Basics of Cold Isostatic Pressing
Table of Contents
Definition and purpose of Cold Isostatic Pressing (CIP)
Cold Isostatic Pressing (CIP) is a method of processing materials by compacting powders through the application of uniform pressure from all directions. This process is based on Pascal's law, which states that pressure applied in an enclosed fluid is transmitted equally in all directions.
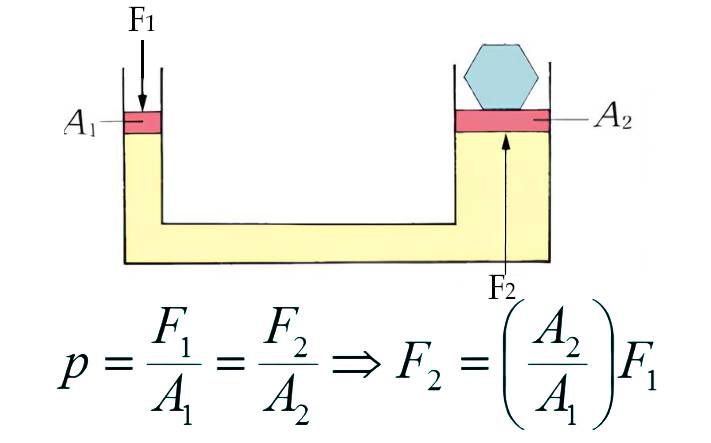
CIP involves enclosing the powder in an elastomer mold and applying liquid pressure to compress it. The result is a highly compact solid material. CIP can be used for a wide range of materials such as plastics, graphite, ceramics, powdered metallurgy, and sputtering targets.
Differentiation between wet bag and dry bag isostatic pressing
There are two types of cold isostatic pressing: wet bag and dry bag isostatic pressing.
In wet bag isostatic pressing, the powder is enclosed in a rubber sheath and immersed in a liquid that transmits pressure uniformly to the powder. This method is used for low-volume production, prototyping, and research and development.
In dry bag isostatic pressing, the elastomer mold is an integral part of the isostatic press. The pressure applied is mostly biaxial, and this method is suitable for high-volume production.
Role of powder quality and tooling design in CIP
Powder quality and tooling design play crucial roles in the success of cold isostatic pressing.
The quality of the powder used affects the density and strength of the final product. Powders with low or no wax content are commonly used in CIP. Additionally, dimensional tolerances for parts produced by CIP are relatively large, so size and shape control may not be as critical as in other pressing methods.
Tooling design is also important in CIP. Elastomer molds made from materials like urethane, rubber, or polyvinyl chloride are used. The choice of mold material and design impacts the accuracy and precision of the final product.
Concept and benefits of isostatic pressing
Isostatic pressing, including cold isostatic pressing, offers several advantages in materials processing.
One major benefit is the ability to achieve uniform compaction and increased shape capability compared to uniaxial pressing. Isostatic pressing applies pressure from multiple directions, resulting in high-quality parts with greater density.
Isostatic pressing is also suitable for forming complicated shapes that cannot be compressed using other methods. The use of elastomer molds allows for flexibility and versatility in shaping materials.
In summary, cold isostatic pressing is a valuable method for shaping and compacting powders. It offers unique advantages in terms of uniformity, shape capability, and versatility. By understanding the basics of CIP and its applications, businesses can leverage this process to produce high-quality components for various industries.
Types of Cold Isostatic Pressing
Wetbag technique of CIP
Cold isostatic pressing (CIP) is a common method used for compacting powdered materials into a solid homogeneous mass before machining or sintering. The wetbag technique is a subtype of CIP where the raw powder is filled into flexible molds that are immersed in water or other liquids. Isostatic pressure is then applied to compress the powder into the desired shape. This process allows for the production of complex components and can even be used to press tungsten ingots weighing up to 1 ton.
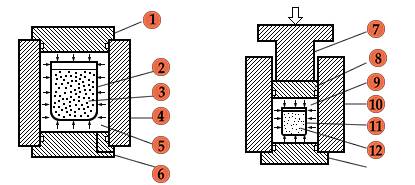
Drybag pressing and its application
Another subtype of CIP is drybag pressing, which is used for simple shapes. In this process, the powder-filled mold is sealed and the compression occurs between the mold and the pressure vessel. Drybag pressing is more suitable for high-volume production of relatively simple shapes and can be automated for increased efficiency.

Comparison of complex shapes production between CIP and uniaxial die pressing
When comparing cold isostatic pressing (CIP) to uniaxial die pressing, it is evident that CIP allows for the production of more complex shapes. Uniaxial pressing, on the other hand, is suitable for pressing simple shapes with fixed dimensions, such as cylinders or squares. CIP offers greater flexibility in shape and size, allowing for the production of longer aspect ratios and improved compaction of the powder. Additionally, CIP does not require a wax binder like uniaxial pressing, eliminating the need for dewaxing operations.
Advantages of CIP over uniaxial die pressing
There are several advantages of cold isostatic pressing (CIP) over uniaxial die pressing. Firstly, CIP allows for the production of more complex shapes compared to uniaxial die pressing, which is limited to simple shapes. Secondly, CIP offers more uniform product properties, greater homogeneity, and more precise control of the finished product dimensions. It also enables longer aspect ratios, improved densification of the powder, and the ability to process materials with different characteristics and shapes. Additionally, CIP reduces cycle times and improves productivity.
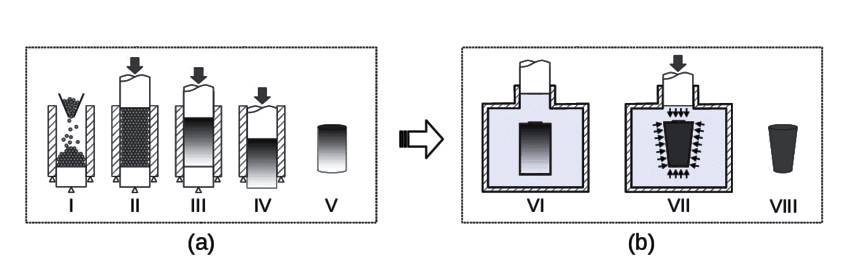
CIP vs Other Techniques
Comparison of CIP and injection molding
When complex-shaped components are required beyond the capabilities of uniaxial die pressing and a large-volume production throughput is needed, two main options are used: CIP (Cold Isostatic Pressing) and injection molding. CIP was the first high-tech method reported in the literature for manufacturing alumina ceramics. Compared to uniaxial die pressing, CIP allows for more complex shapes and greatly reduced pressing pressure gradients, resulting in less distortion and cracking. However, CIP is not as common industrially as injection molding and is generally only used when very complex shapes are required and injection molding is not practical.
Role of CIP in manufacturing alumina ceramics
CIP plays a crucial role in the manufacturing of alumina ceramics. It allows for the production of complex-shaped components that are beyond the capabilities of other techniques like uniaxial die pressing. CIP feedstock for alumina ceramics can be simple milled Bayer alumina, milled and spray-dried Bayer alumina, or high-tech spray-dried SolGel nanopowders. Some of the key advantages of CIP for alumina ceramics include the ability to produce more complex shapes, reduced pressing pressure gradients, low mold cost for complex parts with small production runs, no size limitation, and short processing cycle times.
Usage of CIP in the production of spark plug insulators
Spark plug insulators are one of the largest production-volume ceramic components globally that are manufactured using CIP. Approximately 3 billion spark plug insulators are CIPed annually. The use of CIP in the production of spark plug insulators showcases its ability to handle large production volumes and complex shapes. CIP is the mainstay of the spark plug industry and is a relatively low-cost process ideal for shape complexity and large production runs.
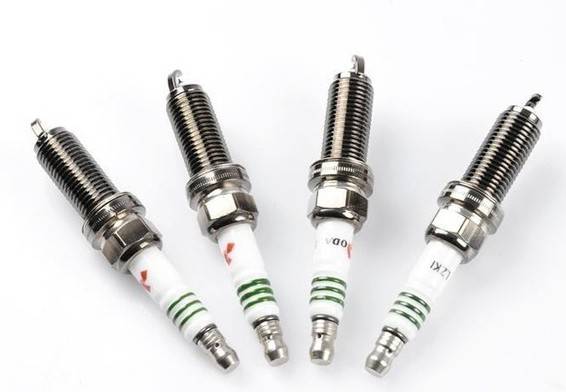
Types of CIP feedstock
In the production of alumina ceramics using CIP, various types of feedstock can be used. Commonly used feedstock includes simple milled Bayer alumina, milled and spray-dried Bayer alumina, and in rare cases, high-tech spray-dried SolGel nanopowders. The choice of feedstock depends on the specific requirements of the ceramic component being produced. CIP feedstock requires excellent flowability, which is typically achieved through spray drying or mold vibration during filling.
Advantages of CIP:
- More complex shapes are possible compared to uniaxial die pressing
- Greatly reduced pressing pressure gradients, resulting in less distortion and cracking
- Low mold cost, ideal for complex parts with small production runs
- No size limitation, suitable for very large components
- Short processing cycle times, no drying or binder burnout required
Disadvantages of CIP:
- Limited dimensional control compared to metal die compaction
- Shape complexity is superior to uniaxial die pressing but inferior to Powder Injection Molding (PIM)
- Powders for CIP require excellent flowability, often achieved through spray drying
- Limited vessel capability and capacity
- Comparatively manual process with lower production rates compared to metal die compaction
CIP is a solid-state process that offers several advantages for the production of high-performance metal components. It provides uniform microstructure, shape complexity, low tooling cost, process scalability, and the potential to produce near-net-shape parts with minimal material waste. However, it also has limitations such as being limited to processing certain types of powders, limited vessel capability and capacity, and requiring more post-processing compared to processes that use rigid tools. Despite these limitations, CIP remains a valuable technique for mass production of advanced ceramics and the production of complex-shaped components.
Process of Cold Isostatic Pressing
Process of uniform pressing in CIP
Cold Isostatic Pressing (CIP) is a method of processing materials by compacting powders enclosed in an elastomer mold. The mold is then uniformly subjected to liquid pressure, which compresses the powders into a highly compact solid. This process ensures that the pressure is applied uniformly in all directions, resulting in a homogenous final product. CIP can be used for a variety of materials, including plastics, graphite, ceramics, and powdered metallurgy.
Use of soft bag or mold for CIP
In CIP, an elastomer mold or a soft bag is used to enclose the powders. This mold has low resistance to deformation, allowing it to compress easily under the applied pressure. The use of a soft bag or mold ensures that the pressure is evenly distributed throughout the powders, resulting in a uniform and compact final product.
Concept of post-CIP
After the CIP process, the molded body undergoes a post-CIP treatment. This treatment involves further processing or sintering to achieve the desired final strength and properties. Post-CIP treatments may vary depending on the specific material being processed.
Role of oil chamber in CIP
In CIP, an oil chamber is used as the pressure medium. The oil chamber encloses the elastomer mold and allows for the application of liquid pressure. The oil chamber plays a crucial role in transmitting the applied pressure uniformly to the mold, ensuring that the powders are compacted uniformly.
Pressurization and depressurization cycles in CIP
The CIP process involves pressurization and depressurization cycles. During the pressurization cycle, the liquid pressure is applied to the elastomer mold, compressing the powders. The pressure is held for a specific period, allowing the powders to consolidate. Afterward, the depressurization cycle begins, releasing the pressure and allowing the molded body to be retrieved.
Automation and large-scale implementation of CIP
CIP can be automated and implemented on a large scale for industrial production. Automation allows for precise control of the pressurization and depressurization cycles, ensuring consistent and high-quality results. The large-scale implementation of CIP enables the efficient processing of a large volume of materials, making it suitable for various industries.
Overall, Cold Isostatic Pressing is a valuable method for processing materials, providing uniform compaction and high-quality final products. Its use of an elastomer mold, oil chamber, and pressurization cycles ensures consistent results and enables large-scale production. Whether it's for plastics, ceramics, or powdered metallurgy, CIP offers a reliable and efficient solution for material processing.
Advantages and Disadvantages of CIP for Alumina Ceramics
Benefits of CIP compared to uniaxial die pressing and other ceramic forming methods
When complex-shaped components are required beyond the capabilities of uniaxial die pressing, and a large-volume production throughput is needed, CIP (Cold Isostatic Pressing) and injection molding are the two main options used. CIP was the first high-tech method reported in the literature for manufacturing alumina ceramics. It is commonly used for mass production of advanced ceramics with complex shapes or extremely large ceramic components.
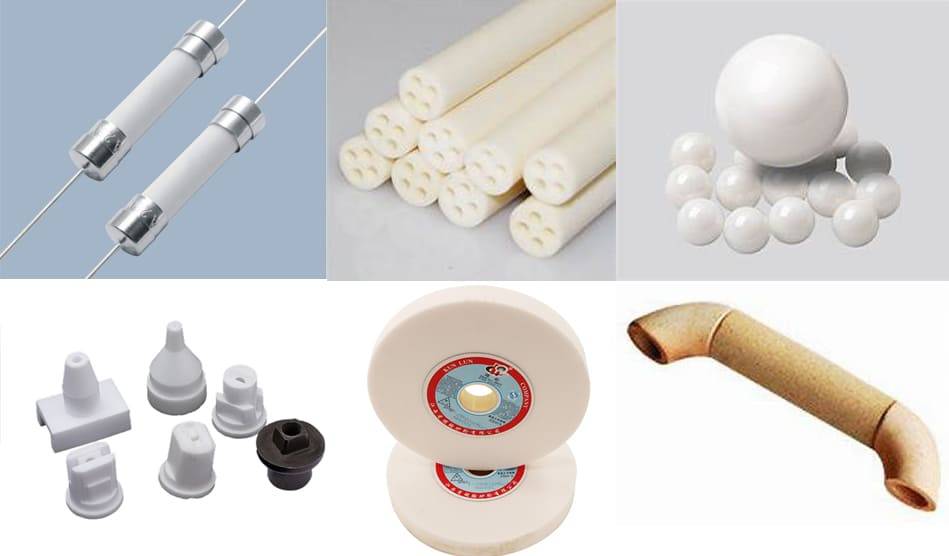
Some of the key advantages of CIP for alumina ceramics are as follows:
-
More complex shapes are possible: CIP allows for the production of complex-shaped components that are beyond the shape capabilities of uniaxial die pressing.
-
Greatly reduced pressing pressure gradients: CIP helps in reducing distortion and cracking by applying uniform pressing from all directions in three dimensions.
-
Low mold cost: CIP is ideal for complex parts with small production runs, as it requires low mold cost.
-
No size limitation: CIP has no size limitation, other than the limits of the press chamber. It is therefore ideal for very large components, especially complex-shaped ones. Components heavier than 1 ton have been CIPed.
-
Short processing cycle times: CIP does not require drying or binder burnout, resulting in shorter processing cycle times.
Limitations and challenges of CIP for ceramics
Despite its advantages, CIP also has some limitations and challenges for ceramics:
-
Limited dimensional control: Achieving high precision is problematic in CIP due to the need for a very thin and uniformly thick elastomer mold or sheath.
-
Shape complexity inferior to PIM: While CIP offers superior shape complexity compared to uniaxial die pressing, it is still inferior to Powder Injection Molding (PIM) in terms of shape complexity.
-
Powder flowability requirements: Powders used in CIP require excellent flowability, which generally means spray drying or mold vibration during filling.
-
Comparatively manual: CIP is a comparatively manual process, requiring careful handling and control.
-
Limited to processing certain types of powders: CIP is limited to processing powders with excellent flowability, which may restrict the range of materials that can be used.
-
Limited vessel capability and capacity: CIP is limited by the capability and capacity of the press chamber, which may restrict the size of the components that can be produced.
Despite these limitations, CIP remains a commonly used method for mass production of advanced ceramics with complex shapes or large production runs. It is particularly prevalent in the alumina industry, where it is the mainstay of the spark plug industry and a relatively low-cost process ideal for shape complexity and large production runs. In addition to spark plug insulators, other components commonly CIPed include specialty wear components (such as those used in pumps and the textile industry) and electrical insulators.
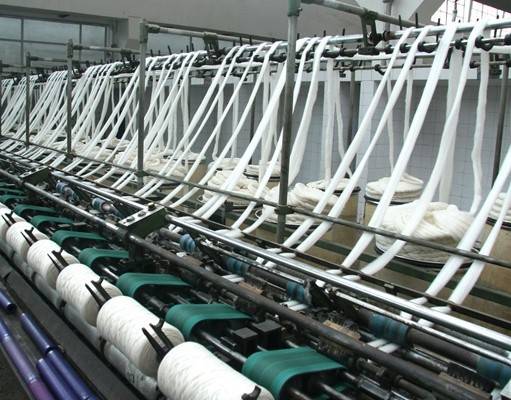
Overall, CIP offers unique advantages for the production of alumina ceramics, enabling the manufacturing of complex-shaped components with reduced pressure gradients and shorter processing cycle times. However, it is important to consider its limitations and challenges, such as limited dimensional control and powder flowability requirements, when deciding on the appropriate ceramic forming method for a specific application.
Applications of Cold Isostatic Pressing
Common usage of CIP in advanced ceramics production
Cold Isostatic Pressing (CIP) is a powder-based, near-net-shape technology used for the production of metal and ceramic components. While it has been commonly used for processing ceramics, recent developments in process capability and powder metallurgy have allowed CIP to be increasingly used in the manufacture of high-performance metal parts as well.
Advantages such as solid-state processing, uniform microstructure, shape complexity, low tooling cost, and process scalability have made CIP a viable processing route for metals. In addition, the potential to produce near-net-shape parts with minimal material waste has made the process more widely acceptable in niche applications, such as aerospace and automotive.
Common applications for cold isostatic pressing include the consolidation of ceramic powders, graphite, refractory materials, electrical insulators, and the compression of advanced ceramics. Materials such as silicon nitride, silicon carbide, boron nitride, boron carbide, titanium boride, and spinel are commonly used. The technology is also expanding into new applications, such as the compression of sputtering targets, coating of valve components used to reduce cylinder wear in engines, and applications in telecommunications, electronics, aerospace, and automotive industries.
Role of CIP in the spark plug industry and alumina industry
CIP plays a significant role in the spark plug industry and the alumina industry. In the spark plug industry, CIP is commonly used for mass production of advanced ceramics with complex shapes or extremely large ceramic components. It is not only used for spark plug insulators but also for specialty wear components in pumps and the textile industry, as well as electrical insulators.
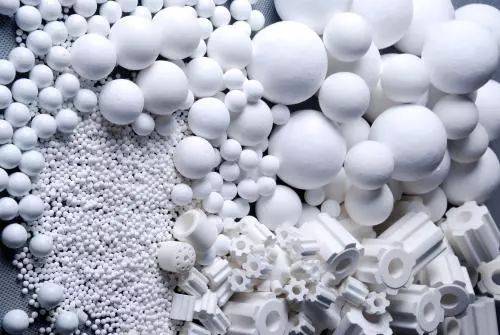
In the alumina industry, CIP is considered the mainstay of the spark plug industry. It is a relatively low-cost process that is ideal for shape complexity and large production runs. This makes it an essential technique for manufacturing spark plugs efficiently.
Overall, Cold Isostatic Pressing is a proven process for the production of high-performance parts in various industries. Its ability to achieve high densities for ceramics and its versatility in processing both ceramics and metals make it a valuable technique for manufacturers.
Comparison with Other Compression Technologies
Cold Isostatic Pressing vs. Hot Isostatic Pressing: A Comparative Overview
In the realm of materials processing, two powerful techniques stand out: Cold Isostatic Pressing (CIP) and Hot Isostatic Pressing (HIP). While both methods share the goal of enhancing material properties, they do so under different conditions, each offering unique advantages. Here's a comparative overview of Cold Isostatic Pressing vs. Hot Isostatic Pressing:
Cold Isostatic Pressing (CIP): Cold Isostatic Pressing, often referred to as cold isostatic compaction, involves subjecting a material to uniform pressure from all sides. This is achieved by immersing the material in a high-pressure fluid medium and applying hydraulic pressure. CIP is particularly effective for shaping and consolidating powdered materials, creating intricate shapes and achieving high green density.
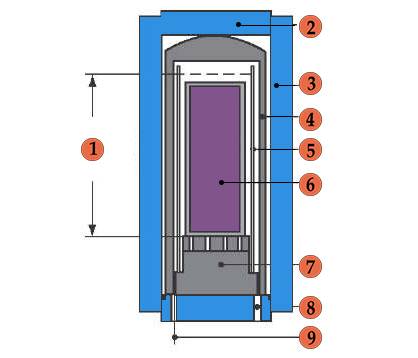
Hot Isostatic Pressing (HIP): Hot isostatic pressing (HIP) is a process technology that uses high temperature and high pressure to subject metal or ceramic products to equal pressure in all directions so that the parts can be sintered and densified. In 2021, the North American Heat Treatment Association, a representative of the global heat treatment industry, ranked hot isostatic pressing, hydrogen combustion technology, and additive manufacturing technology as the three most promising technologies and processes.
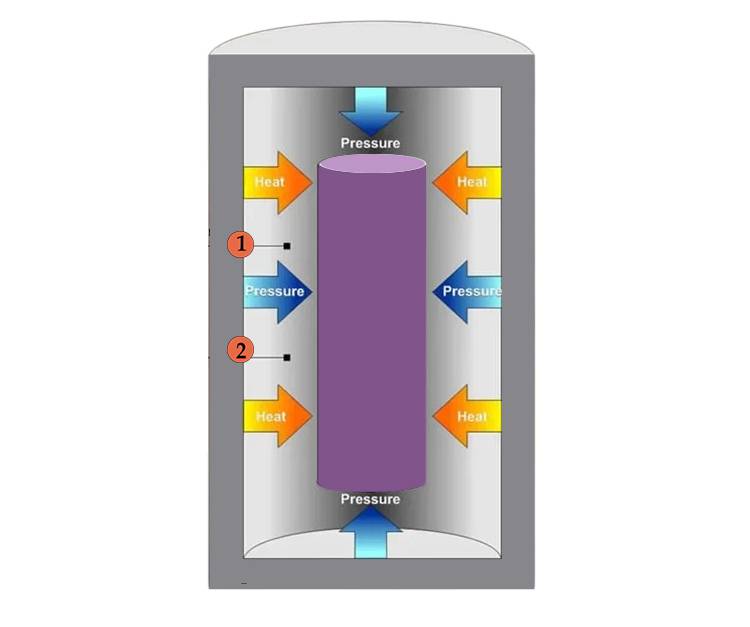
Hot isostatic pressing equipment consists of a high-pressure vessel, heating furnace, compressor, vacuum pump, storage tank, cooling system and computer control system, where the high-pressure vessel is the key device of the whole equipment.
From this point of view, the search for alternative methods that will meet the advancing technology and meet technological requirements not only for metal and ceramic substrates but also polymer-based ones encouraged researchers to work on new techniques and methods. “Ceramic powder aerosol deposition method,” which is pointed, is not only requiring additional high-temperature heat treatment or sintering steps but also homogeneous and continuous applicability to large areas. It has become a trend that draws the attention of researchers on semiconductor material technologies annually. As a result of all these advantages, the aerosol deposition method has been deemed worthy of examination both in terms of its technical details and applicability, and because it is a virgin technology that is still open to development in the field, it may meet the need in new-generation semiconductor technologies.
There is a distinct advantage in using isostatic pressing except for aluminium and iron compacted to high densities. At high densities both die and isostatic compaction produces similar green densities with iron and aluminium powders. However, for materials such as aluminium that have constant shear stress, the radial pressure becomes approximately equal to the axial pressure, i.e. approaches an isostatic pressure distribution. However, for materials like copper where yield stress is a function of the normal stress on the shear plane, the radial pressure remains less than the axial pressure. Although the pressure distribution within a cold-pressed compact may become isostatic, presumably, the pressure vs. density relationship should be identical with that of isostatic compacting only if the density distribution is equally uniform.
In summary, Cold Isostatic Pressing and Hot Isostatic Pressing represent distinct approaches to materials processing, each with its own advantages. The decision between the two depends on the specific goals of your project and the characteristics of the materials involved.
CONTACT US FOR A FREE CONSULTATION
KINTEK LAB SOLUTION's products and services have been recognized by customers around the world. Our staff will be happy to assist with any inquiry you might have. Contact us for a free consultation and talk to a product specialist to find the most suitable solution for your application needs!