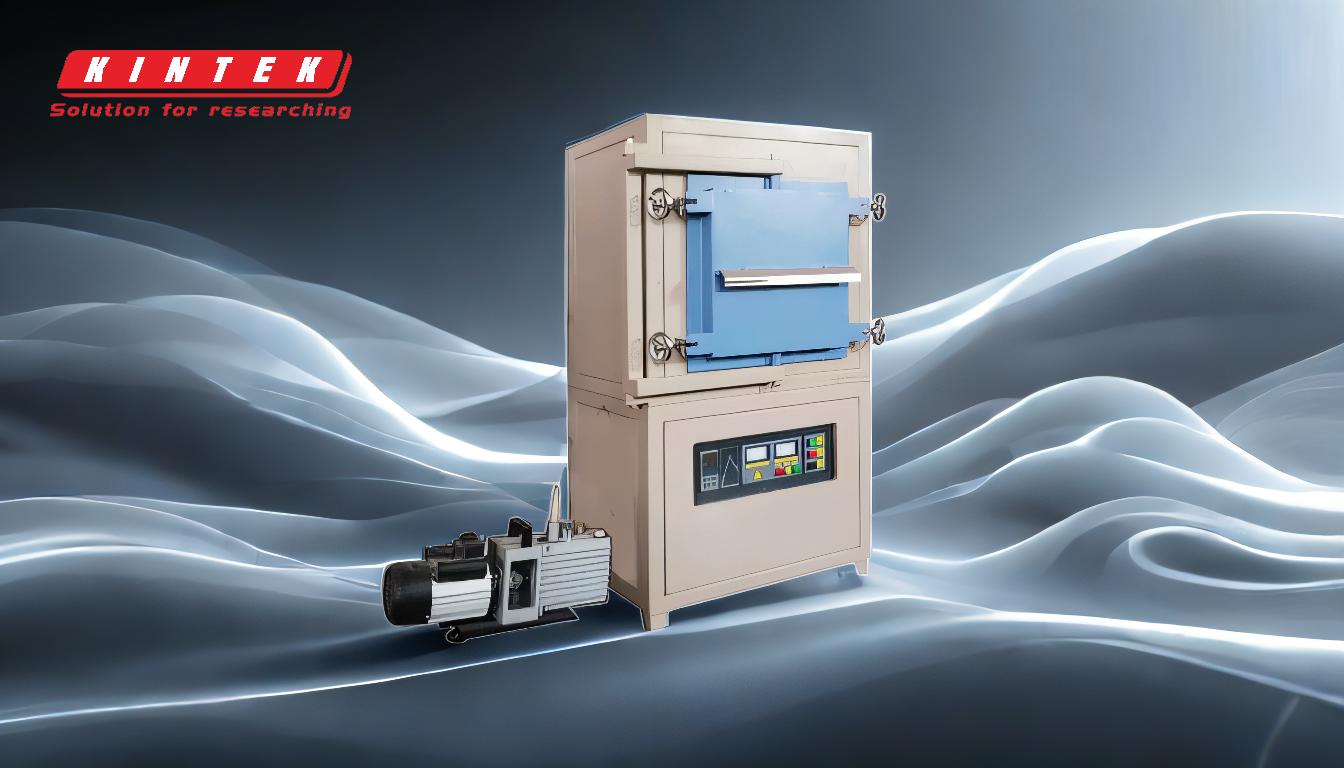
-
Recrystallization Temperature Determines Furnace Temperature:
- The annealing furnace heats materials above their recrystallization temperature, which is the point at which new grains form in the material's structure.
- The recrystallization temperature varies by material:
- Copper and Copper Alloys: 400°C to 700°C (752°F to 1292°F).
- Stainless Steel: 900°C to 1200°C (1652°F to 2192°F).
- Refractory Metals: Can exceed 1200°C (2192°F).
- The furnace must be capable of reaching and maintaining these temperatures accurately.
-
Purpose of Heating Above Recrystallization Temperature:
- Heating above the recrystallization temperature allows the material's atoms to redistribute, eliminating dislocations and internal stresses.
- This process improves the material's ductility, making it easier to work with in subsequent manufacturing steps.
- It also reduces hardness and increases toughness, which are critical for materials used in demanding applications.
-
Holding Temperature for Specific Durations:
- Once the material reaches the desired temperature, it is held there for a specific period to ensure uniform heating and complete recrystallization.
- The duration depends on the material type, thickness, and desired properties. For example:
- Thin copper wires may require shorter holding times (minutes).
- Thick stainless steel components may need hours to achieve uniform results.
-
Controlled Cooling Process:
- After the holding period, the material is cooled at a controlled rate to prevent the reintroduction of stresses or uneven properties.
- Cooling methods vary:
- Air Cooling: Suitable for some materials like copper.
- Furnace Cooling: Slower cooling for materials requiring precise control.
- Quenching: Rapid cooling for specific alloys to achieve unique properties.
-
Material-Specific Applications:
- Annealing furnaces are designed for a wide range of materials, including:
- Copper and Copper Alloys: Used in electrical wiring and plumbing.
- Stainless Steel: Common in automotive, aerospace, and medical industries.
- Refractory Metals: Used in high-temperature applications like jet engines and nuclear reactors.
- Each material requires tailored furnace settings to achieve optimal results.
- Annealing furnaces are designed for a wide range of materials, including:
-
Furnace Design and Capabilities:
- Annealing furnaces are built to handle specific temperature ranges and material types.
- Key features include:
- Temperature Control Systems: Ensure precise heating and cooling rates.
- Atmosphere Control: Some furnaces use inert gases (e.g., nitrogen or argon) to prevent oxidation during annealing.
- Uniform Heating: Ensures consistent material properties throughout the workpiece.
-
Importance for Material Properties:
- Annealing is critical for achieving desired mechanical properties, such as:
- Increased Ductility: Allows materials to be shaped without cracking.
- Reduced Hardness: Makes materials easier to machine or form.
- Stress Relief: Prevents warping or failure in service.
- Annealing is critical for achieving desired mechanical properties, such as:
In summary, the temperature of an annealing furnace is not fixed but depends on the material being processed. It must exceed the recrystallization temperature of the material, which varies widely. The furnace's ability to precisely control heating, holding, and cooling processes ensures the material achieves the desired properties for its intended application.
Summary Table:
Material | Recrystallization Temperature | Common Applications |
---|---|---|
Copper & Alloys | 400°C to 700°C (752°F to 1292°F) | Electrical wiring, plumbing |
Stainless Steel | 900°C to 1200°C (1652°F to 2192°F) | Automotive, aerospace, medical industries |
Refractory Metals | Exceeds 1200°C (2192°F) | Jet engines, nuclear reactors |
Need help selecting the right annealing furnace for your materials? Contact our experts today!