When selecting heating elements for high-temperature furnaces operating in an oxidizing atmosphere, the choice of material is critical due to the harsh conditions that can lead to rapid degradation of unsuitable materials. The primary considerations include the maximum operating temperature, resistance to oxidation, and mechanical stability. Based on the references provided, the most suitable materials for oxidizing atmospheres are silicon carbide (SiC) and molybdenum disilicide (MoSi2). These materials are known for their excellent oxidation resistance and ability to withstand high temperatures, making them ideal for such environments. Below, we will explore the key points in detail to understand why these materials are preferred and how they perform under oxidizing conditions.
Key Points Explained:
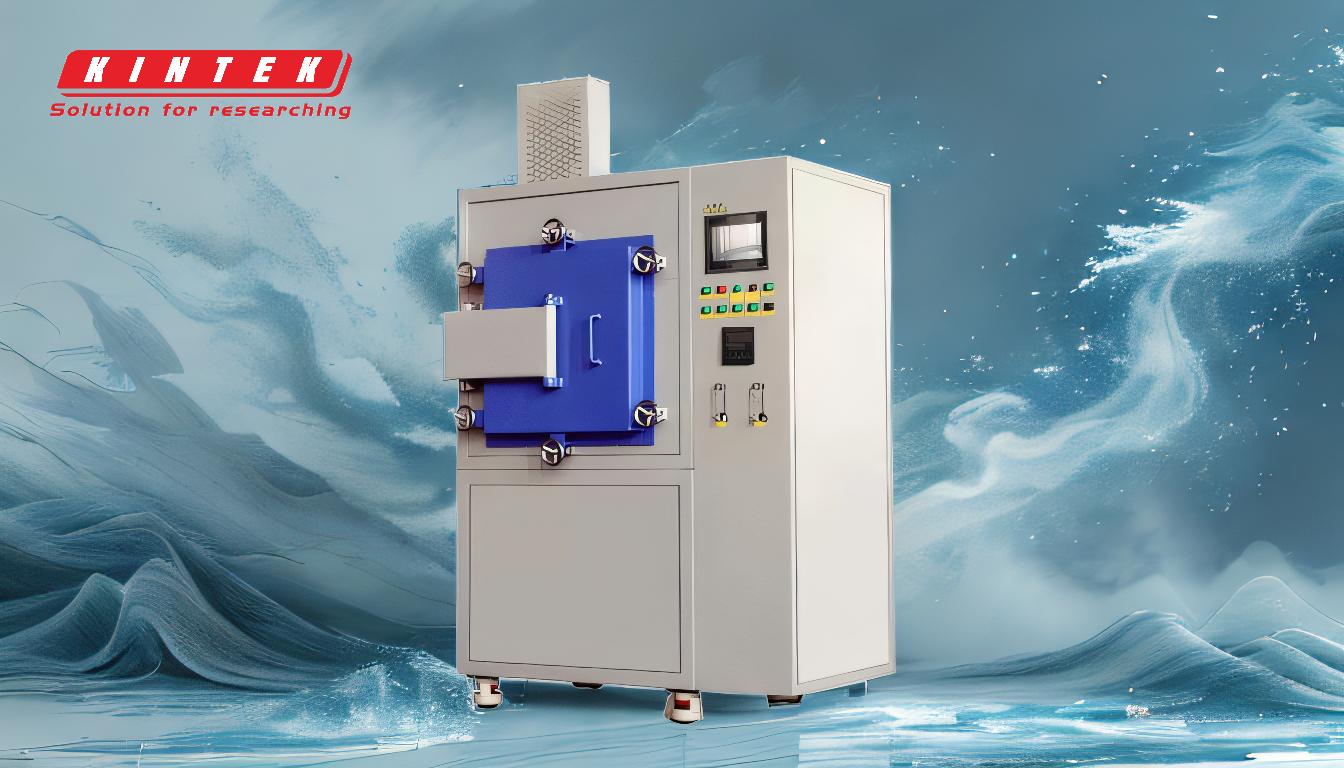
-
Material Selection for Oxidizing Atmospheres:
- Silicon Carbide (SiC): SiC is a popular choice for heating elements in oxidizing atmospheres due to its excellent thermal conductivity, high melting point (approximately 2700°C), and superior oxidation resistance. It forms a protective layer of silicon dioxide (SiO2) when exposed to oxygen, which prevents further oxidation and extends the element's lifespan.
- Molybdenum Disilicide (MoSi2): MoSi2 is another material well-suited for oxidizing environments. It operates effectively at temperatures up to 1800°C and forms a protective SiO2 layer similar to SiC. This layer acts as a barrier against further oxidation, ensuring long-term stability and performance.
-
Temperature Ranges and Applications:
- Silicon Carbide: SiC heating elements are typically used in applications requiring temperatures between 1300°C and 1400°C. They are commonly employed in processes such as ceramic sintering, glass melting, and heat treatment.
- Molybdenum Disilicide: MoSi2 elements are ideal for higher temperature ranges, typically between 1400°C and 1700°C. They are often used in advanced ceramic processing, semiconductor manufacturing, and other high-temperature industrial applications.
-
Advantages of SiC and MoSi2 in Oxidizing Atmospheres:
- Oxidation Resistance: Both SiC and MoSi2 form protective oxide layers that prevent further oxidation, ensuring durability in high-temperature oxidizing environments.
- Thermal Stability: These materials maintain their structural integrity and performance even under prolonged exposure to high temperatures.
- Long Service Life: Due to their resistance to oxidation and thermal degradation, SiC and MoSi2 heating elements have a longer service life compared to other materials like graphite or pure metals, which are more prone to oxidation.
-
Comparison with Other Materials:
- Graphite: While graphite is excellent for high-temperature applications in inert or reducing atmospheres, it oxidizes rapidly in the presence of oxygen, making it unsuitable for oxidizing environments.
- Pure Metals (Tungsten, Molybdenum, Tantalum): These metals are often used in vacuum or inert atmospheres but oxidize quickly in the presence of oxygen, limiting their use in oxidizing conditions.
- Platinum: Platinum has excellent oxidation resistance but is prohibitively expensive for most industrial applications.
-
Practical Considerations for Equipment Purchasers:
- Cost vs. Performance: While SiC and MoSi2 are more expensive than some alternatives, their long service life and reliability in oxidizing atmospheres often justify the higher initial investment.
- Operational Temperature: Ensure the selected heating elements match the required operational temperature range of your furnace.
- Maintenance and Replacement: Consider the ease of maintenance and availability of replacement parts when selecting heating elements.
In conclusion, for high-temperature furnaces operating in oxidizing atmospheres, silicon carbide (SiC) and molybdenum disilicide (MoSi2) are the most suitable heating element materials due to their excellent oxidation resistance, thermal stability, and long service life. These materials ensure consistent performance and reliability, making them ideal for demanding industrial applications.
Summary Table:
Material | Max Operating Temp | Key Features | Applications |
---|---|---|---|
Silicon Carbide (SiC) | ~2700°C | Excellent oxidation resistance, high thermal conductivity, forms SiO2 layer | Ceramic sintering, glass melting, heat treatment |
Molybdenum Disilicide (MoSi2) | ~1800°C | Forms SiO2 layer, high oxidation resistance, thermal stability | Advanced ceramics, semiconductor manufacturing, high-temperature industrial uses |
Graphite | ~3000°C | Unsuitable for oxidizing atmospheres, oxidizes rapidly | Inert or reducing atmospheres |
Pure Metals (W, Mo, Ta) | ~2000-3000°C | Oxidize quickly in oxygen, limited to vacuum/inert atmospheres | Vacuum or inert environments |
Platinum | ~1700°C | Excellent oxidation resistance, but expensive | Specialized high-cost applications |
Need help selecting the right heating elements for your furnace? Contact our experts today!