Yes, PVD (Physical Vapor Deposition) coating can be applied to plastic materials, but it requires careful consideration of the plastic's properties and specific pre-treatment steps to ensure proper adhesion and durability of the coating. PVD coating on plastics is commonly used in industries like automotive, electronics, and consumer goods to enhance aesthetics, durability, and functionality. However, the process is more challenging compared to coating metals due to the lower thermal and mechanical stability of plastics.
Key Points Explained:
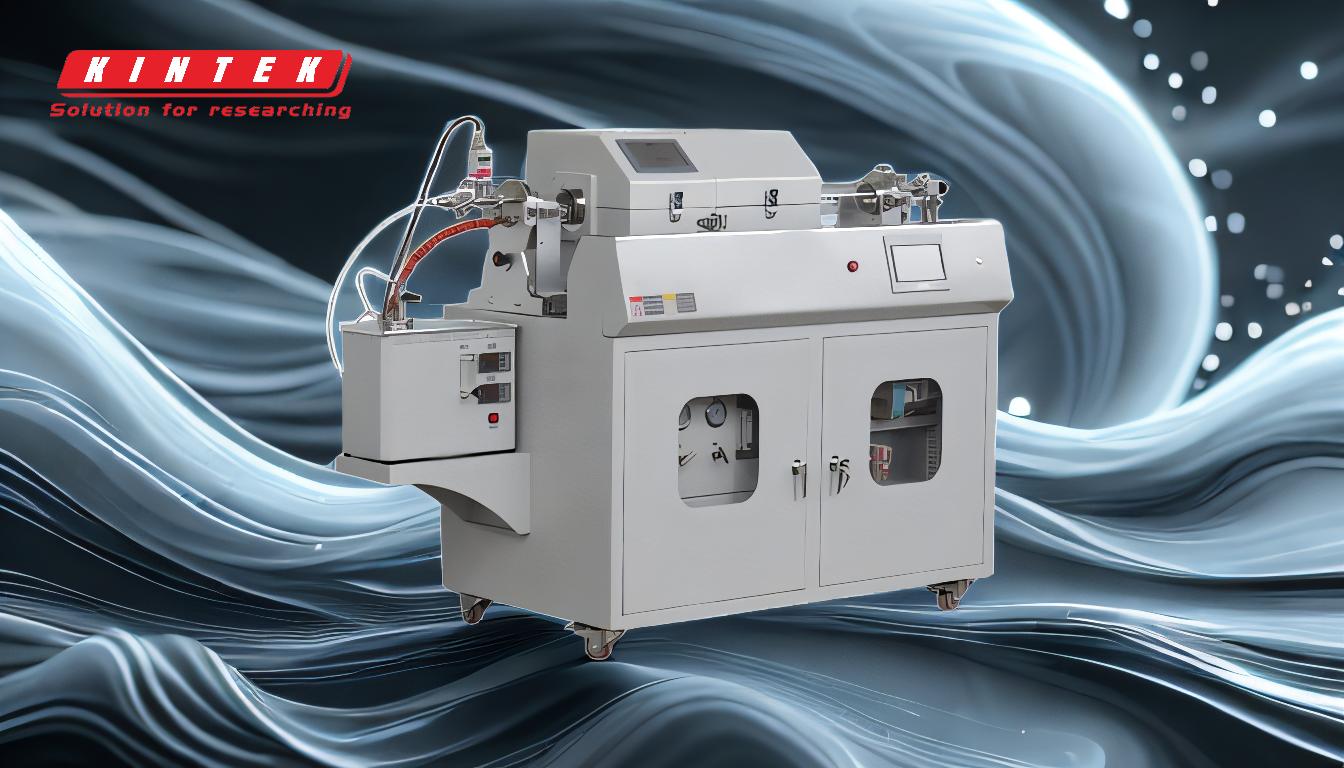
-
Feasibility of PVD Coating on Plastics
- PVD coating can be applied to plastics, but not all plastics are suitable. Thermoplastics like ABS, polycarbonate, and polyamide are commonly used because they can withstand the vacuum environment and moderate temperatures of the PVD process.
- The coating adheres well to plastics with proper surface preparation, but the process is more complex than coating metals due to the lower thermal stability and mechanical strength of plastics.
-
Challenges of PVD Coating on Plastics
- Thermal Sensitivity: Plastics have lower melting points and can deform or degrade under high temperatures. The PVD process must be carefully controlled to avoid overheating.
- Adhesion Issues: Plastics have smooth, non-porous surfaces that make adhesion difficult. Pre-treatment steps like plasma cleaning or chemical etching are often required to improve bonding.
- Mechanical Stress: The vacuum environment and coating process can cause mechanical stress on plastics, leading to cracking or warping.
-
Pre-Treatment Steps for Plastics
- Surface Cleaning: Plastics must be thoroughly cleaned to remove contaminants like oils, dust, or residues that can interfere with adhesion.
- Plasma Treatment: Plasma activation modifies the surface energy of plastics, making them more receptive to the PVD coating.
- Primer Application: A thin primer layer is sometimes applied to improve adhesion and create a uniform surface for the PVD coating.
-
PVD Process for Plastics
- The PVD process for plastics is similar to that for metals but operates at lower temperatures and shorter durations to avoid damaging the substrate.
- The vacuum chamber is evacuated to create a high-vacuum environment, and the target material is vaporized using techniques like sputtering or electron beam evaporation.
- The vaporized material is transported to the plastic substrate, where it condenses to form a thin, adherent coating.
-
Benefits of PVD Coating on Plastics
- Aesthetic Enhancement: PVD coatings can provide a metallic, glossy, or matte finish, enhancing the visual appeal of plastic components.
- Durability: The coating improves scratch resistance, wear resistance, and UV stability, extending the lifespan of plastic parts.
- Functionality: PVD coatings can add functional properties like electrical conductivity, anti-static properties, or barrier protection against moisture and gases.
-
Applications of PVD-Coated Plastics
- Automotive: Decorative trims, logos, and interior components.
- Electronics: Housings for smartphones, laptops, and wearables.
- Consumer Goods: Eyewear frames, kitchenware, and decorative items.
- Medical Devices: Coated plastic components for improved biocompatibility and durability.
-
Limitations and Considerations
- Not all plastics are suitable for PVD coating due to their thermal and mechanical properties.
- The process requires specialized equipment and expertise to ensure consistent results.
- The cost of PVD coating plastics can be higher than traditional coating methods, but the benefits often justify the investment.
In conclusion, while PVD coating on plastics is feasible and offers significant advantages, it requires careful material selection, pre-treatment, and process control to achieve optimal results. The ability to enhance both the aesthetics and functionality of plastic components makes PVD coating a valuable technique in various industries.
Summary Table:
Aspect | Details |
---|---|
Feasibility | Suitable for thermoplastics like ABS, polycarbonate, and polyamide. |
Challenges | Thermal sensitivity, adhesion issues, and mechanical stress. |
Pre-Treatment Steps | Surface cleaning, plasma treatment, and primer application. |
PVD Process | Operates at lower temperatures and shorter durations to protect plastics. |
Benefits | Aesthetic enhancement, improved durability, and added functionality. |
Applications | Automotive, electronics, consumer goods, and medical devices. |
Limitations | Requires specialized equipment, expertise, and higher costs. |
Discover how PVD coating can transform your plastic components—contact us today for expert guidance!