Heat treatment plays a critical role in determining the hardness of metals and alloys. Among the various heat treatment processes, quenching is widely recognized for achieving the highest hardness. Quenching involves rapidly cooling a heated metal, typically steel, in water, oil, or another medium to lock in a hard microstructure, such as martensite. However, the specific hardness achieved depends on factors like the material's composition, the quenching medium, and subsequent tempering. While quenching maximizes hardness, it can also make the material brittle, so tempering is often used to balance hardness with toughness. Other heat treatments like annealing and normalizing improve ductility and reduce hardness.
Key Points Explained:
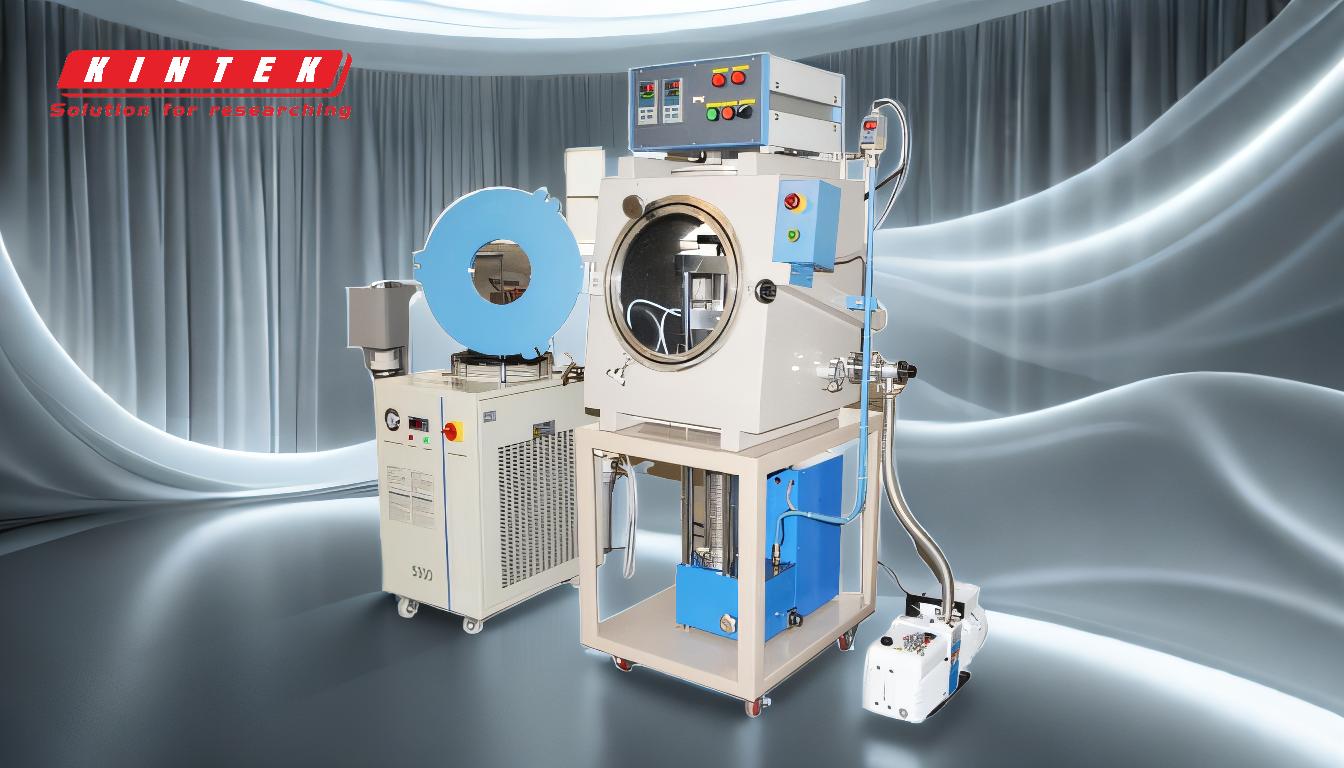
-
Quenching as the Primary Hardening Process:
- Quenching involves heating the metal to its austenitizing temperature (typically above 900°C for steel) and then rapidly cooling it in a medium like water, oil, or air.
- This rapid cooling suppresses the formation of softer phases like pearlite and promotes the formation of martensite, a hard and brittle microstructure.
- The hardness achieved depends on the cooling rate and the material's carbon content. Higher carbon steels generally achieve greater hardness after quenching.
-
Factors Influencing Hardness in Quenching:
- Material Composition: Alloying elements like carbon, chromium, and manganese enhance hardenability, allowing deeper hardening during quenching.
- Quenching Medium: Water provides the fastest cooling rate, resulting in the highest hardness but also the highest risk of cracking. Oil cools more slowly, reducing cracking risk but slightly lowering hardness.
- Section Thickness: Thicker sections may not cool uniformly, leading to variations in hardness.
-
Role of Tempering After Quenching:
- While quenching maximizes hardness, it often results in brittleness, making the material prone to cracking under stress.
- Tempering involves reheating the quenched material to a temperature below its critical point (typically 150–650°C) and then cooling it slowly.
- This process reduces brittleness and internal stresses while retaining a significant portion of the hardness.
-
Comparison with Other Heat Treatments:
- Annealing: Involves slow cooling to soften the material, improving machinability and ductility but reducing hardness.
- Normalizing: Similar to annealing but involves air cooling, resulting in a finer grain structure and slightly higher hardness than annealing.
- Case Hardening: Adds a hard surface layer while maintaining a tough core, but the overall hardness is lower than that achieved by quenching.
-
Practical Considerations for Achieving Maximum Hardness:
- Select the appropriate steel grade with sufficient carbon and alloying elements.
- Ensure proper heating and uniform cooling during quenching to avoid distortion or cracking.
- Use tempering to balance hardness with toughness, depending on the application.
-
Applications of High-Hardness Materials:
- High-hardness materials are essential for tools, dies, gears, and components subject to wear or high stress.
- Examples include drill bits, cutting tools, and bearings, where hardness is critical for performance and longevity.
In conclusion, quenching is the heat treatment process that provides the highest hardness, but it must be carefully controlled and often followed by tempering to ensure the material is both hard and durable. The specific hardness achieved depends on the material, quenching medium, and tempering process, making it essential to tailor the heat treatment to the application's requirements.
Summary Table:
Aspect | Details |
---|---|
Primary Process | Quenching: Rapid cooling of heated metal to form hard martensite structure. |
Key Factors | Material composition, quenching medium, and tempering. |
Quenching Medium | Water (fastest cooling, highest hardness), oil (slower, less cracking). |
Tempering | Reduces brittleness while retaining hardness. |
Comparison | Annealing and normalizing reduce hardness but improve ductility. |
Applications | Tools, dies, gears, and wear-resistant components. |
Need help optimizing your heat treatment process? Contact our experts today for tailored solutions!