Brazing is often chosen over soldering due to its ability to create stronger, more durable joints that are as strong as the base metals themselves. This makes it ideal for applications requiring high reliability and strength, such as in cookware, automotive, and HVAC systems. Additionally, brazing maintains a clean appearance and prevents oxidation, especially in vacuum brazing processes. It also allows for complex geometries and consistent joint quality, making it versatile for various industrial applications. Furthermore, brazing is particularly advantageous for materials like cast iron, as it minimizes heating, preserves material properties, and reduces the risk of cracking.
Key Points Explained:
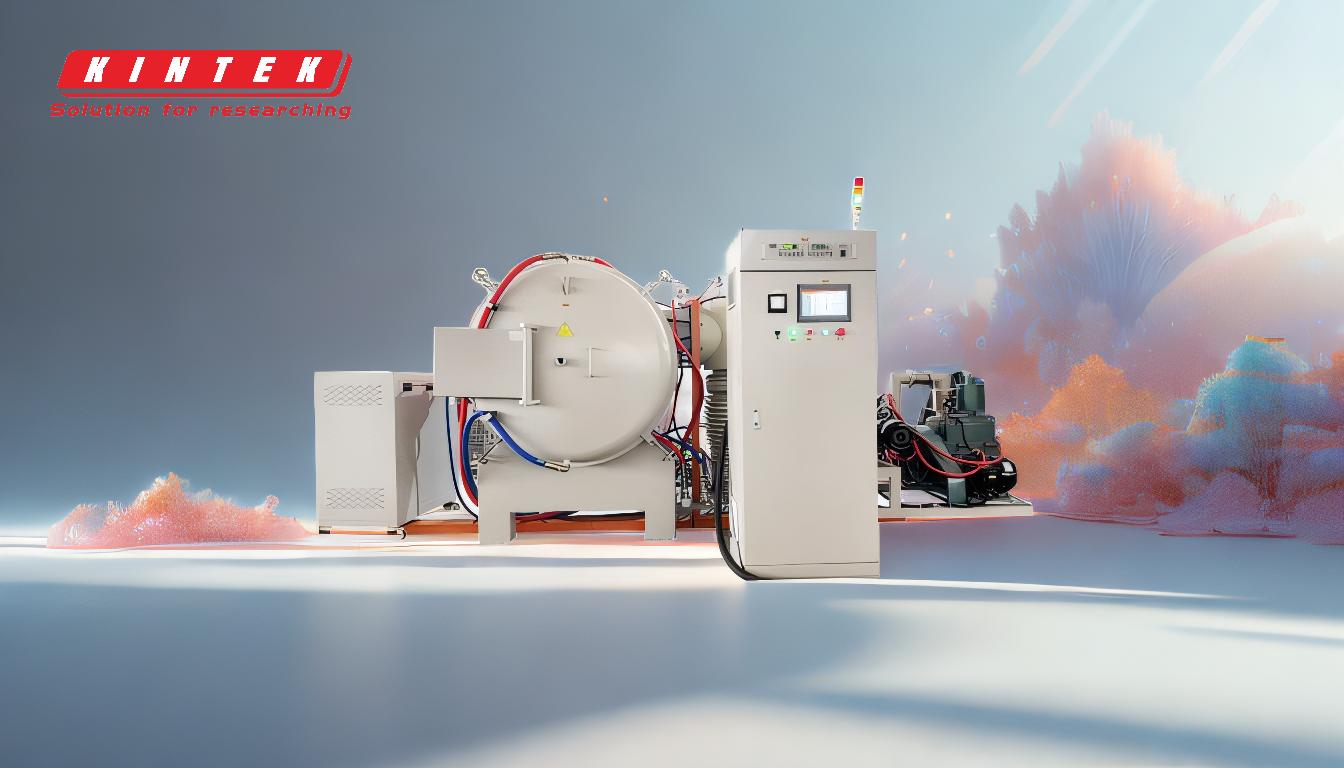
-
Strength of Joints:
- Brazing creates joints that are as strong as the base metals, unlike soldering, which typically produces weaker joints. This makes brazed joints more suitable for applications requiring high durability and reliability, such as in automotive and HVAC systems.
-
Versatility Across Industries:
- Brazing is widely used in various industries, including cookware, automotive, and HVAC systems. Its ability to join different metals and withstand high temperatures makes it a versatile and preferred choice for many industrial applications.
-
Clean Appearance and Oxidation Prevention:
- Unlike soldering, vacuum brazing keeps the finished part free from oxidation, maintaining a clean and aesthetically pleasing appearance. This is particularly important in industries where the visual quality of the product is crucial.
-
Complex Joining Geometries:
- Brazing allows for the joining of complex geometries that might be challenging with soldering. This capability is essential in industries that require intricate and precise metal joining, such as aerospace and electronics.
-
Consistency in Joint Quality:
- Brazed parts exhibit high joint strength and excellent part-to-part consistency in both appearance and size. This consistency ensures reliable performance and reduces the need for rework or quality control issues.
-
Advantages for Cast Iron:
- Brazing cast iron offers significant benefits, including limited heating that prevents the base metal from reaching its melting temperature. This preserves the material's properties and reduces the risk of cracking, making brazing a safer and more effective method for joining cast iron components.
-
Filling Large Lap Joints:
- Brazing allows for the filling of large lap joints without the need for external welds. This capability is particularly useful in applications where strong, seamless joints are required, such as in heavy machinery and structural components.
By considering these key points, it becomes clear why brazing is often preferred over soldering for applications requiring strong, durable, and reliable metal joints.
Summary Table:
Key Advantage | Description |
---|---|
Strength of Joints | Joints as strong as base metals, ideal for high-reliability applications. |
Versatility Across Industries | Used in cookware, automotive, HVAC, and more for joining diverse metals. |
Clean Appearance | Prevents oxidation, maintaining a clean and aesthetically pleasing finish. |
Complex Geometries | Enables precise joining of intricate shapes, essential for aerospace/electronics. |
Consistent Joint Quality | Ensures high joint strength and uniformity, reducing rework. |
Advantages for Cast Iron | Minimizes heating, preserves material properties, and reduces cracking risks. |
Filling Large Lap Joints | Creates strong, seamless joints without external welds. |
Looking for reliable brazing solutions? Contact our experts today to enhance your metal joining processes!