Brazing is a critical process in metal joining, and improving its quality can lead to stronger, more reliable joints. Vacuum brazing, in particular, offers significant advantages by creating a controlled environment that minimizes impurities and enhances the performance of welded joints. By understanding the principles and techniques of vacuum brazing, you can achieve better results in your brazing projects. Below, we’ll explore key strategies to improve your brazing process, focusing on the benefits of vacuum brazing and practical steps to optimize your workflow.
Key Points Explained:
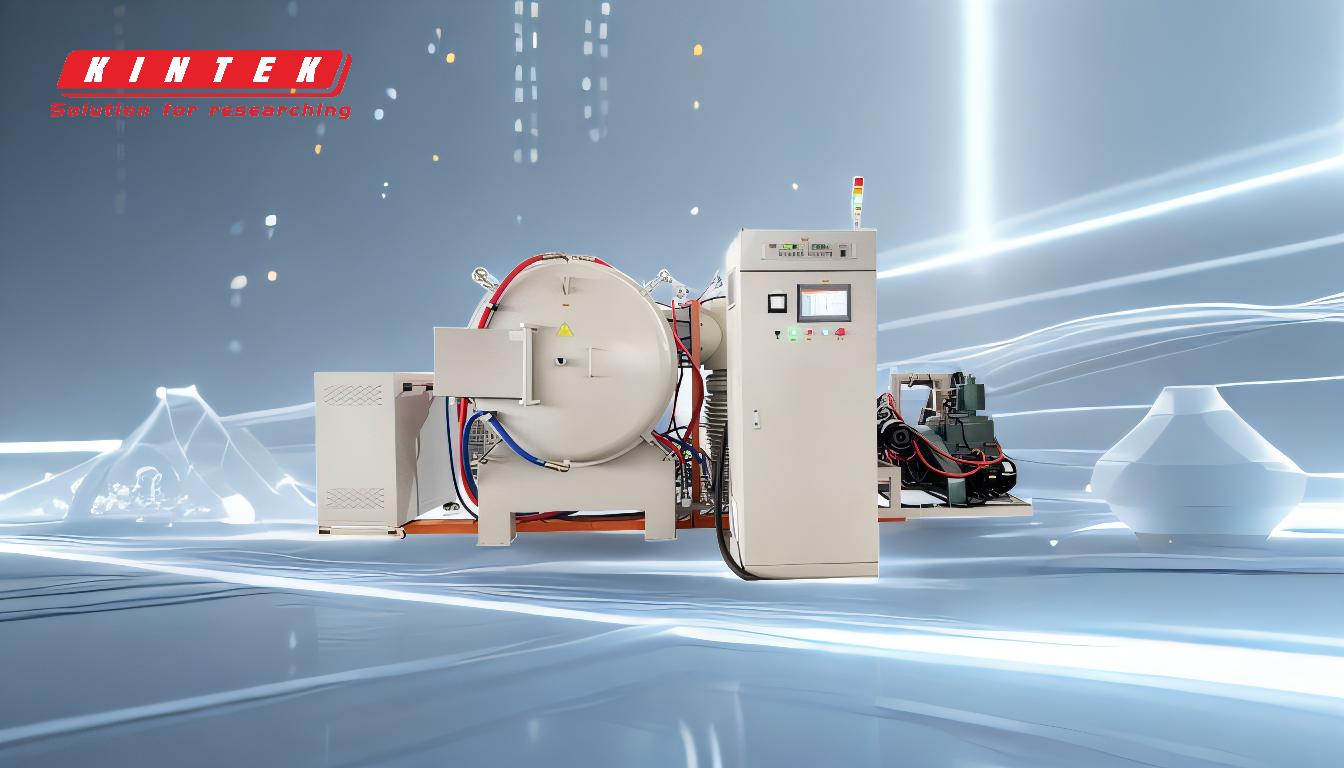
-
Understanding Vacuum Brazing
- Vacuum brazing is a process that takes place in a vacuum environment, which eliminates air and other gases that can interfere with the brazing process.
- This method is particularly effective for removing impurities such as oxides and air bubbles, which can compromise the quality of the weld.
- By performing brazing in a vacuum, you ensure a cleaner and more controlled environment, leading to higher-quality joints.
-
Eliminating Impurities
- In a vacuum environment, the absence of oxygen prevents the formation of oxides on the metal surfaces. Oxides can weaken the bond between the base metal and the filler material.
- Air bubbles, which can form during traditional brazing, are also eliminated. These bubbles can create weak spots in the joint, reducing its overall strength.
- The result is a cleaner, more uniform joint with fewer defects.
-
Enhancing Joint Performance
- Vacuum brazing allows for the formation of a thin, even layer of filler material at the joint. This layer is crucial for creating a strong bond between the two metal pieces.
- The controlled environment reduces the risk of cracks and deformation, which are common issues in traditional brazing methods.
- The improved joint performance translates to greater durability and reliability in the final product.
-
Optimizing Filler Material Application
- Choosing the right filler material is essential for successful brazing. The material should have a melting point lower than the base metals but high enough to ensure strength.
- In vacuum brazing, the filler material flows more evenly due to the absence of contaminants, resulting in a more consistent joint.
- Proper application techniques, such as pre-placing the filler material or using a paste, can further enhance the quality of the brazed joint.
-
Controlling Temperature and Heating Rates
- Temperature control is critical in vacuum brazing. The process requires precise heating to ensure the filler material melts and flows properly without overheating the base metals.
- Slow and uniform heating rates help prevent thermal stress, which can lead to cracks or warping.
- Using advanced equipment, such as a muffle furnace, can provide the necessary temperature control and uniformity.
-
Post-Brazing Inspection and Quality Control
- After brazing, it’s important to inspect the joints for any defects, such as voids, cracks, or incomplete bonding.
- Non-destructive testing methods, such as X-ray or ultrasonic inspection, can be used to ensure the integrity of the joint.
- Implementing a rigorous quality control process helps identify and address any issues before the final product is used.
-
Choosing the Right Equipment
- Investing in high-quality vacuum brazing equipment is essential for achieving consistent results.
- Look for equipment that offers precise temperature control, uniform heating, and a reliable vacuum system.
- Regular maintenance of the equipment ensures it operates at peak performance, reducing the risk of defects in the brazed joints.
-
Training and Skill Development
- Improving your brazing skills requires practice and knowledge. Consider attending training programs or workshops focused on advanced brazing techniques.
- Staying updated on the latest advancements in brazing technology can help you adopt new methods and improve your results.
- Collaborating with experienced professionals can provide valuable insights and tips for optimizing your brazing process.
By focusing on these key points, you can significantly improve the quality of your brazing projects. Vacuum brazing, in particular, offers a reliable way to achieve strong, defect-free joints, making it an excellent choice for high-performance applications.
Summary Table:
Key Strategy | Benefits |
---|---|
Vacuum Brazing | Eliminates impurities like oxides and air bubbles for cleaner joints. |
Filler Material Optimization | Ensures even flow and strong bonding with the right material selection. |
Temperature Control | Prevents thermal stress and warping with precise heating. |
Quality Inspection | Identifies defects early using non-destructive testing methods. |
Equipment Selection | High-quality vacuum brazing tools ensure consistent, reliable results. |
Skill Development | Training and collaboration improve techniques and outcomes. |
Ready to elevate your brazing process? Contact us today to learn more about vacuum brazing solutions!