Alumina (Aluminum Oxide, Al2O3) is widely used in furnaces due to its exceptional combination of properties, making it ideal for high-temperature and demanding industrial environments. Its high refractoriness, chemical inertness, thermal stability, and mechanical strength allow it to withstand extreme temperatures (up to 1800°C) and harsh conditions without degrading. Alumina is used in furnace linings, crucibles, tubes, and insulation due to its resistance to thermal shock, wear, and corrosion. Additionally, its electrical insulation properties and lightweight nature make it suitable for specialized applications like thermocouple protection and muffle furnaces. These attributes ensure durability, longevity, and reliability in continuous and high-temperature furnace operations.
Key Points Explained:
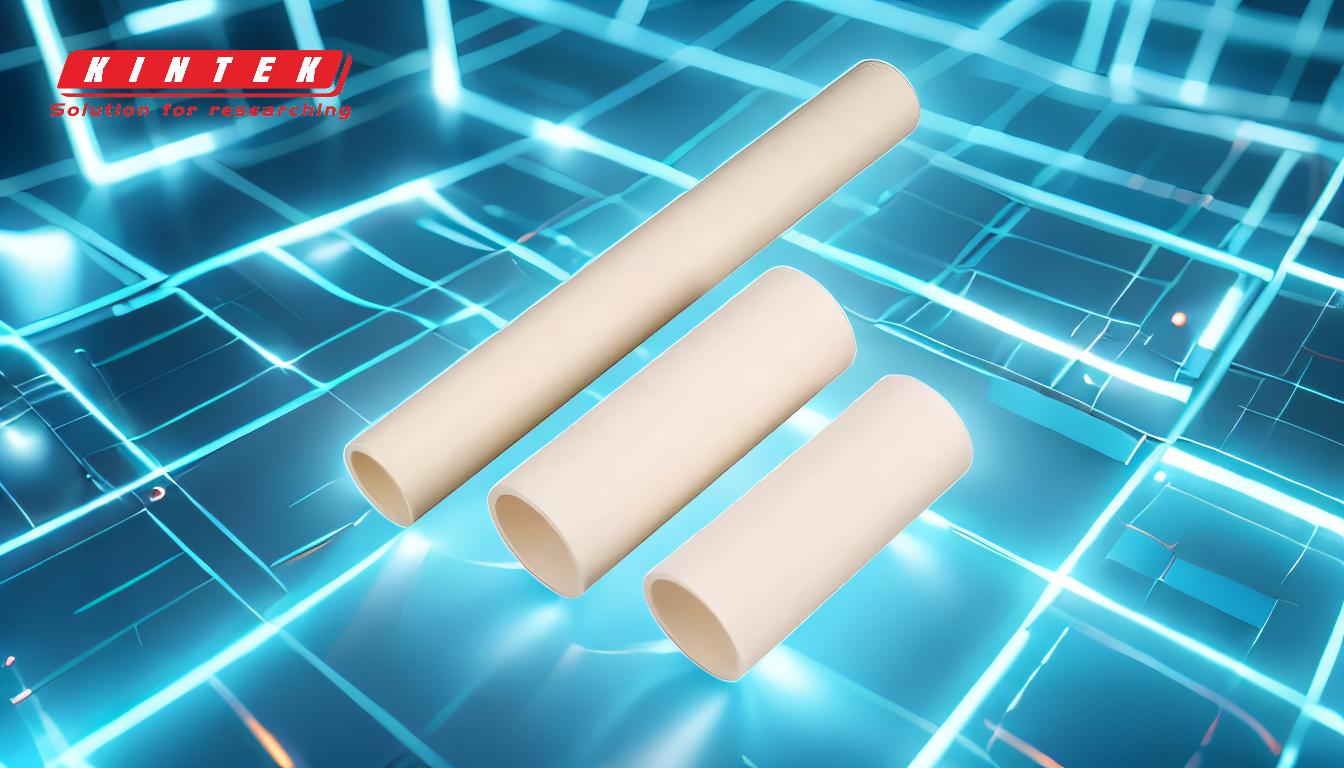
-
High Temperature Resistance:
- Alumina can withstand extreme temperatures, up to 1800°C, making it suitable for high-temperature furnace applications.
- Its high temperature stability ensures that it maintains structural integrity and performance even under prolonged exposure to heat.
- This property is critical for furnace linings, crucibles, and tubes, where materials must endure intense thermal conditions without melting or degrading.
-
Refractoriness:
- Alumina's high refractoriness (ability to resist heat and maintain strength at high temperatures) makes it ideal for use in furnaces, kilns, and other high-temperature environments.
- It is commonly used in the hot-face lining of sintering furnaces, blast furnaces, cement kilns, and glass tanks.
- The material's ability to retain its properties at high temperatures ensures consistent performance and longevity.
-
Chemical Inertness and Corrosion Resistance:
- Alumina is exceptionally inert, meaning it does not react with most chemicals, even at high temperatures.
- This makes it resistant to corrosion and chemical attack, which is crucial in environments where corrosive gases or materials are present.
- Its chemical resistance ensures that alumina components, such as crucibles and furnace linings, remain durable and unaffected by harsh substances.
-
Mechanical Strength and Durability:
- Alumina exhibits high compression strength and wear resistance, even at elevated temperatures.
- This mechanical robustness allows it to withstand physical stress, abrasion, and erosion in demanding furnace applications.
- As a result, alumina components like tubes and linings have a longer lifespan compared to materials like quartz.
-
Thermal Stability and Low Thermal Conductivity:
- Alumina has excellent thermal stability, meaning it does not undergo significant dimensional changes or degradation when exposed to thermal cycling.
- Its low thermal conductivity helps in insulating furnaces, reducing heat loss, and improving energy efficiency.
- These properties are particularly beneficial in muffle furnaces and other applications requiring precise temperature control.
-
Electrical Insulation:
- Alumina provides good electrical insulation, even at high temperatures, making it suitable for applications involving electricity or electronics.
- This property is essential for components like thermocouple protection tubes, where electrical insulation is required to ensure accurate temperature measurements.
-
Lightweight and Versatile:
- Alumina fiber and other forms of alumina are lightweight, which reduces the overall weight of furnace components.
- Its versatility allows it to be used in various forms, such as tubes, crucibles, linings, and insulation, catering to a wide range of furnace designs and requirements.
-
Resistance to Thermal Shock:
- While alumina is less resistant to thermal shock compared to some materials, its performance in continuous furnaces (where thermal shock is minimal) is exceptional.
- In applications where thermal cycling is not extreme, alumina components can last for many years without failure.
-
Applications in Furnaces:
- Crucibles: Alumina crucibles are used for melting and holding high-temperature materials due to their refractoriness and chemical resistance.
- Furnace Linings: High-purity alumina is used in the hot-face lining of sintering furnaces and other high-temperature furnaces.
- Tubes: Alumina tubes are preferred over quartz tubes for their durability and ability to handle higher temperatures.
- Insulation: Alumina fiber is used in muffle furnaces for its lightweight and insulating properties.
-
Economic and Operational Benefits:
- The durability and longevity of alumina reduce maintenance costs and downtime, making it a cost-effective choice for furnace applications.
- Its ability to perform reliably under extreme conditions ensures consistent furnace operation, which is critical for industrial processes.
In summary, alumina's unique combination of high temperature resistance, chemical inertness, mechanical strength, and thermal stability makes it an indispensable material for furnace applications. Its properties ensure durability, efficiency, and reliability, making it a preferred choice for high-temperature industrial environments.
Summary Table:
Property | Description |
---|---|
High Temperature Resistance | Withstands up to 1800°C, ideal for furnace linings, crucibles, and tubes. |
Refractoriness | Maintains strength and performance at high temperatures. |
Chemical Inertness | Resists corrosion and chemical attack, ensuring durability. |
Mechanical Strength | High compression strength and wear resistance, even at elevated temperatures. |
Thermal Stability | Low thermal conductivity and excellent dimensional stability under heat. |
Electrical Insulation | Provides insulation at high temperatures, suitable for thermocouple protection. |
Lightweight & Versatile | Reduces furnace weight and adapts to various forms like tubes and insulation. |
Applications | Used in crucibles, furnace linings, tubes, and insulation for muffle furnaces. |
Upgrade your furnace performance with alumina components—contact our experts today to learn more!