Hydrogen is widely used in furnaces, particularly in heat treatment processes, due to its unique properties and benefits. Its primary role is to prevent oxidation of metals like iron and steel during high-temperature treatments, ensuring a clean and bright surface finish. Hydrogen's high thermal conductivity allows for rapid heating and cooling, making it efficient for processes like annealing, sintering, and brazing. Additionally, it acts as a reducing agent, lowering oxygen content and preventing corrosion. However, challenges such as the risk of hydrogen explosions, hydrogen embrittlement, and the need for high purity graphite crucible must be carefully managed.
Key Points Explained:
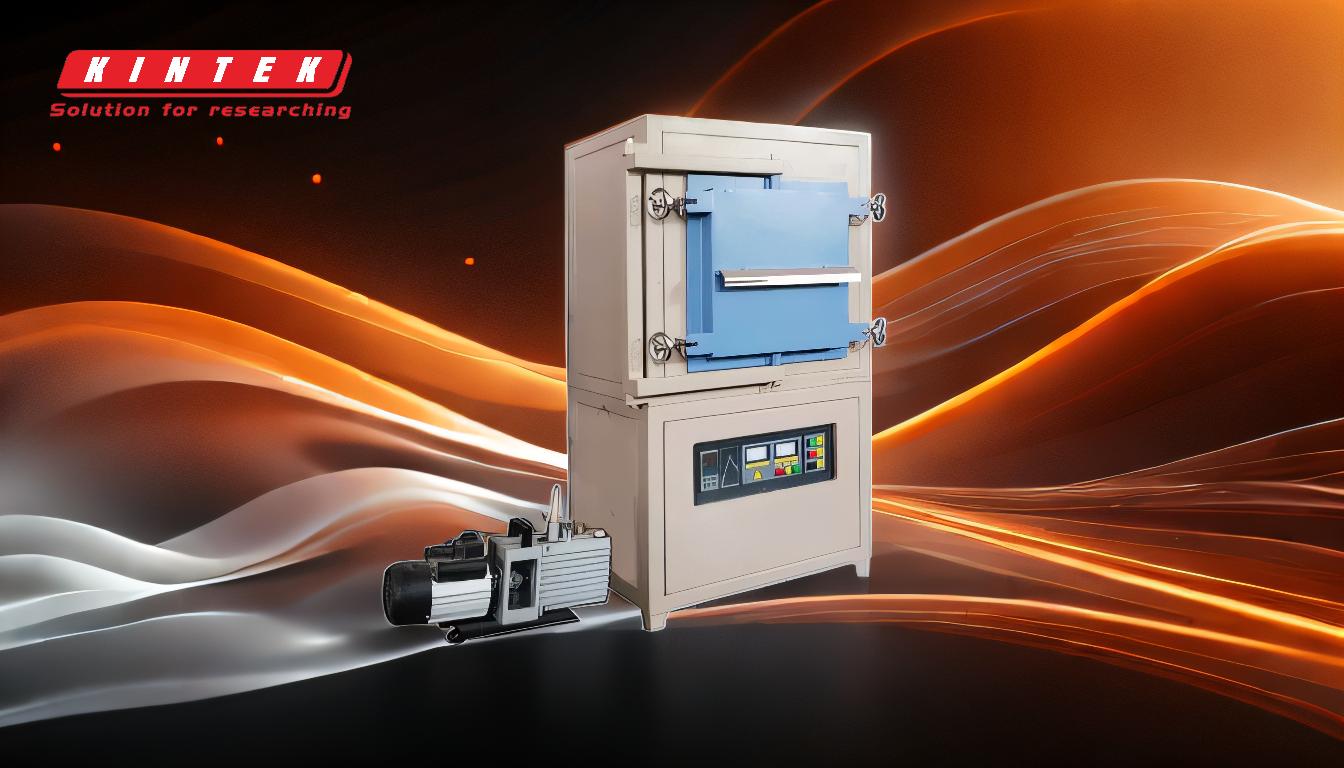
-
Prevention of Oxidation:
- Hydrogen is used in furnaces to create a controlled atmosphere that prevents oxidation of metals like iron and steel during heat treatment.
- In processes like bright annealing, metals are heated in a hydrogen-rich environment and then slowly cooled, resulting in a clean, oxide-free surface.
-
High Thermal Conductivity:
- Hydrogen has a thermal conductivity seven times higher than air, enabling rapid heating and cooling of materials.
- This property is particularly beneficial for processes requiring precise temperature control, such as annealing and sintering.
-
Reducing Atmosphere:
- Hydrogen acts as a strong deoxidizer, reducing the oxygen content in the furnace atmosphere.
- This prevents corrosion and ensures the integrity of the metal surface during high-temperature treatments.
-
Applications in Heat Treatment:
- Hydrogen atmosphere furnace are used for annealing stainless steel alloys, magnetic steel alloys, and sintering processes.
- It is also employed in copper brazing and other high-temperature material processing applications.
-
Challenges and Risks:
- Hydrogen Embrittlement: Prolonged exposure to hydrogen can make certain steels brittle, reducing their lifespan.
- Explosion Risk: Hydrogen is highly flammable, requiring strict safety measures to prevent accidents.
- Purity Requirements: High-purity hydrogen (98-99.9%) is necessary to avoid contamination from impurities like water vapor, oxygen, and trace gases.
-
Material Compatibility:
- While hydrogen is effective for many metals, it can cause decarburization in high-carbon steels, altering their properties.
- Proper selection of materials and process parameters is essential to mitigate these effects.
-
Specialized Furnace Design:
- Hydrogen atmosphere furnaces are designed to handle the unique requirements of hydrogen use, including safety features and precise temperature control.
- These furnaces are used for drying, sintering, and annealing in hydrogen or inert gas environments.
By leveraging hydrogen's unique properties, furnaces can achieve efficient and high-quality heat treatment processes, though careful management of its risks and limitations is essential.
Summary Table:
Key Aspect | Details |
---|---|
Prevention of Oxidation | Creates a controlled atmosphere to prevent oxidation of metals. |
High Thermal Conductivity | Enables rapid heating and cooling, ideal for annealing and sintering. |
Reducing Atmosphere | Acts as a deoxidizer, reducing oxygen content and preventing corrosion. |
Applications | Annealing, sintering, brazing, and high-temperature material processing. |
Challenges | Hydrogen embrittlement, explosion risks, and high-purity requirements. |
Material Compatibility | Effective for many metals but may cause decarburization in high-carbon steels. |
Furnace Design | Specialized designs for safety and precise temperature control. |
Learn how hydrogen can enhance your heat treatment processes—contact our experts today for tailored solutions!