Metals are generally not easy to compress due to their dense atomic structure and strong metallic bonds. Unlike gases or some soft materials, metals have a high bulk modulus, which measures their resistance to compression. This property arises from the close-packed arrangement of atoms in metals, which makes it difficult to reduce their volume under pressure. However, certain factors, such as the type of metal, its crystal structure, and external conditions like temperature and pressure, can influence compressibility. For example, alkali metals are relatively more compressible than transition metals due to their lower density and weaker bonding. Overall, while metals can be compressed under extreme conditions, they are not considered easy to compress compared to other materials.
Key Points Explained:
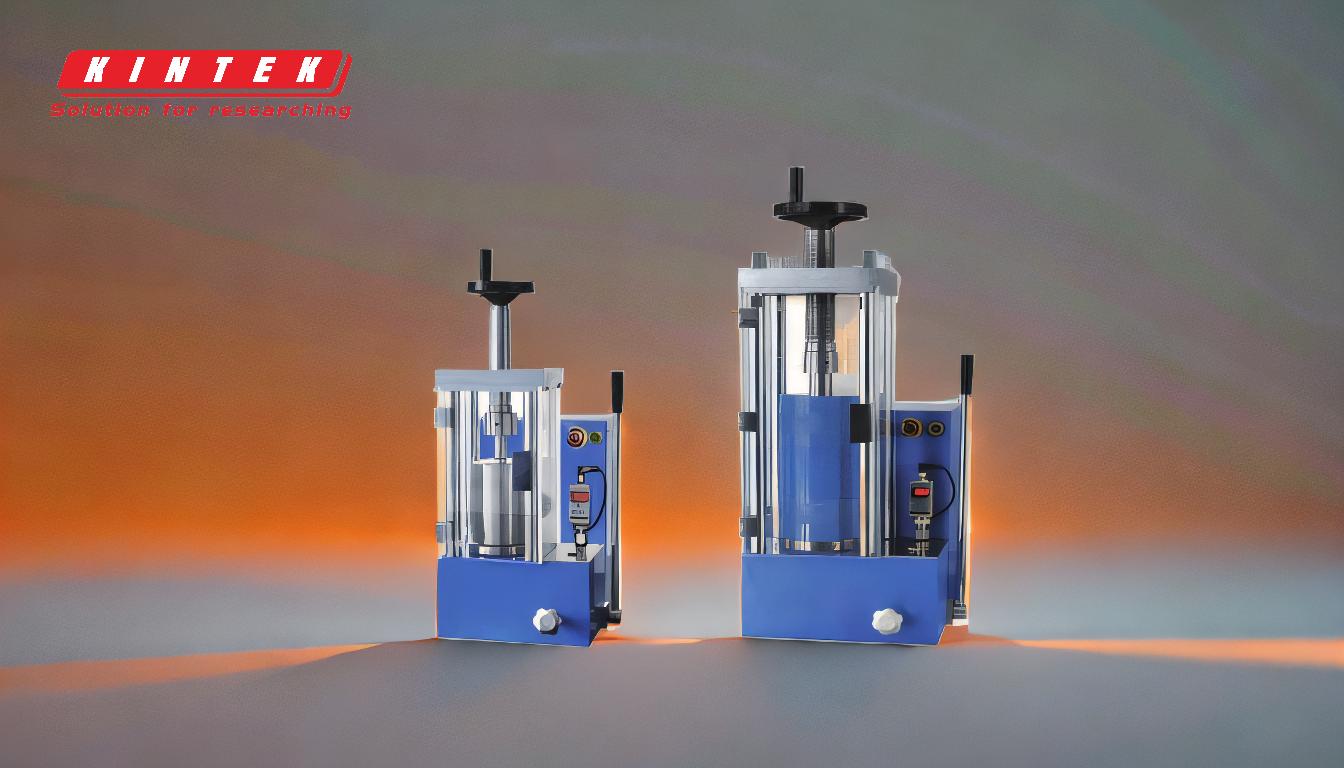
-
Atomic Structure and Metallic Bonds:
- Metals consist of closely packed atoms arranged in a crystalline structure. This arrangement creates strong metallic bonds, where electrons are shared among atoms in a "sea of electrons." These bonds contribute to the high density and rigidity of metals, making them resistant to compression.
-
Bulk Modulus:
- The bulk modulus is a measure of a material's resistance to uniform compression. Metals generally have a high bulk modulus, indicating that they require significant pressure to achieve even a small reduction in volume. For example, steel has a bulk modulus of around 160 GPa, making it highly resistant to compression.
-
Crystal Structure and Compressibility:
- The compressibility of a metal depends on its crystal structure. Metals with body-centered cubic (BCC) structures, such as iron at high temperatures, are generally more compressible than those with face-centered cubic (FCC) or hexagonal close-packed (HCP) structures. This is because BCC structures have more empty space between atoms, allowing for greater compression under pressure.
-
Types of Metals and Their Compressibility:
- Not all metals are equally compressible. Alkali metals like sodium and potassium are more compressible than transition metals like iron or copper due to their lower density and weaker metallic bonds. This makes them easier to compress under similar conditions.
-
External Conditions: Temperature and Pressure:
- Temperature and pressure play significant roles in the compressibility of metals. At high temperatures, metals may become more compressible as thermal energy weakens atomic bonds. Similarly, under extremely high pressures, such as those found in planetary cores, even dense metals like iron can undergo significant compression.
-
Practical Implications:
- The low compressibility of metals makes them ideal for applications requiring structural integrity and durability, such as construction, aerospace, and manufacturing. However, in specialized fields like high-pressure physics or materials science, understanding the compressibility of metals under extreme conditions is crucial for developing advanced materials and technologies.
In summary, while metals are not easy to compress due to their dense atomic structure and strong bonds, their compressibility can vary based on factors like crystal structure, type of metal, and external conditions. This property makes metals highly valuable for a wide range of industrial and scientific applications.
Summary Table:
Factor | Impact on Compressibility |
---|---|
Atomic Structure | Closely packed atoms and strong metallic bonds make metals resistant to compression. |
Bulk Modulus | High bulk modulus indicates significant pressure is needed to compress metals. |
Crystal Structure | BCC structures (e.g., iron) are more compressible than FCC or HCP structures. |
Type of Metal | Alkali metals (e.g., sodium) are more compressible than transition metals (e.g., iron). |
Temperature and Pressure | High temperatures and extreme pressures can increase compressibility. |
Practical Applications | Low compressibility makes metals ideal for construction, aerospace, and manufacturing. |
Want to learn more about the properties of metals and their applications? Contact us today for expert insights!