Creating a vacuum in the chamber before thermal evaporation is essential for achieving high-quality thin film deposition. The vacuum environment ensures that material atoms can evaporate and travel freely without interference from air molecules, allowing them to coat the substrate effectively. This process prevents collisions between evaporated molecules and residual gas molecules, which could degrade the quality of the deposited film. Additionally, a high vacuum environment ensures a long mean free path for the evaporated atoms, enabling them to reach the substrate in a straight line without scattering. This results in a clean, stable, and uniform thin film on the substrate.
Key Points Explained:
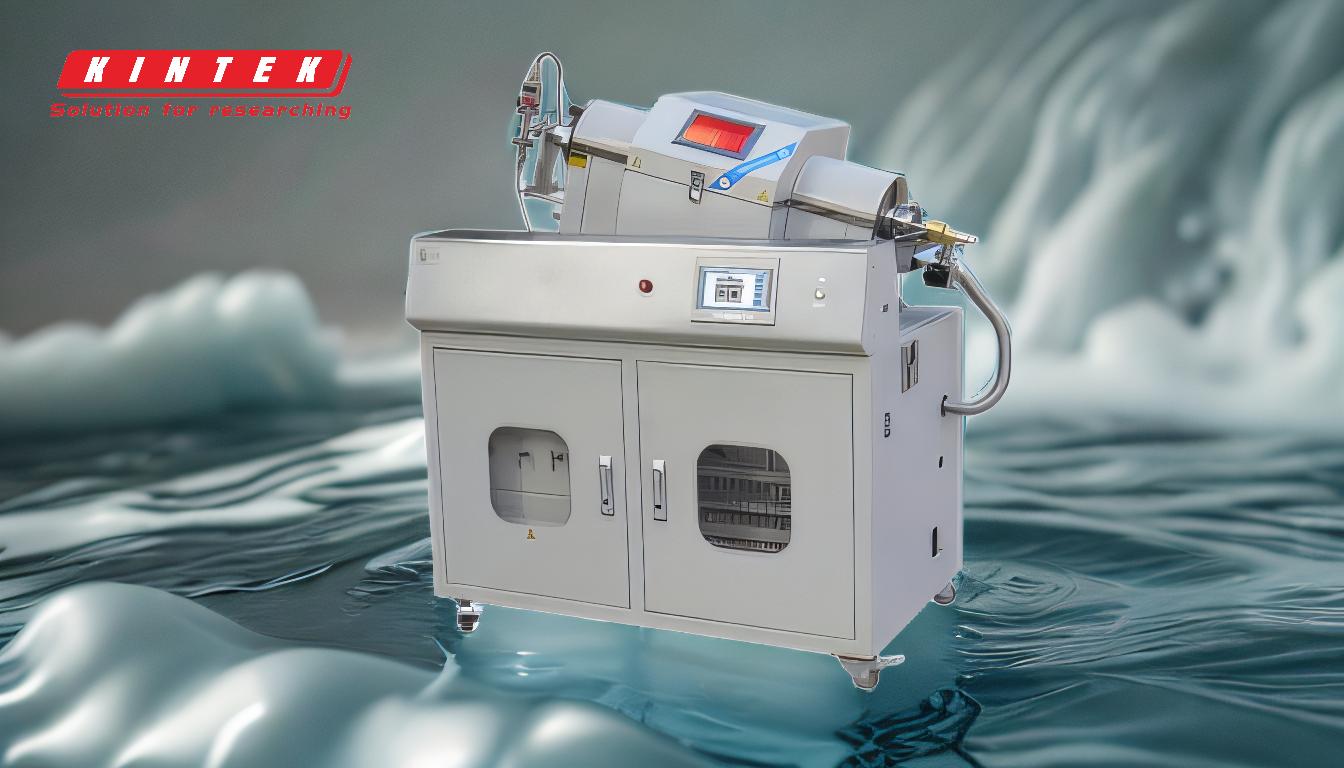
-
Preventing Interference from Air Molecules:
- In a vacuum environment, air molecules are removed, ensuring that the material atoms can evaporate and travel freely without colliding with gas molecules. This interference-free environment is crucial for achieving a high-quality thin film deposition.
- If air molecules were present, they could collide with the evaporated material atoms, causing them to scatter and potentially degrade the quality of the deposited film.
-
Ensuring a Long Mean Free Path:
- The mean free path is the average distance a molecule travels before colliding with another molecule. In a high vacuum environment (typically 10^-5 to 10^-7 Torr), the mean free path of the evaporated atoms is significantly longer than the distance from the source to the substrate.
- This long mean free path ensures that the evaporated atoms can travel in a straight line to the substrate without being scattered by residual gas molecules, resulting in a more uniform and high-quality thin film.
-
Facilitating Effective Substrate Coating:
- A high vacuum environment allows even materials with low vapor pressure to produce a vapor cloud, which then coats the substrate surface as a thin film. This is particularly important for materials that require precise and uniform deposition.
- Without a vacuum, the evaporated atoms might not stick well to the substrate, leading to an unstable and non-uniform film.
-
Providing Clean Surfaces for Deposition:
- A vacuum environment ensures that the substrate and the evaporated material are free from contaminants. This clean environment is essential for the evaporated atoms to adhere properly to the substrate, forming a stable and durable thin film.
- Residual gases in the chamber could react with the evaporated material or the substrate, leading to impurities and defects in the deposited film.
-
Maintaining Controlled Deposition Conditions:
- The vacuum environment allows for precise control over the deposition process, including the rate of evaporation and the uniformity of the film. This control is crucial for applications that require specific film properties, such as thickness, composition, and structure.
- By maintaining a high vacuum, the process can be optimized to achieve the desired film characteristics, ensuring consistency and reproducibility in the deposition process.
In summary, creating a vacuum in the chamber before thermal evaporation is essential for preventing interference from air molecules, ensuring a long mean free path for evaporated atoms, facilitating effective substrate coating, providing clean surfaces for deposition, and maintaining controlled deposition conditions. These factors collectively contribute to the production of high-quality, uniform, and stable thin films.
Summary Table:
Key Benefit | Explanation |
---|---|
Prevents Interference | Removes air molecules, allowing material atoms to travel freely without collisions. |
Ensures Long Mean Free Path | Evaporated atoms travel in a straight line, ensuring uniform and high-quality films. |
Facilitates Effective Coating | Enables precise and uniform deposition, even for low vapor pressure materials. |
Provides Clean Surfaces | Eliminates contaminants, ensuring stable and durable thin films. |
Maintains Controlled Conditions | Allows precise control over deposition, ensuring consistent and reproducible results. |
Ready to optimize your thin film deposition process? Contact us today to learn more!