Carbon nanotubes (CNTs) are synthesized using various methods, each with its own advantages and challenges. The primary methods include Chemical Vapor Deposition (CVD), Arc Discharge, and Laser Ablation. These methods differ in terms of scalability, purity, and the quality of CNTs produced. CVD is the most widely used due to its scalability and ability to produce high-quality CNTs, while Arc Discharge and Laser Ablation are more suited for producing CNTs with specific properties. Understanding these methods is crucial for selecting the appropriate synthesis technique based on the desired application and production scale.
Key Points Explained:
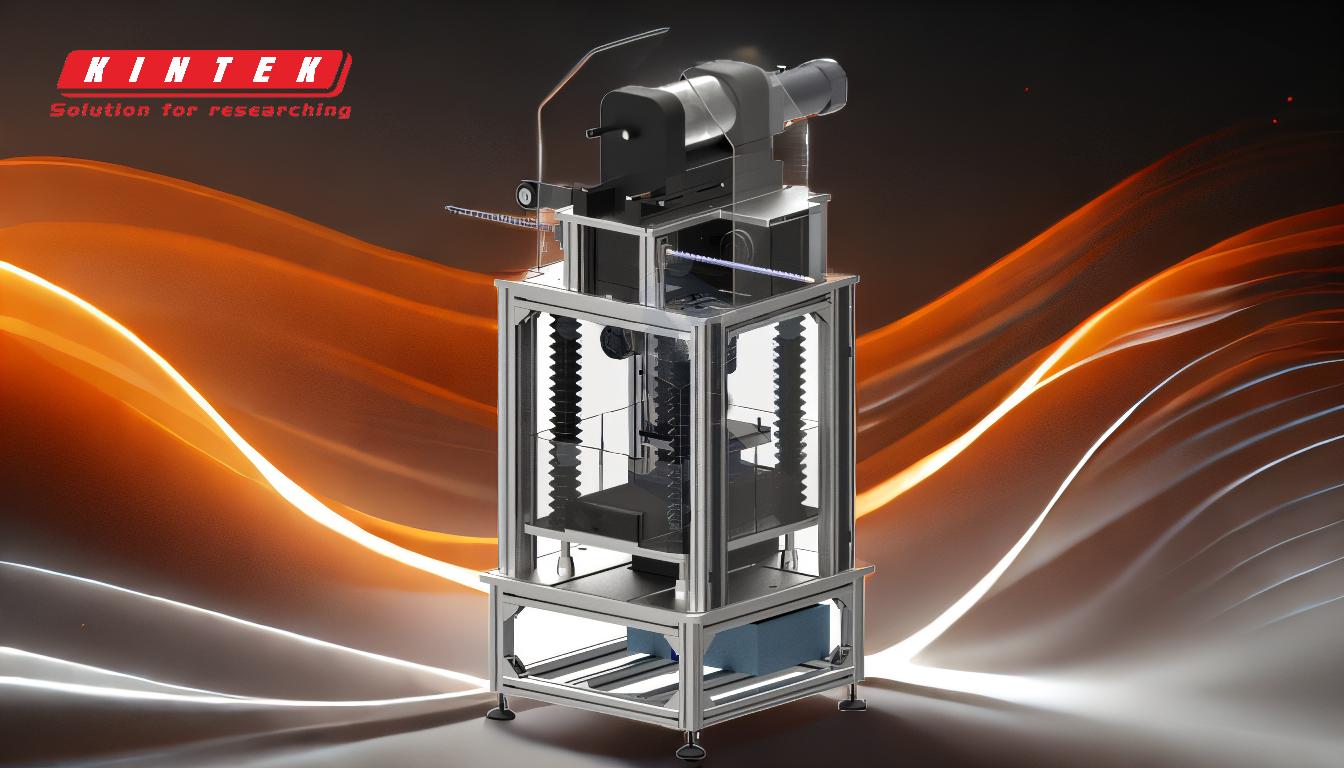
-
Chemical Vapor Deposition (CVD):
- Process: CVD involves the decomposition of hydrocarbon gases at high temperatures (600-1200°C) in the presence of a metal catalyst (e.g., iron, cobalt, or nickel). The catalyst particles facilitate the growth of CNTs from the carbon source.
-
Advantages:
- Scalable and suitable for large-scale production.
- Produces high-quality CNTs with controllable diameter and length.
- Can be used to grow CNTs on various substrates, enabling integration into devices.
-
Challenges:
- Requires precise control over temperature, pressure, and gas flow rates.
- Catalyst contamination can affect CNT purity.
- Post-processing is often needed to remove amorphous carbon and catalyst residues.
-
Arc Discharge:
- Process: Arc Discharge involves creating an electric arc between two graphite electrodes in an inert gas atmosphere (e.g., helium or argon). The high temperature of the arc vaporizes the graphite, and CNTs form on the cathode.
-
Advantages:
- Produces high-quality multi-walled CNTs (MWCNTs) and single-walled CNTs (SWCNTs).
- Relatively simple setup compared to CVD.
-
Challenges:
- Limited scalability due to the batch process nature.
- Produces a mixture of CNTs and other carbonaceous materials, requiring extensive purification.
- Energy-intensive and less controllable than CVD.
-
Laser Ablation:
- Process: Laser Ablation involves using a high-power laser to vaporize a graphite target in the presence of a metal catalyst and inert gas. The vaporized carbon condenses to form CNTs.
-
Advantages:
- Produces high-purity SWCNTs with uniform diameters.
- Suitable for producing CNTs with specific chirality, which is important for electronic applications.
-
Challenges:
- Expensive and energy-intensive due to the use of high-power lasers.
- Limited scalability and low yield compared to CVD.
- Requires post-processing to separate CNTs from other carbon by-products.
-
Comparison of Methods:
- Scalability: CVD is the most scalable method, making it the preferred choice for industrial applications. Arc Discharge and Laser Ablation are less scalable but are useful for producing CNTs with specific properties.
- Purity and Quality: CVD and Laser Ablation produce high-purity CNTs, but CVD is more controllable in terms of CNT dimensions. Arc Discharge produces a mixture of CNTs and other carbon materials, requiring extensive purification.
- Cost and Energy Efficiency: CVD is more cost-effective and energy-efficient compared to Arc Discharge and Laser Ablation, which are more expensive and energy-intensive.
-
Applications and Post-Processing:
- Applications: The choice of synthesis method depends on the intended application. For example, CVD is commonly used for producing CNTs for electronics, composites, and energy storage devices. Arc Discharge and Laser Ablation are more suited for research and specialized applications where specific CNT properties are required.
- Post-Processing: Regardless of the synthesis method, post-processing steps such as purification, functionalization, and dispersion are critical for enhancing the performance and integration of CNTs into various products. These steps ensure that the CNTs are free from impurities and can be effectively incorporated into macro-scale materials.
In conclusion, the selection of a CNT synthesis method depends on the desired application, production scale, and specific CNT properties required. CVD is the most widely used method due to its scalability and controllability, while Arc Discharge and Laser Ablation are more specialized techniques for producing CNTs with unique characteristics. Understanding these methods and their associated challenges is essential for optimizing CNT production and realizing their full potential in various applications.
Summary Table:
Method | Advantages | Challenges |
---|---|---|
Chemical Vapor Deposition (CVD) | Scalable, high-quality CNTs, controllable dimensions, substrate integration | Precise control needed, catalyst contamination, post-processing required |
Arc Discharge | High-quality MWCNTs/SWCNTs, simple setup | Limited scalability, energy-intensive, extensive purification needed |
Laser Ablation | High-purity SWCNTs, uniform diameters, specific chirality | Expensive, energy-intensive, limited scalability, post-processing required |
Need help choosing the right CNT synthesis method? Contact our experts today for tailored solutions!