Heat treatment is a controlled process used to modify the microstructure of metallic alloys, thereby altering their mechanical and physical properties. By carefully managing factors such as temperature, time, and cooling rates, heat treatment can enhance properties like hardness, strength, toughness, ductility, elasticity, wear resistance, and even magnetism. The process works by influencing the diffusion of atoms and the formation of microstructures within the metal, which directly impacts its performance characteristics. This makes heat treatment a critical step in manufacturing and engineering, enabling materials to meet specific application requirements.
Key Points Explained:
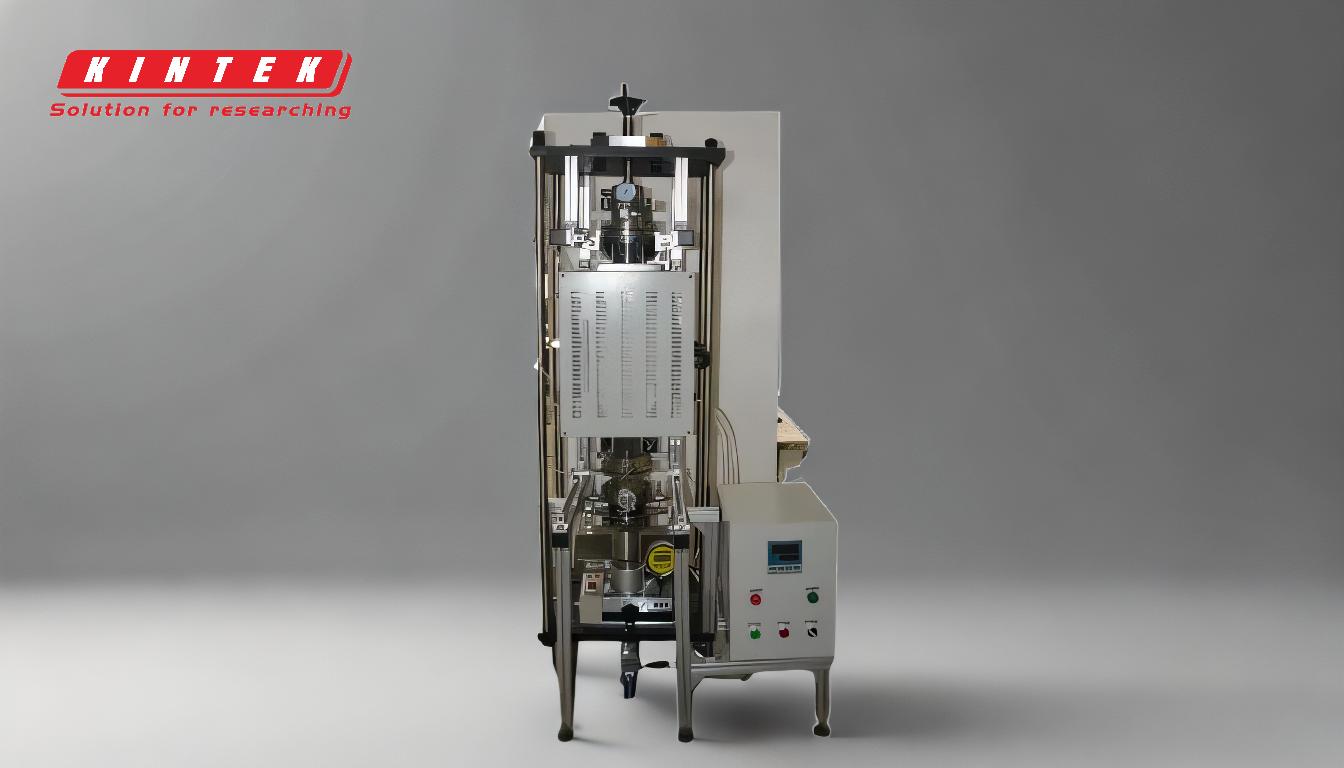
-
Microstructural Changes During Heat Treatment
- Heat treatment involves heating the metal to a specific temperature and then cooling it at a controlled rate.
- This process causes changes in the metal's microstructure, such as the formation of new phases (e.g., martensite in steel) or the redistribution of atoms.
- These microstructural changes directly influence the material's mechanical properties, such as hardness and strength.
-
Control of Diffusion and Cooling Rates
- The rate of diffusion (movement of atoms within the metal) determines how quickly new phases or structures form.
- Faster cooling rates (e.g., quenching) can create harder but more brittle structures, while slower cooling (e.g., annealing) results in softer, more ductile materials.
- By adjusting these rates, engineers can tailor the material's properties to specific needs.
-
Enhanced Mechanical Properties
- Hardness and Strength: Heat treatment can increase hardness and strength by forming harder microstructures, such as martensite in steel.
- Toughness and Ductility: Processes like tempering can reduce brittleness while maintaining strength, improving toughness and ductility.
- Elasticity and Wear Resistance: Heat treatment can refine grain structures, enhancing elasticity and resistance to wear and fatigue.
-
Applications in Industry
- Heat treatment is widely used in industries such as automotive, aerospace, and construction to improve the performance and longevity of components.
- For example, gears, shafts, and cutting tools are often heat-treated to achieve the desired balance of hardness and toughness.
-
Physical Property Modifications
- Beyond mechanical properties, heat treatment can also alter physical properties like magnetism (permeability) and thermal conductivity.
- This makes it a versatile process for applications requiring specific electrical or magnetic characteristics.
By understanding and controlling the heat treatment process, manufacturers can optimize material properties to meet the demands of various applications, ensuring durability, efficiency, and performance.
Summary Table:
Key Aspect | Description |
---|---|
Microstructural Changes | Heating and cooling alter metal phases, influencing hardness and strength. |
Diffusion & Cooling Rates | Faster cooling increases hardness; slower cooling enhances ductility. |
Mechanical Properties | Improves hardness, strength, toughness, elasticity, and wear resistance. |
Industrial Applications | Used in automotive, aerospace, and construction for durable, high-performance parts. |
Physical Property Changes | Modifies magnetism and thermal conductivity for specialized applications. |
Optimize your materials with expert heat treatment solutions—contact us today!