Moulding presses are rated based on several key factors that determine their performance, capacity, and suitability for specific applications. These factors include the maximum force or pressure the press can exert, the size of the moulding area, the type of moulding process (e.g., compression, transfer, or injection moulding), and the material compatibility. Additionally, the speed, precision, and automation level of the press are critical considerations. Understanding these ratings helps purchasers select the right equipment for their production needs, ensuring efficiency and quality in the moulding process.
Key Points Explained:
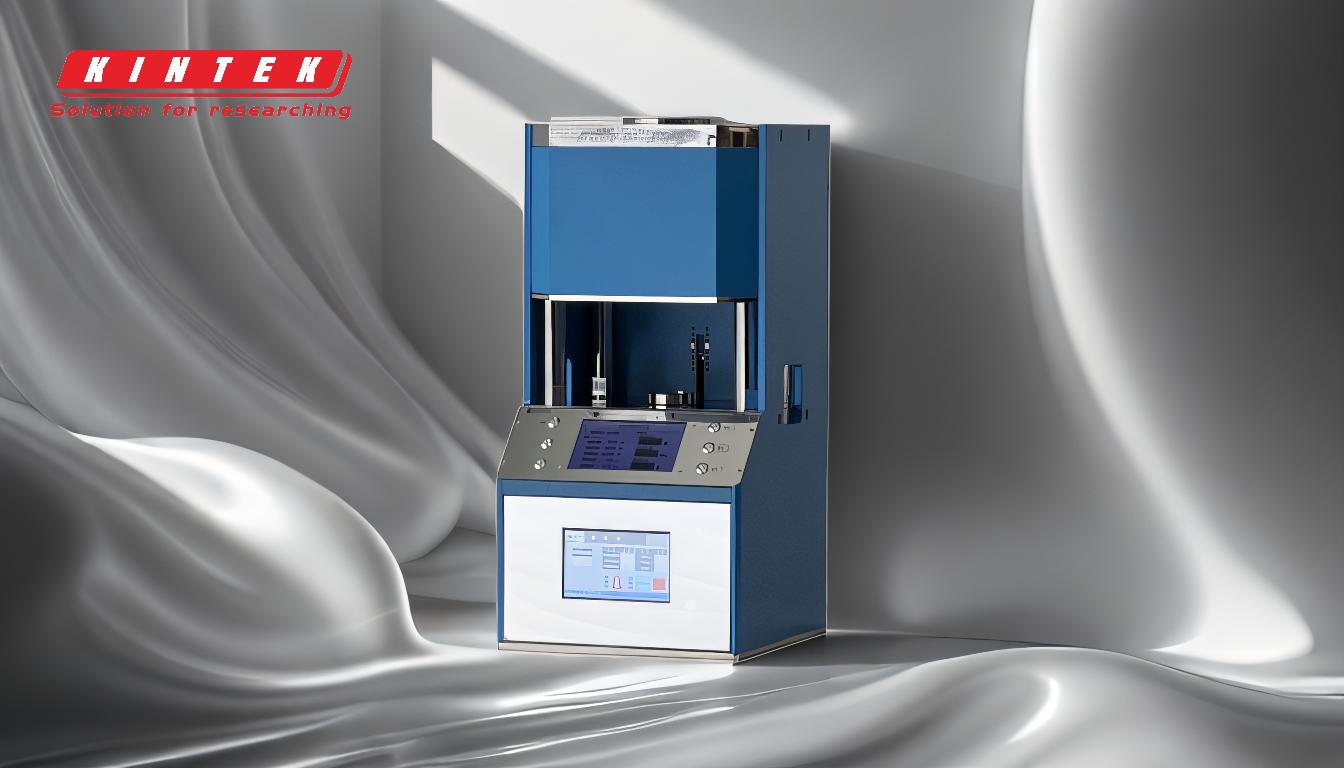
-
Maximum Force or Pressure:
- Moulding presses are often rated by the maximum force or pressure they can apply, typically measured in tons or kilonewtons (kN). This rating indicates the press's ability to compress or shape materials effectively.
- For example, a press rated at 100 tons can exert up to 100 tons of force, which is crucial for moulding dense or hard materials.
-
Moulding Area Size:
- The size of the moulding area, often referred to as the platen size, determines the maximum dimensions of the mould that can be used. This is critical for ensuring the press can accommodate the desired product size.
- Larger moulding areas allow for the production of bigger parts or multiple smaller parts in a single cycle.
-
Type of Moulding Process:
- Moulding presses are designed for specific processes such as compression, transfer, or injection moulding. Each process has unique requirements, and the press must be rated accordingly.
- For instance, injection moulding presses require precise control over temperature and pressure, while compression moulding presses need robust construction to handle high forces.
-
Material Compatibility:
- The press must be rated for compatibility with the materials being moulded, such as plastics, rubber, or composites. Different materials require different levels of force, temperature, and pressure.
- For example, moulding rubber might require lower temperatures but higher pressures compared to plastics.
-
Speed and Precision:
- The speed at which the press operates and its precision in applying force are critical ratings. High-speed presses can increase production rates, while precision ensures consistent product quality.
- Advanced presses may include features like programmable logic controllers (PLCs) for precise control over the moulding cycle.
-
Automation Level:
- The level of automation in a moulding press, from manual to fully automated, affects its rating. Automated presses can significantly reduce labor costs and increase consistency.
- Features like automatic mould changing, robotic part removal, and integrated quality control systems enhance the press's efficiency and reliability.
-
Energy Efficiency:
- Modern moulding presses are also rated based on their energy efficiency. Energy-efficient presses reduce operational costs and environmental impact.
- Look for presses with energy-saving features such as variable speed drives and efficient heating systems.
By considering these factors, purchasers can select a moulding press that meets their specific production requirements, ensuring optimal performance and cost-effectiveness.
Summary Table:
Factor | Description |
---|---|
Maximum Force/Pressure | Rated in tons or kN; crucial for compressing or shaping dense/hard materials. |
Moulding Area Size | Determines the maximum mould dimensions; larger areas allow bigger/multiple parts. |
Type of Moulding Process | Specific to processes like compression, transfer, or injection moulding. |
Material Compatibility | Must align with materials (e.g., plastics, rubber, composites) for optimal results. |
Speed and Precision | High-speed presses boost production; precision ensures consistent quality. |
Automation Level | Ranges from manual to fully automated; reduces labor costs and improves consistency. |
Energy Efficiency | Modern presses focus on reducing energy consumption and operational costs. |
Ready to choose the perfect moulding press for your needs? Contact our experts today for personalized advice!