Introduction
Table of Contents
Cold isostatic pressing (CIP) is a technique used in the manufacturing industry to achieve high-density materials with uniform properties. It involves applying equal pressure from all directions to a powder compact, resulting in improved compaction compared to traditional cold pressing methods. CIP offers several advantages, including the elimination of die-wall friction, the capability to compact brittle or fine powders, and the ability to produce complex shapes without any limitations on the part's cross section-to-height ratio. In this article, we will explore the technical aspects of CIP and its benefits over other compaction techniques.
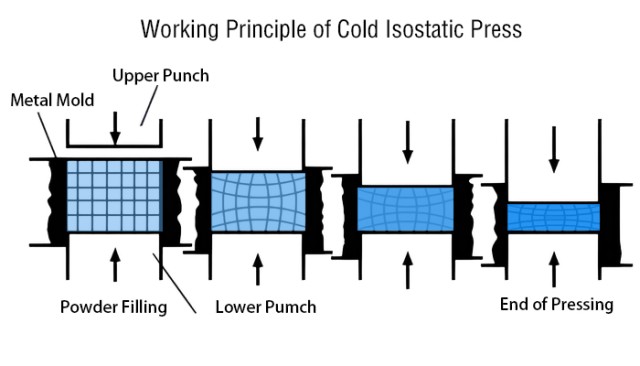
Advantages of Isostatic Compaction over Cold Pressing
Isostatic compaction, also known as cold isostatic pressing, offers several advantages over cold pressing. Let's explore the key benefits of this process:
1. Uniform pressure application
In isostatic compaction, pressure is applied uniformly over the entire surface of the mold. This results in more uniform product properties, greater homogeneity, and more precise control of the finished product dimensions. Compared to cold pressing, where pressure is exerted in a unidirectional manner, isostatic compaction ensures consistent pressure distribution, leading to better quality products.
2. Elimination of die-wall friction
Die-wall friction is a major factor that affects the density distribution of cold-pressed parts. In isostatic compaction, die-wall friction is eliminated. This absence of friction allows for the attainment of much more uniform densities. The elimination of die-wall lubricants also permits higher pressed densities and eliminates problems associated with lubricant removal prior to or during final sintering.
3. Higher and more uniform densities
Due to the uniform pressure application and absence of die-wall friction, isostatic compaction achieves higher and more uniform densities compared to cold pressing. The ability to achieve higher densities is particularly advantageous when working with brittle or fine powders. Isostatic compaction provides increased and more uniform density at a given compaction pressure, resulting in improved product quality.
4. Capability of compacting brittle or fine powders
Isostatic compaction is well-suited for compacting brittle or fine powders. The uniform compaction pressure and absence of die-wall friction minimize the risk of compact defects. This allows for the successful compaction of materials that are prone to cracking or breakage during the cold pressing process.
5. Ability to compact complex shapes
Isostatic compaction offers greater flexibility in terms of shape and size compared to cold pressing. The process can be used to compact more complex shapes that are not achievable with uniaxial pressing. This advantage opens up possibilities for manufacturing components with intricate designs and features.
6. No limit on part's cross section-to-height ratio due to uniform compaction pressure
In uniaxial pressing, the cross section-to-height ratio of the part can limit the compaction process. However, in isostatic compaction, the uniform pressure application allows for a higher cross section-to-height ratio. This means that parts with larger dimensions relative to their height can be successfully compacted, offering more design freedom.
In summary, isostatic compaction provides several advantages over cold pressing. It offers uniform pressure application, eliminates die-wall friction, achieves higher and more uniform densities, enables the compaction of brittle or fine powders, allows for the compacting of complex shapes, and removes limitations on the part's cross section-to-height ratio. These advantages make isostatic compaction a valuable technique in various industries, including pharmaceuticals, explosives, chemicals, food, nuclear fuel, and more.
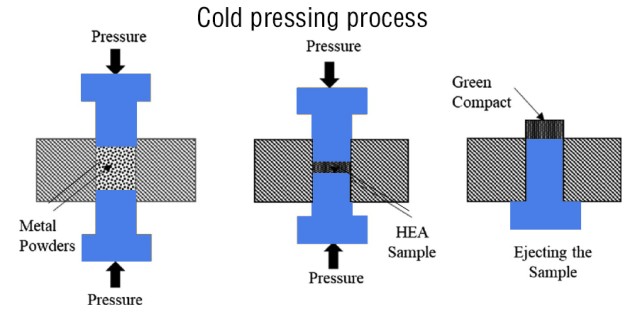
Comparison of Isostatic Pressing with Die Compaction for High-Density Materials
Similar green densities with iron and aluminum powders
Isostatic compaction provides increased and more uniform density at a given compaction pressure and relative freedom from compact defects when applied to brittle or fine powders. It eliminates problems associated with lubricant removal and allows for the evacuation of air from loose powder before compaction. Compared to cold pressing, isostatic compaction applies pressure uniformly over the entire surface of the mold, resulting in more uniform densities. However, for materials such as aluminum that have constant shear stress, the radial pressure becomes approximately equal to the axial pressure, approaching an isostatic pressure distribution. On the other hand, for materials like copper where yield stress is a function of the normal stress on the shear plane, the radial pressure remains less than the axial pressure.
Isostatic pressure distribution with materials having constant shear stress
For materials such as aluminum, where the shear stress is constant, the radial pressure in isostatic compaction becomes approximately equal to the axial pressure. This results in an isostatic pressure distribution, which allows for more uniform densities. Isostatic compaction is particularly advantageous for materials with constant shear stress, as it eliminates die-wall friction and allows for higher pressed densities without the need for die-wall lubricants.
Non-isostatic pressure distribution in materials where yield stress is a function of normal stress
In materials like copper, where the yield stress is a function of the normal stress on the shear plane, the radial pressure in isostatic compaction remains less than the axial pressure. While the pressure distribution within a cold-pressed compact may become isostatic, the pressure vs. density relationship will only be identical to isostatic compacting if the density distribution is equally uniform. Therefore, for materials with yield stress dependent on normal stress, the pressure distribution in isostatic compaction will not be fully isostatic.
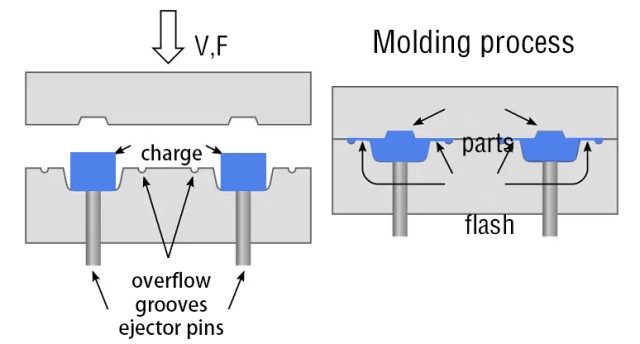
In conclusion, isostatic pressing offers advantages over die compaction for high-density materials, especially for brittle or fine powders. It provides increased and more uniform density, eliminates die-wall friction, allows for higher pressed densities, and enables the compaction of more complex shapes. However, the pressure distribution in isostatic compaction may vary depending on the material's shear stress characteristics and yield stress behavior.
Conclusion
In conclusion, cold isostatic pressing offers numerous advantages over traditional die compaction methods. The uniform pressure application ensures consistent and reliable compaction, resulting in higher and more uniform densities. Additionally, the elimination of die-wall friction allows for the compaction of brittle or fine powders, as well as the ability to compact complex shapes. Unlike die compaction, there is no limit on the part's cross section-to-height ratio due to the uniform compaction pressure. Overall, cold isostatic pressing is a highly effective technique for achieving high-density materials with superior quality and performance.
CONTACT US FOR A FREE CONSULTATION
KINTEK LAB SOLUTION's products and services have been recognized by customers around the world. Our staff will be happy to assist with any inquiry you might have. Contact us for a free consultation and talk to a product specialist to find the most suitable solution for your application needs!