The best heat treatment process depends on the specific material, desired properties, and application. Heat treatment processes such as annealing, tempering, quenching, and case hardening are commonly used, each offering unique benefits. Annealing improves ductility and reduces hardness, making it ideal for materials that need to be machined or formed. Tempering enhances toughness and reduces brittleness, often used after quenching. Quenching rapidly cools the material to increase hardness and strength, while case hardening creates a hard outer surface while maintaining a tough core. The choice of process should align with the material's composition, intended use, and required mechanical properties.
Key Points Explained:
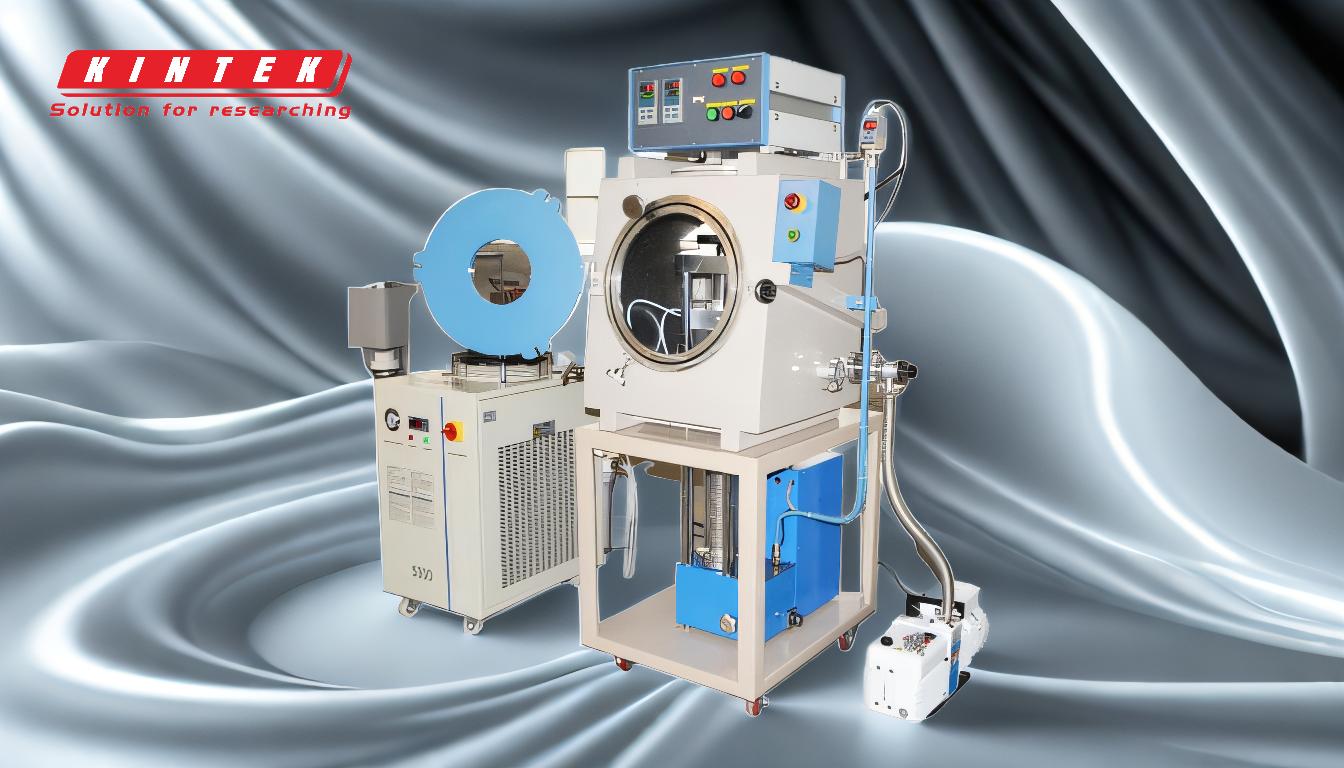
-
Understanding Heat Treatment Processes:
- Heat treatment involves controlled heating and cooling of materials to alter their physical and mechanical properties.
- Common processes include annealing, tempering, quenching, and case hardening, each serving different purposes.
-
Annealing:
- Annealing involves heating the material to a specific temperature and then slowly cooling it to improve ductility and reduce hardness.
- This process is ideal for materials that need to be machined or formed, as it makes them easier to work with.
-
Tempering:
- Tempering is typically performed after quenching to reduce brittleness and improve toughness.
- It involves reheating the material to a lower temperature and then cooling it, balancing hardness with flexibility.
-
Quenching:
- Quenching rapidly cools the material by immersing it in a liquid (e.g., water, oil) to increase hardness and strength.
- This process is suitable for materials that require high wear resistance but may increase brittleness.
-
Case Hardening:
- Case hardening creates a hard outer surface while maintaining a tough core, enhancing wear resistance without compromising overall toughness.
- Techniques like carburizing and nitriding are commonly used for this purpose.
-
Material Considerations:
- The choice of heat treatment process depends on the material's composition, such as carbon content in steel or alloying elements in metals.
- Different materials respond differently to heat treatment, so understanding the material's properties is crucial.
-
Application Requirements:
- The intended use of the material determines the best heat treatment process. For example, tools requiring high hardness may benefit from quenching and tempering, while components needing ductility may require annealing.
-
Process Selection:
- Evaluate the desired mechanical properties (e.g., hardness, toughness, ductility) and match them with the appropriate heat treatment process.
- Consider factors like cost, equipment availability, and production timelines when making a decision.
By carefully analyzing the material, application, and desired outcomes, you can select the most suitable heat treatment process to achieve optimal results.
Summary Table:
Process | Primary Benefit | Best For |
---|---|---|
Annealing | Improves ductility, reduces hardness | Materials needing machining or forming |
Tempering | Enhances toughness, reduces brittleness | Post-quenching to balance hardness and flexibility |
Quenching | Increases hardness and strength | Materials requiring high wear resistance |
Case Hardening | Creates hard surface, maintains tough core | Components needing wear resistance and toughness |
Need help selecting the right heat treatment process? Contact our experts today for tailored advice!