To calculate the power of an induction furnace, the primary formula used is ( P = \frac{C \times T \times G}{0.24 \times t \times \eta} ), where ( C ) is the specific heat of the material, ( T ) is the heating temperature, ( G ) is the workpiece weight, ( t ) is the heating time, and ( \eta ) is the heating efficiency. Additionally, factors like material properties, heating time, productivity, and desired yearly production are considered to ensure accurate power calculations. For example, if the desired yearly production is 2000 tons, the required power supply capacity can be calculated based on hourly production and standard power consumption rates, resulting in a specific power requirement like 325 kW for the given example.
Key Points Explained:
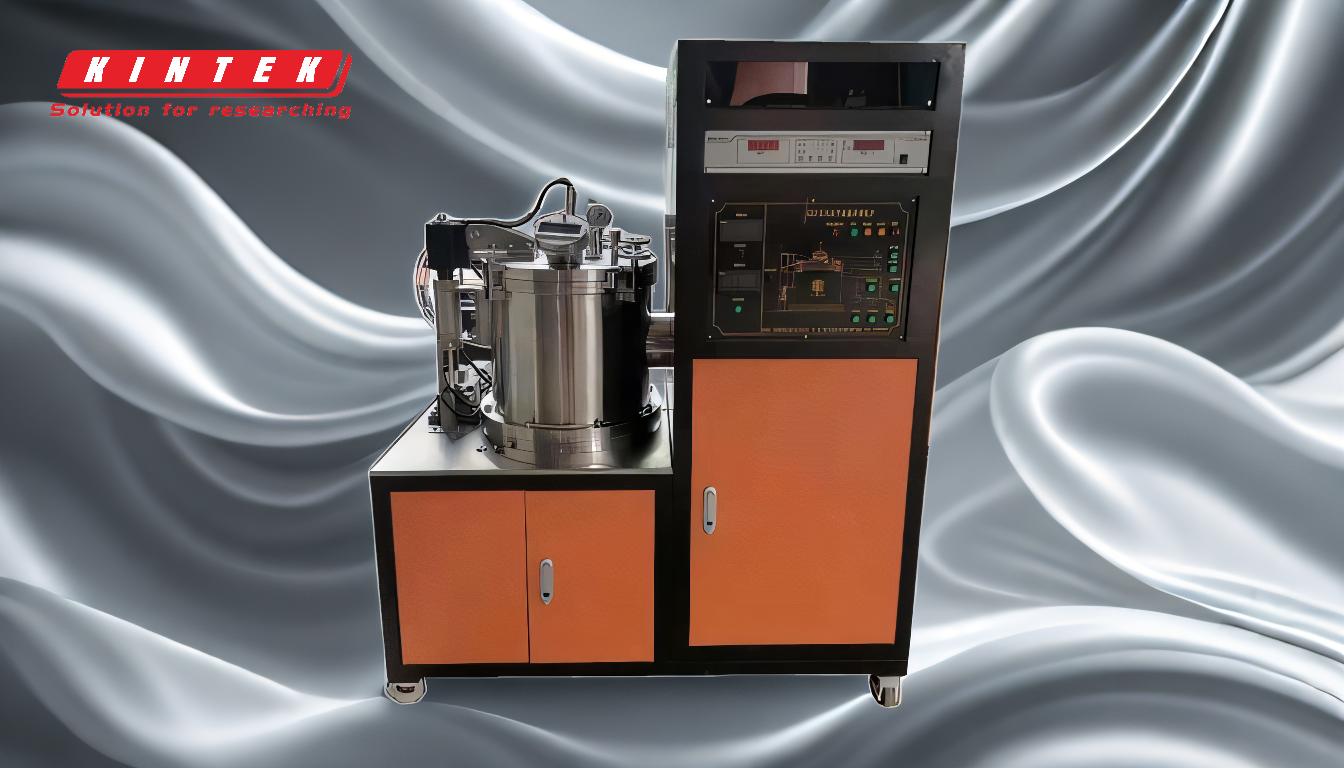
-
Power Calculation Formula:
- The formula ( P = \frac{C \times T \times G}{0.24 \times t \times \eta} ) is central to determining the power of an induction furnace.
- Specific Heat (C): This is the amount of heat required to raise the temperature of one kilogram of the material by one degree Celsius (kcal/kg℃). It varies depending on the material being heated.
- Heating Temperature (T): The desired temperature to which the material needs to be heated (℃).
- Workpiece Weight (G): The mass of the material being heated (kg).
- Heating Time (t): The duration required to heat the material to the desired temperature (seconds).
- Heating Efficiency (η): A factor representing the efficiency of the heating process, typically around 0.6.
-
Factors Influencing Power Calculation:
- Material Properties: Different materials have different specific heats, which directly affect the power required.
- Heating Time: Shorter heating times require higher power inputs.
- Productivity: The desired output rate (e.g., tons per hour) influences the total power needed.
- Heating Temperature: Higher temperatures require more energy.
- Workpiece Weight: Larger or heavier workpieces require more power to heat.
-
Practical Example Based on Yearly Production:
- Desired Yearly Production: For instance, 2000 tons per year.
- Daily Production: Calculated as 8.33 tons/day (assuming 240 working days in a year).
- Hourly Production: 0.520 tons/hour (520 kg/hour).
- Standard Power Consumption: 625 kWh/ton.
- Required Power Calculation: ( (520 , \text{kg/hour}) \times (625 , \text{kWh}/1000 , \text{kg}) = 325 , \text{kW} ).
- This means a power supply capacity of 325 kW is needed to meet the production target.
-
Heating Efficiency (η):
- The efficiency factor (η) accounts for losses in the heating process. A typical value of 0.6 means that 60% of the input energy is effectively used for heating, while the rest is lost, often as heat to the surroundings or through other inefficiencies.
-
Importance of Accurate Calculations:
- Accurate power calculations ensure that the induction furnace is neither underpowered (leading to insufficient heating) nor overpowered (leading to unnecessary energy consumption and costs).
- These calculations are based on years of industry experience and empirical data to ensure reliability and efficiency.
By understanding and applying these key points, one can accurately determine the power requirements for an induction furnace, ensuring optimal performance and energy efficiency.
Summary Table:
Variable | Description | Unit |
---|---|---|
C (Specific Heat) | Heat required to raise 1 kg of material by 1°C | kcal/kg℃ |
T (Heating Temp) | Desired temperature for heating | ℃ |
G (Workpiece Weight) | Mass of the material being heated | kg |
t (Heating Time) | Time required to heat the material | seconds |
η (Efficiency) | Heating efficiency, typically 0.6 (60%) | - |
P (Power) | Power required for the induction furnace | kW |
Example Calculation | For 2000 tons/year production, power required = 325 kW | - |
Need help calculating the power for your induction furnace? Contact our experts today for accurate and reliable solutions!