Calculating the cost of firing an electric kiln, such as an electric rotary kiln, involves understanding the kiln's energy consumption, operational parameters, and the cost of electricity. The process requires breaking down the kiln's wattage, converting it to kilowatts, and factoring in the cost per kilowatt-hour from your energy bill. Additionally, material characteristics like specific heat, thermal conductivity, and temperature profiles influence the kiln's efficiency and energy usage. By following a systematic approach, you can accurately estimate the cost of firing your kiln.
Key Points Explained:
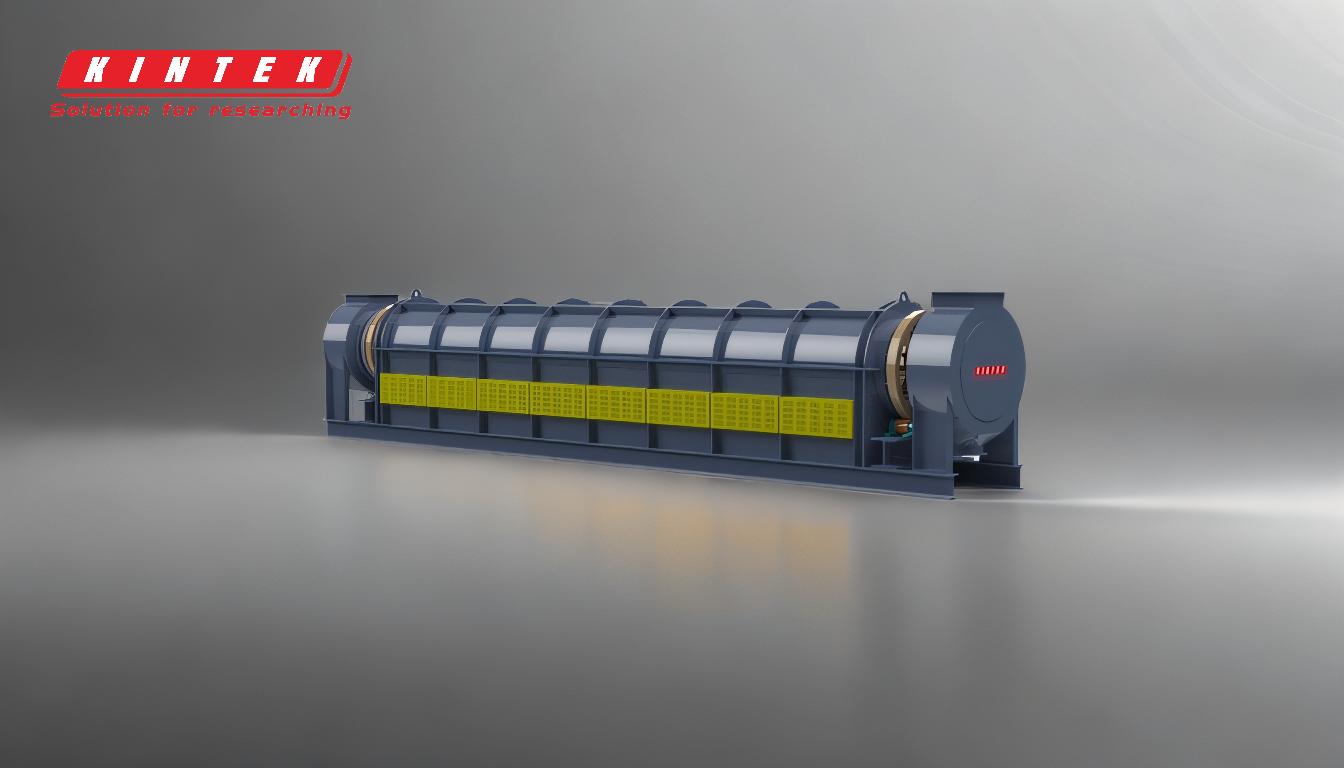
-
Determine the Kiln's Wattage:
- The first step in calculating the cost of firing an electric kiln is to determine its wattage. This is done by multiplying the kiln's voltage (V) by its amperage (A). For example, if your kiln operates at 240 volts and draws 30 amps, the wattage would be: [ \text{Wattage} = \text{Volts} \times \text{Amps} = 240 , \text{V} \times 30 , \text{A} = 7200 , \text{W} ]
- This wattage represents the power consumption of the kiln during operation.
-
Convert Wattage to Kilowatts:
- Since electricity costs are typically calculated per kilowatt-hour (kWh), you need to convert the wattage to kilowatts by dividing by 1000: [ \text{Kilowatts (kW)} = \frac{\text{Wattage}}{1000} = \frac{7200 , \text{W}}{1000} = 7.2 , \text{kW} ]
- This conversion simplifies the calculation of energy consumption.
-
Multiply by Kilowatt-Hour Cost:
- Next, multiply the kilowatts by the cost per kilowatt-hour as stated on your energy bill. For instance, if your electricity costs $0.12 per kWh: [ \text{Hourly Cost} = \text{Kilowatts} \times \text{Cost per kWh} = 7.2 , \text{kW} \times $0.12/\text{kWh} = $0.864/\text{hour} ]
- This gives you the cost of operating the kiln for one hour.
-
Adjust for Kiln Efficiency:
- Kilns are not 100% efficient, so it's important to account for this by multiplying the hourly cost by 0.75 (assuming 75% efficiency): [ \text{Adjusted Hourly Cost} = \text{Hourly Cost} \times 0.75 = $0.864/\text{hour} \times 0.75 = $0.648/\text{hour} ]
- This adjustment provides a more realistic estimate of the actual energy cost.
-
Calculate Total Firing Cost:
- To determine the total cost of firing the kiln, multiply the adjusted hourly cost by the total firing time. For example, if the firing process takes 8 hours: [ \text{Total Firing Cost} = \text{Adjusted Hourly Cost} \times \text{Firing Time} = $0.648/\text{hour} \times 8 , \text{hours} = $5.184 ]
- This is the estimated cost of firing the kiln for the specified duration.
-
Consider Material Characteristics:
- The design and operation of an electric rotary kiln are influenced by material characteristics such as specific heat, thermal conductivity, and temperature profiles. These factors affect the kiln's energy consumption and efficiency. For example:
- Specific Heat: Materials with higher specific heat require more energy to reach the desired temperature.
- Thermal Conductivity: Poor thermal conductivity can lead to uneven heating, increasing energy usage.
- Temperature Profiles: The required temperature range and duration of heating impact the overall energy cost.
- The design and operation of an electric rotary kiln are influenced by material characteristics such as specific heat, thermal conductivity, and temperature profiles. These factors affect the kiln's energy consumption and efficiency. For example:
-
Optimize Kiln Operation:
- To minimize firing costs, consider optimizing the kiln's operational parameters:
- Retention Time: Adjusting the retention time to match the material's requirements can reduce unnecessary energy consumption.
- Bed Profile: Ensuring an optimal bed profile improves heat transfer and reduces energy waste.
- Feed Rate: Controlling the feed rate helps maintain consistent heating and prevents overloading the kiln.
- To minimize firing costs, consider optimizing the kiln's operational parameters:
By following these steps and considering the material characteristics, you can accurately calculate the cost of firing an electric rotary kiln and identify opportunities to optimize energy usage.
Summary Table:
Step | Calculation | Example |
---|---|---|
Determine Kiln Wattage | Volts × Amps | 240V × 30A = 7200W |
Convert Wattage to Kilowatts | Wattage ÷ 1000 | 7200W ÷ 1000 = 7.2kW |
Multiply by Kilowatt-Hour Cost | Kilowatts × Cost per kWh | 7.2kW × $0.12/kWh = $0.864/hour |
Adjust for Kiln Efficiency | Hourly Cost × Efficiency (e.g., 0.75 for 75%) | $0.864/hour × 0.75 = $0.648/hour |
Calculate Total Firing Cost | Adjusted Hourly Cost × Firing Time | $0.648/hour × 8 hours = $5.184 |
Consider Material Characteristics | Specific heat, thermal conductivity, and temperature profiles influence costs | Higher specific heat = higher energy requirement |
Optimize Kiln Operation | Adjust retention time, bed profile, and feed rate for efficiency | Shorter retention time = reduced energy usage |
Need help calculating your kiln's firing costs or optimizing its efficiency? Contact our experts today for personalized advice!