Controlled atmosphere technology is crucial in various industries, particularly in storage and heat treatment processes, due to its ability to precisely regulate environmental conditions. By controlling the concentration of gases such as oxygen, carbon dioxide, and inert gases, it prevents contamination, oxidation, and unwanted chemical reactions. This ensures the preservation of material properties, enhances product quality, and improves operational efficiency. Additionally, controlled atmospheres contribute to energy savings, environmental safety, and cost-effectiveness by reducing waste and minimizing the risk of fire or explosions. Overall, controlled atmospheres play a vital role in maintaining the integrity and performance of materials and products across multiple applications.
Key Points Explained:
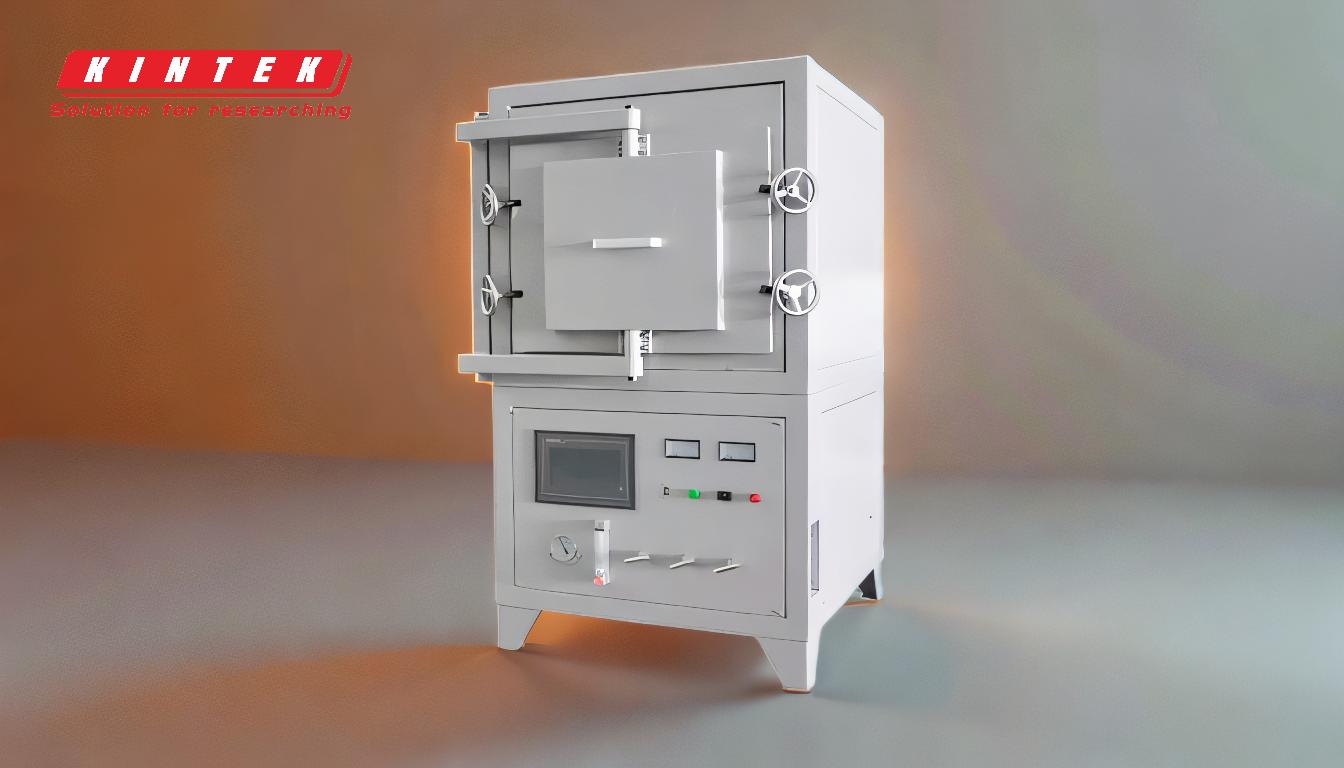
-
Prevention of Contamination and Oxidation
- Controlled atmospheres are essential in preventing contamination and oxidation, which can degrade the quality of materials. For example, in heat treatment processes, maintaining a controlled environment ensures that alloys retain their properties, such as strength, ductility, and dimensional stability.
- In storage applications, reducing oxygen levels inhibits the growth of insects and molds, preserving the quality of stored grains or other perishable materials.
-
Enhanced Material Properties
- Controlled atmosphere heat treatment alters the microstructure of metals, improving their strength, toughness, and resistance to wear and corrosion. This is achieved by carefully controlling the heating and cooling processes in an environment free from contaminants.
- For example, carburizing and tempering processes benefit from controlled atmospheres, as they ensure consistent and high-quality results.
-
Energy Efficiency and Cost Savings
- Controlled atmosphere systems are designed to be energy-efficient, reducing operating costs. They provide thermal homogeneity and precise temperature control, which minimizes energy waste.
- The ability to heat parts of any shape or size further enhances efficiency, making the process adaptable to various industrial needs.
-
Environmental and Safety Benefits
- Controlled atmosphere furnaces eliminate the use of toxic substances like cyanides, reducing the risk of land contamination and simplifying waste disposal.
- Inert atmospheres reduce the risk of fire and explosions, creating a safer working environment. They also slow down oxidation processes, protecting materials from damage.
-
Improved Product Quality and Consistency
- By controlling the composition and flow of gases, controlled atmosphere furnaces ensure minimal oxidation or decarburization. This results in consistent product quality and reduces the risk of defects or damage to the alloy.
- The precise control over environmental conditions also increases production efficiency, as it minimizes the need for rework or quality control adjustments.
-
Versatility in Applications
- Controlled atmosphere technology is versatile and can be applied to various processes, including storage, heat treatment, and material fabrication. It is suitable for industries ranging from food storage to aerospace manufacturing.
- For instance, in labs, controlled atmosphere furnaces enable chemical inertness or reactivity, ensuring successful material fabrication and experimentation.
-
Reduction of Chemical Reactions
- Inert atmospheres slow down or prevent unwanted chemical reactions, such as oxidation, which can compromise the integrity of materials. This is particularly important in processes involving reactive metals or sensitive compounds.
- By reducing reaction rates, controlled atmospheres extend the lifespan of materials and improve their performance.
In summary, controlled atmosphere technology is indispensable for maintaining material integrity, enhancing product quality, and ensuring operational efficiency across a wide range of industries. Its ability to prevent contamination, oxidation, and unwanted chemical reactions, while also providing energy savings and environmental benefits, makes it a critical component in modern industrial processes.
Summary Table:
Key Benefits | Description |
---|---|
Prevents Contamination & Oxidation | Maintains material quality by controlling gas concentrations. |
Enhances Material Properties | Improves strength, toughness, and corrosion resistance. |
Energy Efficiency & Cost Savings | Reduces energy waste and operating costs. |
Environmental & Safety Benefits | Minimizes toxic substances and reduces fire risks. |
Improved Product Quality | Ensures consistent results with minimal oxidation or defects. |
Versatility in Applications | Suitable for storage, heat treatment, and material fabrication across industries. |
Learn how controlled atmosphere technology can transform your processes—contact us today!