Pyrolysis is an advanced thermal decomposition process that converts organic materials into valuable products like biochar, bio-oil, and syngas. However, it is often considered expensive due to several factors, including high capital and operational costs, energy requirements, feedstock preparation, and maintenance. The initial investment in a pyrolysis plant is significant, as it involves purchasing specialized equipment and ensuring compliance with environmental regulations. Additionally, operational costs such as energy consumption, labor, and feedstock processing contribute to the overall expense. Maintenance and repair of pyrolysis equipment, along with the need for consistent feedstock quality, further increase costs. Despite these challenges, pyrolysis offers environmental and economic benefits, making it a viable option for waste management and resource recovery when optimized.
Key Points Explained:
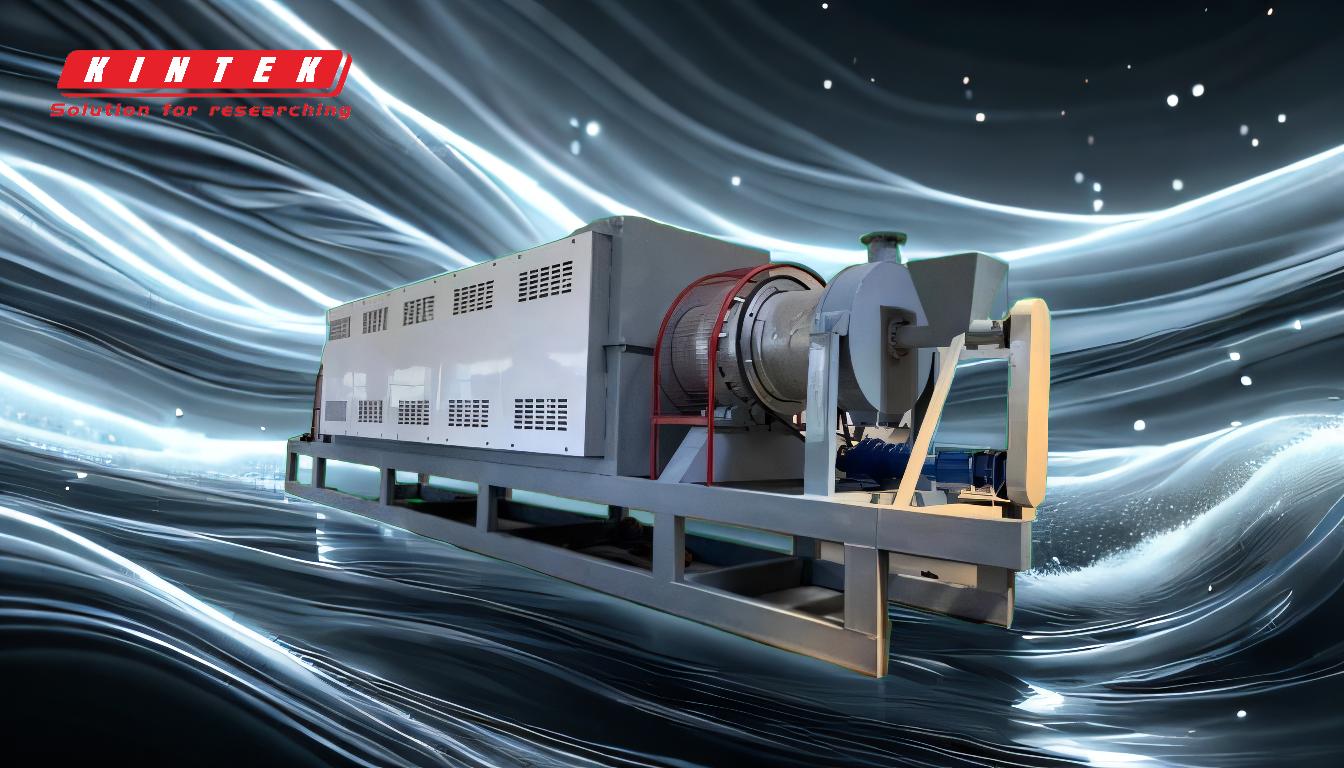
-
High Capital Costs:
- Building a pyrolysis plant requires substantial upfront investment. The equipment needed, such as reactors, condensers, and gas cleaning systems, is highly specialized and expensive.
- Infrastructure development, including land acquisition, construction, and installation, adds to the initial costs.
- Compliance with environmental and safety regulations further increases capital expenditure.
-
Operational Expenses:
- Energy consumption is a major operational cost. Pyrolysis requires high temperatures (typically 400–800°C), which demand significant energy input, often from external sources.
- Labor costs are another factor, as skilled personnel are needed to operate and monitor the plant.
- Feedstock processing, including collection, sorting, and pre-treatment (e.g., drying or shredding), adds to operational expenses.
-
Feedstock Quality and Availability:
- The efficiency and cost-effectiveness of pyrolysis depend heavily on the quality and consistency of the feedstock. Contaminated or inconsistent feedstock can reduce yield and increase processing costs.
- Sourcing sufficient quantities of suitable feedstock can be challenging and costly, especially in regions with limited waste availability.
-
Maintenance and Repair:
- Pyrolysis equipment is subject to wear and tear due to high temperatures and corrosive byproducts, necessitating regular maintenance and occasional repairs.
- Downtime for maintenance can disrupt operations and reduce overall productivity, further increasing costs.
-
Environmental and Regulatory Compliance:
- Pyrolysis plants must adhere to strict environmental regulations to control emissions and manage waste byproducts. This often requires additional equipment, such as scrubbers and filters, increasing costs.
- Obtaining permits and ensuring compliance with local, national, and international standards can be time-consuming and expensive.
-
Technological Challenges:
- Pyrolysis technology is still evolving, and many plants face challenges in scaling up operations or achieving consistent product quality.
- Research and development costs to improve efficiency and reduce costs can be significant, especially for smaller operators.
-
Market and Economic Factors:
- The economic viability of pyrolysis depends on the market demand and pricing for its end products (biochar, bio-oil, syngas). Fluctuations in market prices can impact profitability.
- Competition from other waste management and energy production technologies can also affect the financial feasibility of pyrolysis projects.
In summary, while pyrolysis offers significant environmental benefits and the potential for resource recovery, its high costs are driven by capital investment, operational expenses, feedstock challenges, and regulatory requirements. Addressing these factors through technological advancements, economies of scale, and supportive policies could make pyrolysis more cost-effective in the future.
Summary Table:
Cost Factor | Description |
---|---|
High Capital Costs | Specialized equipment, infrastructure, and regulatory compliance increase costs. |
Operational Expenses | Energy consumption, labor, and feedstock processing add to ongoing costs. |
Feedstock Quality | Inconsistent or contaminated feedstock reduces efficiency and increases costs. |
Maintenance and Repair | High temperatures and corrosive byproducts necessitate frequent maintenance. |
Regulatory Compliance | Emissions control and permits require additional equipment and time. |
Technological Challenges | Scaling up and improving efficiency involve significant R&D costs. |
Market Factors | Fluctuating product prices and competition impact profitability. |
Discover how to optimize pyrolysis costs for your project—contact our experts today!