Thermal treatment processes, such as those used in PECVD (Plasma-Enhanced Chemical Vapor Deposition) equipment, vary significantly based on the type of plasma generation and the interaction between the plasma and the substrate. The three primary types of thermal treatment in PECVD are direct PECVD, inductively coupled plasma reactors, and remote plasma reactors. Each method has unique characteristics, including how plasma is generated, how it interacts with the substrate, and the level of contamination risk. Understanding these differences is crucial for selecting the appropriate equipment for specific applications, such as anti-reflective coatings on solar cells.
Key Points Explained:
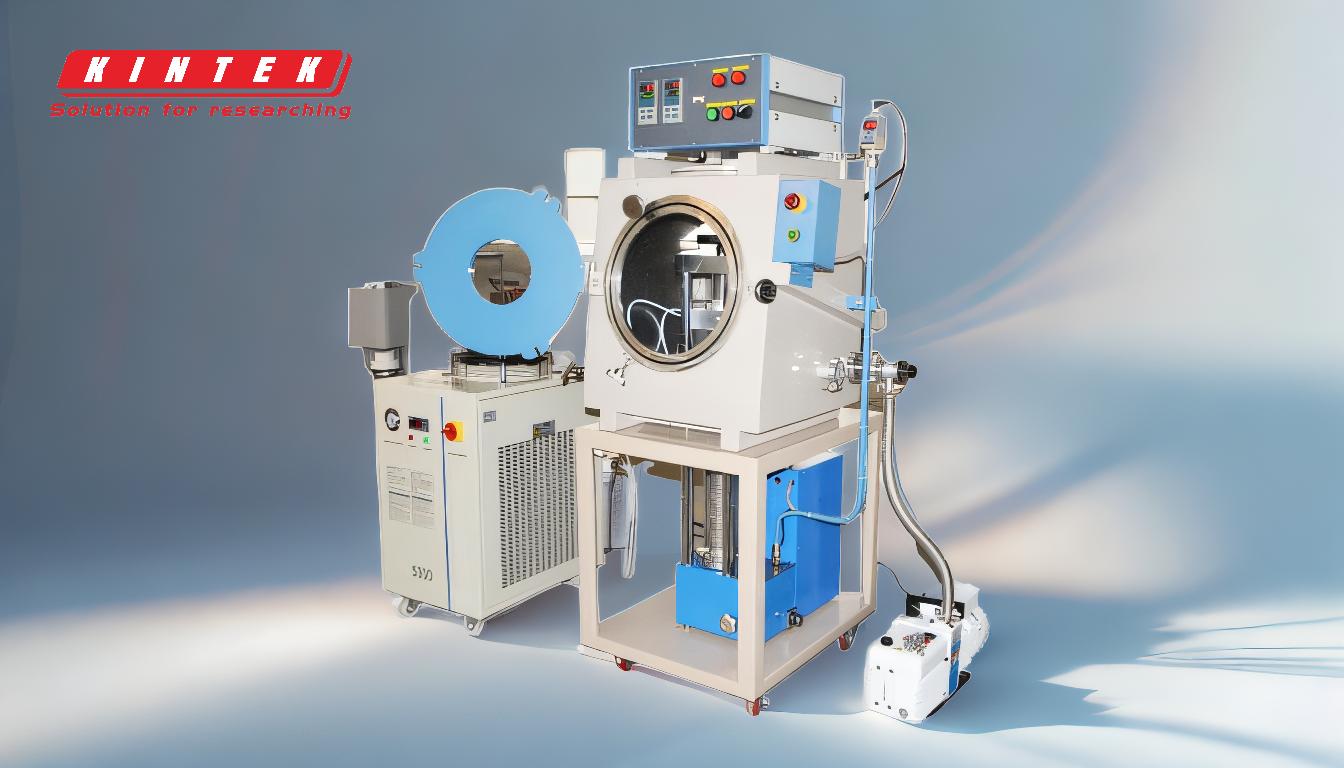
-
Direct PECVD Reactors:
- Plasma Generation: Direct PECVD reactors use capacitively coupled plasma, where the plasma is in direct contact with the substrate.
- Interaction with Substrate: The direct contact allows for efficient energy transfer and deposition of thin films.
- Contamination Risk: Higher risk of contamination due to the direct interaction between the plasma and the substrate.
- Applications: Commonly used in applications requiring precise and efficient thin-film deposition, such as anti-reflective coatings on solar cells.
-
Inductively Coupled Plasma Reactors:
- Plasma Generation: In inductively coupled plasma reactors, the electrodes are placed outside the reaction chamber, generating plasma through inductive coupling.
- Interaction with Substrate: The plasma is not in direct contact with the substrate, reducing contamination risks.
- Contamination Risk: Lower contamination risk compared to direct PECVD reactors.
- Applications: Suitable for applications where contamination control is critical, such as in semiconductor manufacturing.
-
Remote Plasma Reactors:
- Plasma Generation: Remote plasma reactors generate plasma in a separate chamber and then transport it to the substrate chamber.
- Interaction with Substrate: The substrate is not exposed to the plasma generation process, minimizing contamination.
- Contamination Risk: Lowest contamination risk among the three types.
- Applications: Ideal for highly sensitive processes where contamination must be minimized, such as in advanced microelectronics.
-
Process Gases and Plasma Interaction:
- Gases Used: Common process gases include silane and ammonia, which are ionized into plasma within the reactor.
- Plasma Characteristics: The plasma is chemically reactive, facilitating the deposition of thin films on substrates like silicon chips.
- Role in Applications: Essential for producing anti-reflective coatings on solar cell chips, enhancing their efficiency.
-
Equipment Selection Considerations:
- Contamination Control: Choose inductively coupled or remote plasma reactors for applications requiring low contamination.
- Efficiency and Precision: Direct PECVD reactors are preferred for applications needing high precision and efficient thin-film deposition.
- Application-Specific Needs: Consider the specific requirements of the application, such as the need for anti-reflective coatings or advanced semiconductor features.
Understanding these differences helps in selecting the right PECVD equipment for specific thermal treatment needs, ensuring optimal performance and minimal contamination risks.
Summary Table:
Type | Plasma Generation | Interaction with Substrate | Contamination Risk | Applications |
---|---|---|---|---|
Direct PECVD Reactors | Capacitively coupled plasma in direct contact with the substrate. | Efficient energy transfer and deposition of thin films. | Higher contamination risk due to direct interaction. | Anti-reflective coatings on solar cells. |
Inductively Coupled Plasma Reactors | Electrodes outside the chamber generate plasma through inductive coupling. | Plasma not in direct contact with the substrate, reducing contamination. | Lower contamination risk compared to direct PECVD. | Semiconductor manufacturing. |
Remote Plasma Reactors | Plasma generated in a separate chamber and transported to the substrate chamber. | Substrate not exposed to plasma generation, minimizing contamination. | Lowest contamination risk among the three types. | Advanced microelectronics. |
Need help selecting the right PECVD equipment for your needs? Contact our experts today!