Oxygen is used in brazing primarily to control the atmosphere within the brazing furnace, ensuring that oxides do not form on the metal surfaces. This is crucial because oxides can prevent the filler metal from properly wetting and bonding with the base metals, leading to weak or defective joints. By carefully managing the oxygen levels, either by reducing it or using it in combination with other gases, the brazing process can achieve a clean, oxide-free surface. This enhances the flow and adhesion of the filler metal, resulting in stronger, more reliable joints. Additionally, a controlled atmosphere reduces the need for excessive flux, simplifying the process and improving the quality of the brazed components.
Key Points Explained:
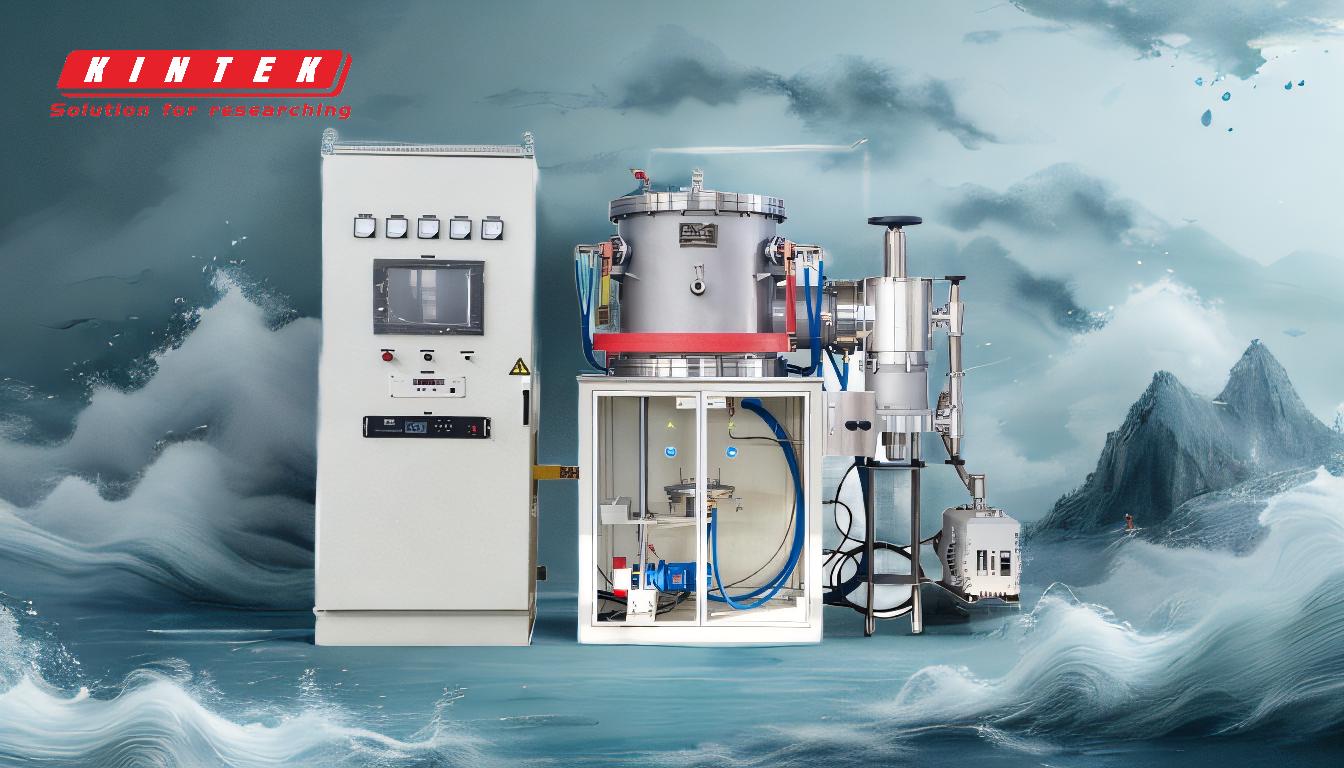
-
Prevention of Oxide Formation:
- Why it matters: Oxides on metal surfaces can act as barriers, preventing the filler metal from properly wetting and bonding with the base metals.
- How oxygen helps: By controlling the atmosphere in the brazing furnace, oxygen levels can be adjusted to minimize the formation of oxides. This ensures that the metal surfaces remain clean and receptive to the filler metal.
-
Enhanced Wetting and Flow of Filler Metal:
- Why it matters: Proper wetting and flow of the filler metal are essential for forming strong, durable joints.
- How oxygen helps: A controlled atmosphere, which may include oxygen in specific concentrations, helps maintain a clean surface, allowing the filler metal to spread evenly and bond effectively with the base metals.
-
Reduction of Flux Requirement:
- Why it matters: Flux is used to remove oxides and other impurities, but excessive use can complicate the brazing process and leave residues that may affect the joint's integrity.
- How oxygen helps: By minimizing oxide formation, a controlled atmosphere reduces the need for large amounts of flux, simplifying the process and improving the quality of the brazed joints.
-
Improved Joint Quality and Reliability:
- Why it matters: The ultimate goal of brazing is to create joints that are strong, durable, and reliable under the intended operating conditions.
- How oxygen helps: By ensuring a clean, oxide-free surface and optimal wetting conditions, oxygen in the brazing atmosphere contributes to the formation of high-quality joints that meet the required performance standards.
In summary, oxygen plays a critical role in brazing by helping to control the furnace atmosphere, preventing oxide formation, enhancing the wetting and flow of the filler metal, and reducing the need for flux. These factors collectively contribute to the creation of strong, reliable brazed joints.
Summary Table:
Key Role of Oxygen in Brazing | Benefits |
---|---|
Prevents Oxide Formation | Ensures clean metal surfaces for better bonding. |
Enhances Filler Metal Wetting | Improves flow and adhesion for stronger joints. |
Reduces Flux Requirement | Simplifies the process and minimizes residues. |
Improves Joint Quality | Creates durable, reliable brazed joints. |
Optimize your brazing process with controlled atmospheres—contact our experts today!