Electroplating is a process where a thin layer of metal is deposited onto a conductive surface to enhance properties such as conductivity, corrosion resistance, and aesthetics. While the plating forms a permanent chemical bond with the base metal, it is not entirely immune to wear and tear. Over time, factors like friction, environmental exposure, and mechanical stress can cause the plating to wear off. The thickness of the coating, typically around 0.0002 inches, plays a significant role in determining its durability. Although electroplating is cost-effective and widely used, its longevity depends on the application, environment, and maintenance.
Key Points Explained:
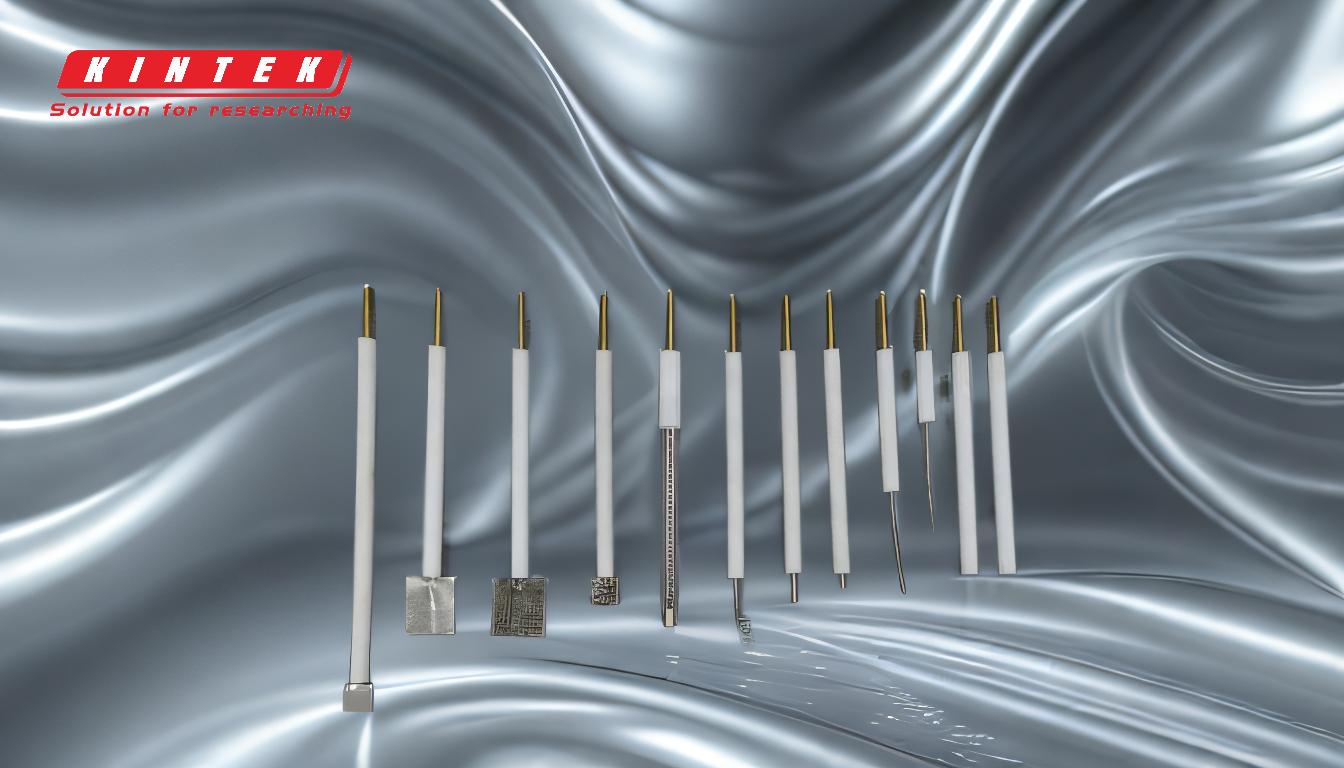
-
Nature of Electroplating Bonding
- Electroplating creates a chemical bond between the plated metal and the base material. This bond ensures that the plating is a permanent addition to the surface, meaning it will not naturally fall off or separate under normal conditions.
- The process involves depositing metal ions onto the cathode (the base material) using an anode made of a different metal. This results in a strong adhesion between the coating and the substrate.
-
Thickness of Electroplated Coatings
- The typical thickness of an electroplated coating is around 0.0002 inches. While this is sufficient for many applications, the thinness of the layer makes it susceptible to wear over time.
- Thicker coatings may offer better durability, but they also increase costs and may not be feasible for all applications.
-
Factors Leading to Wear and Tear
- Friction and Mechanical Stress: Continuous rubbing or abrasion can gradually wear down the plating. For example, in decorative applications like jewelry or automotive parts, frequent handling or exposure to harsh conditions can lead to thinning or loss of the coating.
- Environmental Exposure: Corrosive environments, such as those with high humidity, saltwater, or chemicals, can accelerate the degradation of the plating.
- Improper Maintenance: Lack of proper care, such as cleaning or protective measures, can reduce the lifespan of the electroplated surface.
-
Applications and Durability
- Electroplating is widely used for its cost-effectiveness and versatility. It is employed in industries ranging from electronics (for conductivity improvement) to decorative arts (for aesthetic appeal).
- The durability of the plating depends on the specific application. For instance, plating on consumer goods may wear off faster due to frequent use, while industrial components may retain their coating longer with proper maintenance.
-
Preventing Wear and Extending Lifespan
- Protective Coatings: Applying additional protective layers, such as clear coats or sealants, can help shield the plating from environmental factors and mechanical wear.
- Regular Maintenance: Cleaning and inspecting the plated surfaces can prevent buildup of contaminants that may accelerate wear.
- Material Selection: Choosing the right combination of base metal and plating material can enhance durability. For example, nickel or chromium plating is often used for its superior wear resistance.
-
Cost-Effectiveness of Electroplating
- Compared to other surface coating methods, electroplating is relatively inexpensive, making it a popular choice for a wide range of applications. However, the trade-off is the potential for wear over time, which may require re-plating or replacement in some cases.
In summary, while electroplating provides a durable and cost-effective solution for enhancing surface properties, it is not immune to wear. The longevity of the plating depends on factors such as thickness, application, environment, and maintenance. Understanding these factors can help in making informed decisions about the use and care of electroplated materials.
Summary Table:
Key Factor | Impact on Electroplating |
---|---|
Bonding | Permanent chemical bond ensures plating does not naturally fall off under normal conditions. |
Thickness | Thin coatings (~0.0002 inches) are durable but susceptible to wear over time. |
Friction/Mechanical Stress | Continuous abrasion can wear down the plating, especially in decorative applications. |
Environmental Exposure | Corrosive conditions like humidity or chemicals accelerate degradation. |
Maintenance | Proper care, such as cleaning and protective coatings, extends plating lifespan. |
Cost-Effectiveness | Electroplating is affordable but may require re-plating or replacement over time. |
Need expert advice on electroplating solutions? Contact us today to enhance your project's durability and performance!