Table of Contents
- Overview of Cold Isostatic Pressing
- Types of Cold Isostatic Pressing
- Advantages of Cold Isostatic Pressing over Uniaxial Die Pressing
- Cold Isostatic Pressing in Complex-Shaped Component Production
- Process of Cold Isostatic Pressing
- Advantages of Cold Isostatic Pressing for Alumina Ceramics
- Disadvantages of Cold Isostatic Pressing for Ceramics
- Applications of Cold Isostatic Pressing
- Alternative Compression Technologies
- Conclusion
Cold Isostatic Pressing (CIP) is a widely used manufacturing process in various industries, including ceramics, metalworking, and pharmaceuticals. It involves applying equal pressure from all directions to a material placed inside a flexible mold or bag. This process helps in achieving uniform density and shaping complex components with intricate geometries. CIP offers several advantages over traditional uniaxial die pressing, such as the ability to form more complex shapes and reducing distortions and cracking due to uniform particle packing. In this blog post, we will delve into the application, advantages, and limitations of Cold Isostatic Pressing.
Overview of Cold Isostatic Pressing
Explanation of cold isostatic pressing
Cold isostatic pressing (CIP) is a materials processing technique that involves applying equal pressure in all directions to a powder material. This process is used to compress the powder into a solid mass, creating a raw part with sufficient strength for handling and further processing.
Differentiation between wet bag and dry bag isostatic pressing
One variation of cold isostatic pressing is the wet bag technology. In this process, the powder is filled in a mold and sealed tightly outside the pressure vessel. The mold is then submerged in a high-pressure fluid within the vessel, and isostatic pressure is applied to compress the powder into a shape. Wet bag technology is ideal for multi-shape and small to large quantity production.
On the other hand, dry bag isostatic pressing involves creating an integrated mold within the pressure vessel itself. The powder is added to the mold, the mold is sealed, and pressure is applied to compress the powder. This process eliminates the need for submerging the mold in a separate fluid, making automation easier.
Role of powder quality and tooling design in the process
The quality of the powder used in cold isostatic pressing plays a crucial role in the final product. The powder should have proper particle size distribution, flowability, and density to ensure efficient and uniform compression. Additionally, the tooling design, including the mold or bag used, should be carefully designed to accommodate the specific requirements of the powder material and desired shape.
Proper tooling design and powder quality are essential for achieving the desired density and strength in the final product. This is especially important in industries such as aerospace, automotive, and medical, where high-quality and reliable components are crucial.
In summary, cold isostatic pressing is a versatile materials processing technique that allows for the compression of powder materials into solid parts. The choice between wet bag and dry bag technology depends on the specific production requirements. Additionally, the quality of the powder and tooling design play a significant role in ensuring the desired results in the final product.
Types of Cold Isostatic Pressing
Detailed description of wet bag technique
In the wet bag technique of cold isostatic pressing, the powder material is filled in a mold and tightly sealed outside the pressure vessel. The filled mold is then submerged in a pressure fluid within the pressure vessel. Isostatic pressure is applied to the external surface of the mold, compressing the powder into a solid mass.
This method is not as common as the other type of cold isostatic pressing, but there are over 3000 wet bag presses used worldwide. Wet bags come in various sizes, ranging from 50mm to 2000mm in diameter.
Processing material using wet bag technology can take anywhere from 5 to 30 minutes, making it a relatively slow process. However, the use of high-volume pumps and improved loading mechanisms can help speed up the process.
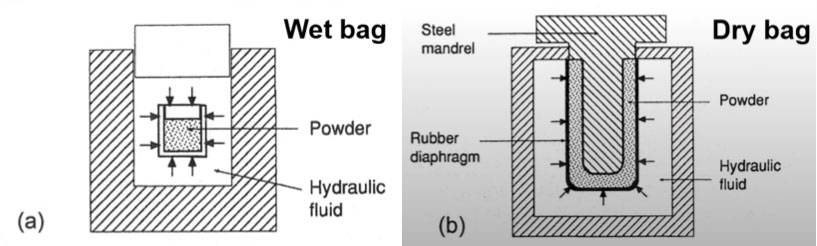
Wet bag isostatic pressing
Pre-shape the sample, load in soft bag,(vacuum) and immerse in hydraulic fluid, apply high pressure " Used for complex shape and large size sample”
Explanation of dry bag pressing technique
The dry bag pressing technique, on the other hand, involves creating a mold that is integrated into the pressure vessel. In this process, the powder is added to the mold, which is then sealed. Pressure is applied, and the resulting part is ejected.
Compared to the wet bag technique, the dry bag process lends itself to automation and is suitable for pressing long runs of compacts at high production rates. The integration of the mold into the pressure vessel eliminates the need for the immersion step, making it a more efficient method.
Comparison of applications for both techniques
The choice between wet bag and dry bag techniques depends on the specific requirements of the application. Wet bag technology is ideal for multi-shape and small to large quantity production, as well as the pressing of large products. It allows for the creation of intricate shapes and achieves high green density.
On the other hand, dry bag pressing is more suitable for automation and high production rates. It offers easier integration into the manufacturing process and eliminates the immersion step, resulting in faster production times.
In summary, both wet bag and dry bag techniques have their advantages and are used in different applications. The decision between the two depends on factors such as the desired shape, production quantity, and level of automation required.
Advantages of Cold Isostatic Pressing over Uniaxial Die Pressing
Capability to form more complex shapes
Cold Isostatic Pressing (CIP) offers the advantage of being able to form more complex shapes compared to Uniaxial Die Pressing. With CIP, the pressure is applied uniformly over the entire surface of the mold, allowing for the compaction of intricate and detailed shapes. This is particularly beneficial when manufacturing components with intricate geometries or designs that may be difficult to achieve with Uniaxial Die Pressing.

Reduction of distortions and cracking due to uniform particle packing
One of the major advantages of Cold Isostatic Pressing over Uniaxial Die Pressing is the reduction of distortions and cracking in the final product. In CIP, the pressure is applied uniformly, resulting in more uniform particle packing and reduced pressure gradients. This leads to a more homogeneous density distribution and reduces the likelihood of distortions and cracking in the finished component. This advantage is especially critical when dealing with complex-shaped components.
According to technical considerations, CIP provides increased and more uniform density at a given compaction pressure, making it particularly suitable for brittle or fine powders. Additionally, the absence of die-wall friction in CIP eliminates problems associated with lubricant removal and allows for higher pressed densities.
Moreover, CIP offers the advantage of more even shrinkage during sintering due to the uniform green density. This is essential for maintaining good shape control and achieving uniform properties in the final product. Furthermore, CIP does not require a wax binder like Uniaxial Die Pressing, eliminating the need for dewaxing operations.
In summary, the advantages of Cold Isostatic Pressing over Uniaxial Die Pressing include the capability to form more complex shapes and the reduction of distortions and cracking due to uniform particle packing. These advantages make CIP a preferred method for manufacturing components with intricate geometries and achieving high-quality, homogeneous products.
Cold Isostatic Pressing in Complex-Shaped Component Production
Comparison of CIP and injection molding for large-volume production
When complex-shaped components are required, beyond the shape capabilities of uniaxial die pressing, and a large-volume production throughput is needed, CIP and injection molding are the two main options used. CIP was the first high-tech method reported in the literature for manufacturing alumina ceramics, by Daubenmeyer in 1934. Indeed, spark plug insulators are probably the largest production-volume CIPed ceramic component globally. A significant proportion of the 3 billion spark plug insulators manufactured annually are CIPed. As for uniaxial die pressing, CIP feedstock is commonly simple milled Bayer alumina, milled and spray-dried Bayer alumina, or in rare cases, high-tech spray-dried SolGel nanopowders. However, in general, CIP is not as common industrially as injection molding. CIP is generally only used when very complex shapes are required and injection molding is not practical for whatever reason.
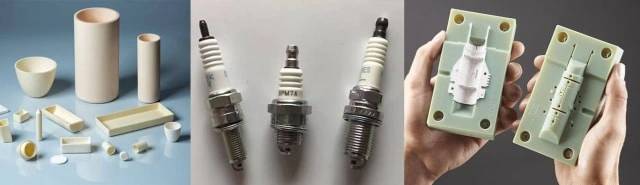
Historical overview of CIP usage in manufacturing alumina ceramics
Cold-isostatic pressing (CIP) is a powder-based, near-net-shape technology for the production of metal and ceramic components. CIP has been commonly used for processing ceramics, but not as widely used for metals. Recent developments in process capability and powder metallurgy, however, have allowed CIP to be increasingly used in the manufacture of high-performance metal parts. Advantages such as solid-state processing, uniform microstructure, shape complexity, low tooling cost and process scalability have made CIP a viable processing route for metals. In addition, the potential to produce near-net-shape parts with minimal material waste has made the process more widely acceptable in niche applications, such as aerospace and automotive.
Usage of CIP in spark plug insulator production
For decades, Cold Isostatic Pressing (CIP) has been used successfully by manufacturers around the world. CIP is used to consolidate metal- and ceramic powders to make a “green” part that can be further treated, i.e. rolling, machining or sintering.
With typical pressures from 1,035 to 4,138 bar (15,000 to 60,000 psi) and ambient temperature up to 93°C (200°F), CIP can achieve 95% of theoretical density for ceramics.
A proven process for high-performance parts Common applications for Cold Isostatic Pressing include consolidation of ceramic powders, compressing of graphite, refractories and electrical insulators, and other fine ceramics for dental and medical applications.
The technology is expanding into new applications such as pressing of sputtering targets, coatings of valve parts in an engine to minimize wear of the cylinder heads, telecommunications, electronics, aerospace and automotive.
Cold Isostatic Presses
Cold isostatic presses (CIP) are used to produce unsintered or green dye-compacted metal powder components in a preliminary densification step prior to rolling, machining or sintering. Our CIP systems are used by companies around the world to effectively produce flawless components for the aerospace, military, industrial and medical industries. Technology leaders worldwide know that our cold isostatic presses are designed in such a way that parts can easily be removed with sufficient green strength for further handling and sintering.
Cold Isostatic Pressing
Cold isostatic pressing has the advantage for producing parts where the high initial cost of pressing dies cannot be justified or when very large or complex compacts are needed. A variety of powders can be pressed isostatically on a commercial scale, including metals, ceramics, plastics, and composites. Pressures required for compacting range from less than 5,000 psi to more than 100,000 psi (34.5 to 690 MPa). Powders are compacted in elastomeric molds in either a wet or dry bag process.
Material capabilities are important to consider when selecting cold isostatic pressing services. Aluminum and magnesium alloys, carbides and cutting tools, carbon and graphite, ceramics, and composites are just some of the materials and components that are produced with CIP. Some cold isostatic pressing services specialize in coatings and thermal spray deposits, copper alloys, or diamond and diamond-like materials. Others work with electronic or electrical materials, explosives or pyrotechnics, or specialty and proprietary materials.
Process of Cold Isostatic Pressing
Explanation of the CIP process
Cold Isostatic Pressing (CIP) is a method of processing materials that involves compacting powders by enclosing them in an elastomer mold. The mold is made from materials like urethane, rubber, or polyvinyl chloride, which have low resistance to deformation. Liquid pressure is then uniformly applied to the mold to compress it. This process is based on Pascal's law, which states that pressure applied in an enclosed fluid is transmitted in all directions without any change in magnitude.
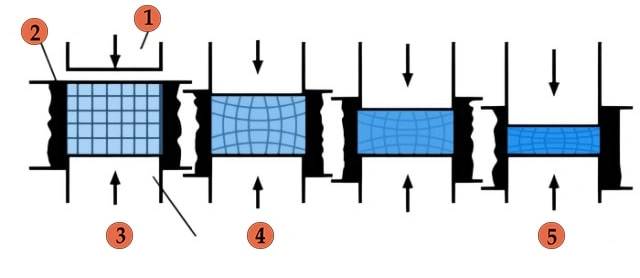
CIP can be used for various materials such as plastics, graphite, powdered metallurgy, ceramics, and sputtering targets. It is commonly used to obtain a "raw" part with sufficient strength for handling and processing, which can then be further sintered to achieve final strength.
Automation of the CIP process
The CIP process can be automated using specialized equipment. The material to be processed is sealed in an elastomer mold and placed in a pressure chamber. A liquid medium, such as water or oil, is pumped into the chamber, and the mold is uniformly subjected to high pressure from all sides. This automation ensures consistent and precise application of pressure, resulting in high-quality finished products.
Automating the CIP process offers several advantages. It improves efficiency by reducing manual labor and increasing production rates. It also ensures consistent pressure application, which improves the overall quality and reliability of the finished products. Additionally, automation allows for better control and monitoring of the process parameters, leading to improved process optimization and cost savings.
Pressurization and depressurization cycles in CIP
The CIP process involves pressurization and depressurization cycles to achieve the desired compaction of the powders. During the pressurization cycle, the liquid medium is pumped into the pressure chamber, applying uniform pressure to the elastomer mold. This pressure compacts the powders and forms a highly compact solid.
After the desired compaction is achieved, the depressurization cycle begins. The pressure in the chamber is gradually released, allowing the mold to relax and the compacted material to be removed. This cycle ensures that the compacted material can be easily extracted from the mold without deformation or damage.
The pressurization and depressurization cycles are carefully controlled to achieve the desired density and strength of the compacted material. The parameters, such as the pressure magnitude, duration, and rate of change, can be adjusted based on the specific requirements of the material being processed.
Advantages of Cold Isostatic Pressing for Alumina Ceramics
Comparison of CIP to uniaxial die pressing and other ceramic forming methods
Cold Isostatic Pressing (CIP) is a powder-based, near-net-shape technology for the production of metal and ceramic components. CIP has been commonly used for processing ceramics, but not as widely used for metals. Recent developments in process capability and powder metallurgy, however, have allowed CIP to be increasingly used in the manufacture of high-performance metal parts. Advantages such as solid-state processing, uniform microstructure, shape complexity, low tooling cost, and process scalability have made CIP a viable processing route for metals.
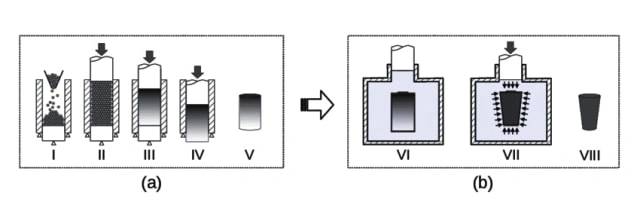
Some of the key advantages of CIP for alumina ceramics in comparison to uniaxial die pressing are as follows:
-
More complex shapes are possible: CIP allows for the production of more complex shapes compared to uniaxial die pressing. This is because CIP uses flexible molds that can accommodate intricate designs and shapes.
-
Greatly reduced pressing pressure gradients: CIP significantly reduces pressing pressure gradients, which helps to minimize distortion and cracking during the forming process. This ensures that the final ceramic components have improved dimensional accuracy and structural integrity.
Benefits of CIP for complex parts with small production runs
CIP offers several benefits for the production of complex parts with small production runs. These advantages include:
-
Low mold cost: CIP requires low mold cost, making it ideal for producing complex parts with small production runs. Unlike other ceramic forming methods, CIP does not require expensive molds, which helps to reduce manufacturing costs.
-
No mold cost for post-CIP: In addition to low mold cost, CIP also eliminates the need for molds in post-CIP processes. This further reduces production costs and allows for greater flexibility in manufacturing complex parts.
-
No size limitation: CIP does not have size limitations, except for the limits of the press chamber. This makes it suitable for producing very large components, especially those with complex shapes. In fact, components weighing over 1 ton have been successfully produced using CIP.
-
Short processing cycle times: CIP has short processing cycle times as it does not require drying or binder burnout. This means that the formed ceramic components can be sintered faster compared to other methods, leading to increased production efficiency.
While CIP offers numerous advantages for alumina ceramics, it is important to note some of its limitations. These include limited dimensional control, shape complexity inferior to powder injection molding (PIM), and the requirement for powders with excellent flowability.
Disadvantages of Cold Isostatic Pressing for Ceramics
Challenges with dimensional control and shape complexity
Cold isostatic pressing (CIP) is a powder-compacting process that is used to obtain parts ready for sintering. However, there are some challenges associated with dimensional control and shape complexity when using CIP for ceramics.
The lower accuracy of pressed surfaces adjacent to the flexible bag compared to mechanical pressing or extrusion often necessitates subsequent machining. This means that additional steps may be required to achieve the desired dimensions and shape of the ceramic parts.
Requirements for powders used in CIP
One of the disadvantages of cold isostatic pressing is that relatively expensive spray-dried powder is normally required for fully automatic dry bag presses. This can increase the overall cost of the process, as specialized powders need to be used.
Additionally, the production rates for CIP are lower compared to extrusion or die compaction. This means that the process may not be as efficient in terms of volume production.
Applications of Cold Isostatic Pressing
Common use of CIP in mass production of advanced ceramics
Cold Isostatic Pressing (CIP) is a powder-based, near-net-shape technology that is commonly used for processing ceramics. It has the advantage of being able to produce parts where the high initial cost of pressing dies cannot be justified or when very large or complex compacts are needed.
A variety of powders can be pressed isostatically on a commercial scale, including metals, ceramics, plastics, and composites. The pressures required for compacting range from less than 5,000 psi to more than 100,000 psi. Powders are compacted in elastomeric molds in either a wet or dry bag process.
CIP has been widely used for the consolidation of ceramic powders, graphite, refractory materials, electrical insulators, and the compression of advanced ceramics. Materials such as silicon nitride, silicon carbide, boron nitride, boron carbide, titanium boride, and spinel can be processed using CIP.
The technology is expanding into new applications such as the compression of sputtering targets, the coating of valve components used to reduce cylinder wear in engines, and various applications in telecommunications, electronics, aerospace, and automotive industries.
Examples of components produced by CIP
CIP is commonly used for the consolidation of ceramic powders, compressing graphite, refractories, and electrical insulators, as well as other fine ceramics for dental and medical applications. It is also used for pressing sputtering targets, coatings of valve parts in engines to minimize wear of the cylinder heads, and in various applications in telecommunications, electronics, aerospace, and automotive industries.
CIP equipment is used to compress production costs and is essential for making finished goods out of raw materials. The process involves confining powders in an elastomer mold, placing the mold in a pressure chamber, pumping in a liquid medium, and uniformly subjecting the mold to high pressure from all sides. CIP can be utilized with powdered metallurgy, cemented carbides, refractory materials, graphite, ceramics, plastics, and other materials.

Material capabilities are important to consider when selecting cold isostatic pressing services. Aluminum and magnesium alloys, carbides and cutting tools, carbon and graphite, ceramics, composites, and other materials can be produced using CIP. Some cold isostatic pressing services specialize in coatings and thermal spray deposits, copper alloys, diamond and diamond-like materials, electronic or electrical materials, explosives or pyrotechnics, or specialty and proprietary materials.
Cold isostatic pressing is performed at room temperature and uses a mold made from an elastomer material such as urethane, rubber, or polyvinyl chloride. The fluid used in cold isostatic pressing is usually oil or water, and the fluid pressure during the operation typically ranges from 60,000 lbs/in2 to 150,000 lbs/in2. A disadvantage of this manufacturing process is the low geometric accuracy due to the flexible mold.
Alternative Compression Technologies
Overview of other compression technologies
In the realm of materials processing, there are several powerful compression techniques available. Two of these techniques, Cold Isostatic Pressing (CIP) and Hot Isostatic Pressing (HIP), are widely used in various industries. While both methods aim to enhance material properties, they differ in their operating conditions and offer unique advantages.
Introduction of shock-wave compaction as an alternative
While CIP and HIP are effective compression techniques, alternative technologies have been developed to address specific challenges. One such alternative is shock-wave compaction, also known as shock compression.
Shock-wave compaction involves the generation of a short, high-pressure shock wave that can severely deform particles or even cause local melting. This process can result in the material becoming fully dense and compact without significant grain growth. Shock waves are characterized by very high pressures, medium temperatures, very short reaction times, and very high strain rates.
Various methods, such as air guns and explosive shock waves, that were previously used for compression of micron-sized powders, are now being used to compress nanopowders. These alternative compression technologies with very short heating times have shown success in achieving fully dense and compact materials without nanograin coarsening.
One example of shock-wave compaction is the use of a plane shock-wave compaction device equipped with an air gun. This device generates a short, high-pressure shock wave that can deform particles and achieve full density and compaction. These alternative compression technologies offer an efficient way to process materials with minimal grain growth and improved material properties.
In the rubber industry, advanced compression presses are used for efficient rubber vulcanization. By applying controlled pressure force on rubber materials, these machines test the physical characteristics of rubber products, such as strength, resilience, and durability, ensuring they meet ASTM standards and are of high quality.
Overall, alternative compression technologies like shock-wave compaction provide innovative solutions for achieving fully dense and compact materials with improved properties. These technologies offer unique advantages and can be utilized in various industries to enhance material processing capabilities.
Conclusion
In conclusion, cold isostatic pressing (CIP) is a highly versatile and efficient technique for manufacturing complex-shaped components, particularly in the production of advanced ceramics. Unlike traditional uniaxial die pressing, CIP allows for the formation of more intricate shapes and reduces the risk of distortions and cracking due to its uniform particle packing. While there are challenges with dimensional control and powder requirements, CIP offers significant advantages for small production runs and is widely used in the mass production of advanced ceramics. As an alternative to CIP, shock-wave compaction is also worth considering for certain compression applications.
CONTACT US FOR A FREE CONSULTATION
KINTEK LAB SOLUTION's products and services have been recognized by customers around the world. Our staff will be happy to assist with any inquiry you might have. Contact us for a free consultation and talk to a product specialist to find the most suitable solution for your application needs!