Upflow and downflow furnaces each have their own advantages, and the choice between them depends on the specific installation requirements, space constraints, and heating needs of a building. Upflow furnaces are more popular due to their higher efficiency and suitability for installations in basements or low-lying areas, where rising heat can effectively warm the entire space. Downflow furnaces, on the other hand, are ideal for homes without basements or where the furnace is installed in an attic or upper level, as they push warm air downward. Both types have unique benefits, and the decision should be based on the building's layout and heating requirements.
Key Points Explained:
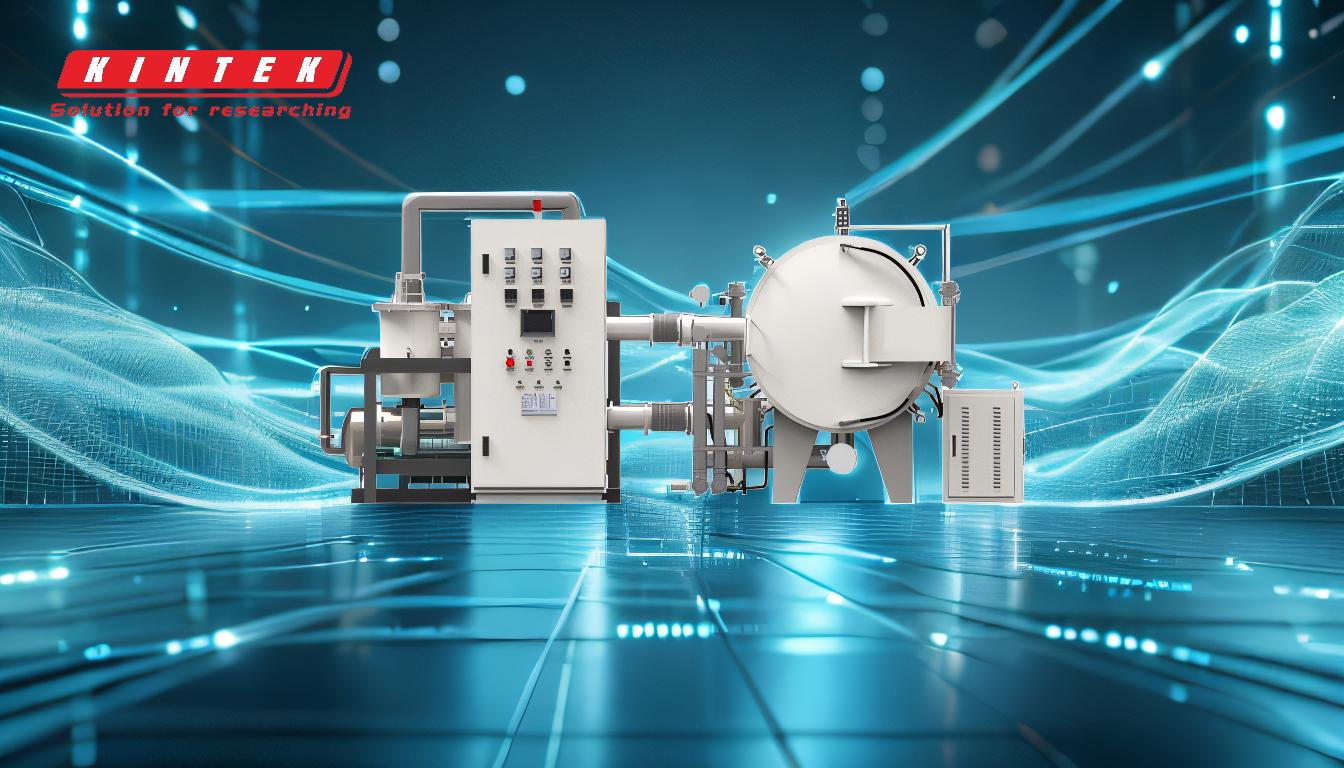
-
Upflow Furnaces:
- Efficiency: Upflow furnaces are known for their higher efficiency levels. The design allows heat to rise naturally, which aligns with the natural convection process, reducing energy waste.
- Installation Location: These furnaces are typically installed in basements or low-lying areas. The rising heat ensures that warm air is distributed evenly throughout the building, making them ideal for multi-story homes.
- Popularity: Due to their efficiency and effectiveness in heating, upflow furnaces are the most popular choice across the nation.
-
Downflow Furnaces:
- Installation Location: Downflow furnaces are better suited for homes without basements or where the furnace is installed in an attic or upper level. They push warm air downward, which is effective for single-story homes or buildings with specific architectural constraints.
- Space Utilization: These furnaces are ideal for compact spaces where vertical installation is not feasible. They are often used in mobile homes or buildings with limited basement space.
- Heating Efficiency: While downflow furnaces may not be as efficient as upflow models in certain scenarios, they are still a reliable option for specific heating needs.
-
Factors to Consider When Choosing:
- Building Layout: The decision between upflow and downflow furnaces should be based on the building's layout. Multi-story homes with basements benefit more from upflow furnaces, while single-story homes or those without basements may find downflow furnaces more suitable.
- Energy Efficiency: Upflow furnaces generally offer higher energy efficiency due to their design, which aligns with natural heat convection. However, downflow furnaces can still provide efficient heating in the right conditions.
- Installation Costs: The cost of installation may vary depending on the type of furnace and the building's structure. Upflow furnaces might require more complex ductwork in some cases, while downflow furnaces could be easier to install in certain layouts.
-
Conclusion:
- The choice between upflow and downflow furnaces ultimately depends on the specific needs of the building and its occupants. Upflow furnaces are more efficient and popular for multi-story homes with basements, while downflow furnaces are better suited for single-story homes or buildings without basements. Both types have their own advantages, and the decision should be made after considering the building's layout, heating requirements, and installation constraints.
Summary Table:
Feature | Upflow Furnace | Downflow Furnace |
---|---|---|
Efficiency | Higher efficiency, aligns with natural heat convection | Efficient in specific conditions, suitable for downward heating |
Installation Location | Basements or low-lying areas, ideal for multi-story homes | Attic or upper levels, ideal for single-story homes or buildings without basements |
Popularity | More popular due to higher efficiency and effectiveness | Less common but effective for specific layouts |
Space Utilization | Requires vertical space for installation | Ideal for compact spaces or limited basement areas |
Cost | May require complex ductwork, potentially higher installation costs | Easier to install in certain layouts, potentially lower installation costs |
Need help choosing the right furnace for your home? Contact our experts today for personalized advice!