Choosing the right heat treatment process involves understanding the specific requirements of the part, including its design, material, and intended application. The process should align with the desired outcomes, such as hardening, drying, or shaping, and consider factors like temperature, duration, and production volume. Whole-part hardening methods like furnace hardening or carburizing are ideal for uniform treatment, while selective methods like flame or induction heat treating are better for targeting specific areas. By evaluating these parameters, you can select the most suitable heat treatment process to achieve the desired material properties.
Key Points Explained:
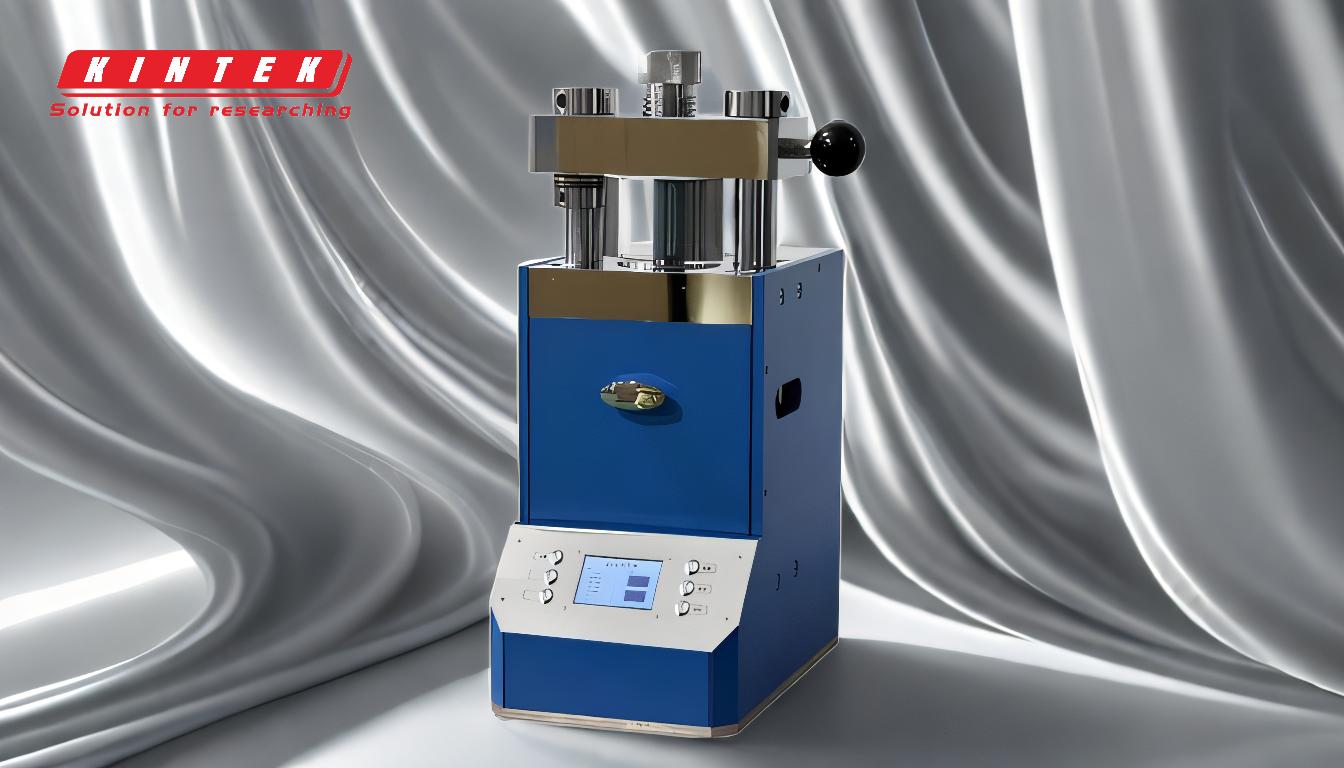
-
Understand the Part's Design and Engineering Requirements
- The design of the part and its engineering specifications play a crucial role in determining the appropriate heat treatment process. For example, complex geometries or specific mechanical properties may require tailored heat treatment methods.
- Whole-part hardening methods, such as furnace hardening or carburizing, are suitable for parts that need uniform hardness throughout. These methods ensure consistent material properties across the entire component.
-
Consider the Material Being Processed
- The type of material (e.g., steel, aluminum, or titanium) significantly influences the choice of heat treatment. Different materials respond differently to heat, and the process must align with the material's characteristics.
- For instance, carburizing is often used for low-carbon steels to increase surface hardness, while annealing is more suitable for softening metals like aluminum.
-
Determine the Desired Outcome
- The goal of the heat treatment process (e.g., hardening, tempering, or stress relief) dictates the method to be used. For example, hardening increases strength and wear resistance, while tempering reduces brittleness.
- Selective hardening methods, such as flame or induction heat treating, are ideal when only specific areas of a part need to be hardened, preserving the properties of the rest of the component.
-
Evaluate Temperature and Duration Requirements
- The temperature and duration of the heat treatment process are critical factors. High-temperature processes like austenitizing are used for hardening, while lower temperatures are suitable for processes like tempering.
- The duration of heating also affects the material's microstructure and properties. For example, prolonged heating during annealing can improve ductility.
-
Assess Production Volume and Efficiency
- The scale of production influences the choice of heat treatment method. High-volume production may require continuous furnaces, while batch furnaces are more suitable for smaller runs.
- Efficiency considerations, such as energy consumption and processing time, should also be evaluated to ensure cost-effectiveness.
-
Match the Process to the Part's End Application
- The final application of the part determines the necessary material properties. For example, parts subjected to high stress or wear may require surface hardening, while components needing flexibility may benefit from annealing.
- Understanding the part's operational environment ensures the chosen heat treatment process delivers the required performance characteristics.
By systematically evaluating these factors, you can select the most appropriate heat treatment process to achieve the desired material properties and ensure the part meets its intended application requirements.
Summary Table:
Factor | Key Considerations |
---|---|
Part Design & Requirements | Complex geometries, mechanical properties, uniform vs. selective hardening methods |
Material Type | Steel, aluminum, titanium; material-specific processes like carburizing or annealing |
Desired Outcome | Hardening, tempering, stress relief; strength, wear resistance, or flexibility |
Temperature & Duration | High vs. low temperatures; heating duration for microstructure changes |
Production Volume & Efficiency | Batch vs. continuous furnaces; energy consumption and processing time |
End Application | High stress, wear, or flexibility requirements; operational environment |
Need help selecting the right heat treatment process? Contact our experts today for tailored solutions!