The optimal temperature for a furnace depends on its type and intended use. For residential heating, the DOE recommends a range of 68°F to 72°F, with higher temperatures (up to 78°F) suggested for households with elderly residents. For industrial furnaces, such as muffle furnaces, operating at 50°C below the maximum temperature ensures longevity, while continuous furnaces maintain permanent temperatures tailored to specific heat treatment processes like annealing or hardening. Environmental factors, such as humidity and the presence of corrosive gases, also play a critical role in determining the appropriate operating conditions.
Key Points Explained:
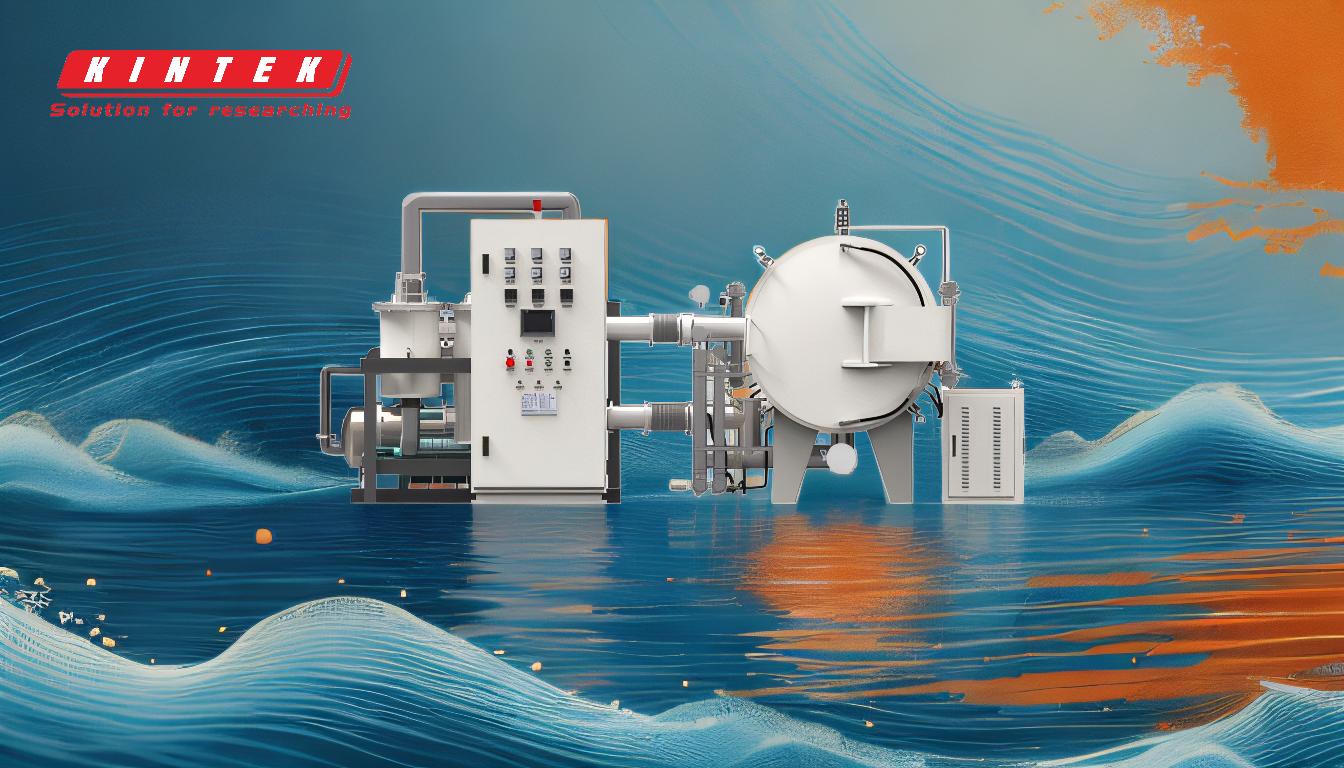
-
Residential Furnace Temperature Recommendations
- The Department of Energy (DOE) suggests maintaining residential furnace temperatures between 68°F and 72°F for general comfort and energy efficiency.
- For households with elderly individuals, temperatures can be increased to up to 78°F to ensure comfort and safety, as older adults may be more sensitive to colder environments.
- These recommendations balance energy consumption with the need for a comfortable living environment.
-
Muffle Furnace Operating Guidelines
- Muffle furnaces should operate 50°C below their maximum rated temperature to extend the lifespan of the heating elements, particularly the furnace wire.
- Operating conditions should avoid environments with relative humidity exceeding 85%, as high humidity can damage the furnace components.
- The furnace should be used in areas free from conductive dust, explosive gases, or corrosive gases, which can compromise safety and performance.
- When heating materials like metals with grease or volatile substances, use sealed containers or proper ventilation to prevent corrosive gases from damaging the heating elements.
-
Continuous Furnace Temperature Settings
- Continuous furnaces are designed to operate at permanent, consistent temperatures tailored to specific industrial processes.
- These furnaces are used for heating components made of the same grade of steel and undergoing the same heat treatment cycles, such as:
- Annealing: Softening materials to improve ductility.
- Hardening: Increasing material strength through controlled heating and cooling.
- Normalising: Refining grain structure to enhance mechanical properties.
- Carburising: Adding carbon to the surface of low-carbon steels to increase hardness.
- The temperature settings are highly specialised and depend on the material and process requirements.
-
Environmental and Safety Considerations
- For all furnace types, environmental conditions such as humidity, dust, and gas exposure must be carefully controlled to ensure safe and efficient operation.
- Proper ventilation and containment measures are essential when heating materials that release volatile or corrosive gases.
- Regular maintenance and adherence to manufacturer guidelines are critical to prevent equipment failure and ensure safety.
By understanding these key points, users can determine the appropriate temperature settings for their specific furnace type, ensuring optimal performance, longevity, and safety.
Summary Table:
Furnace Type | Optimal Temperature | Key Considerations |
---|---|---|
Residential Furnace | 68°F to 72°F (up to 78°F for elderly households) | Balance comfort and energy efficiency; higher temps for elderly safety. |
Muffle Furnace | 50°C below maximum rated temperature | Avoid high humidity (>85%), conductive dust, explosive/corrosive gases. |
Continuous Furnace | Permanent, consistent temperatures for processes like annealing, hardening, and more. | Tailored to material and process requirements; ensure proper ventilation and safety. |
Need help determining the best temperature for your furnace? Contact our experts today for tailored advice!