Thin film metal deposition is a critical process in various industries, including electronics, optics, and coatings. It involves applying a thin layer of metal onto a substrate using specific techniques. These methods are broadly categorized into chemical and physical deposition techniques. Chemical methods include processes like chemical vapor deposition (CVD), plasma-enhanced CVD (PECVD), and atomic layer deposition (ALD), while physical methods primarily involve physical vapor deposition (PVD) techniques such as sputtering, thermal evaporation, and electron beam evaporation. Each method has its unique advantages, applications, and limitations, making the choice of technique dependent on the desired film properties, substrate material, and specific application requirements.
Key Points Explained:
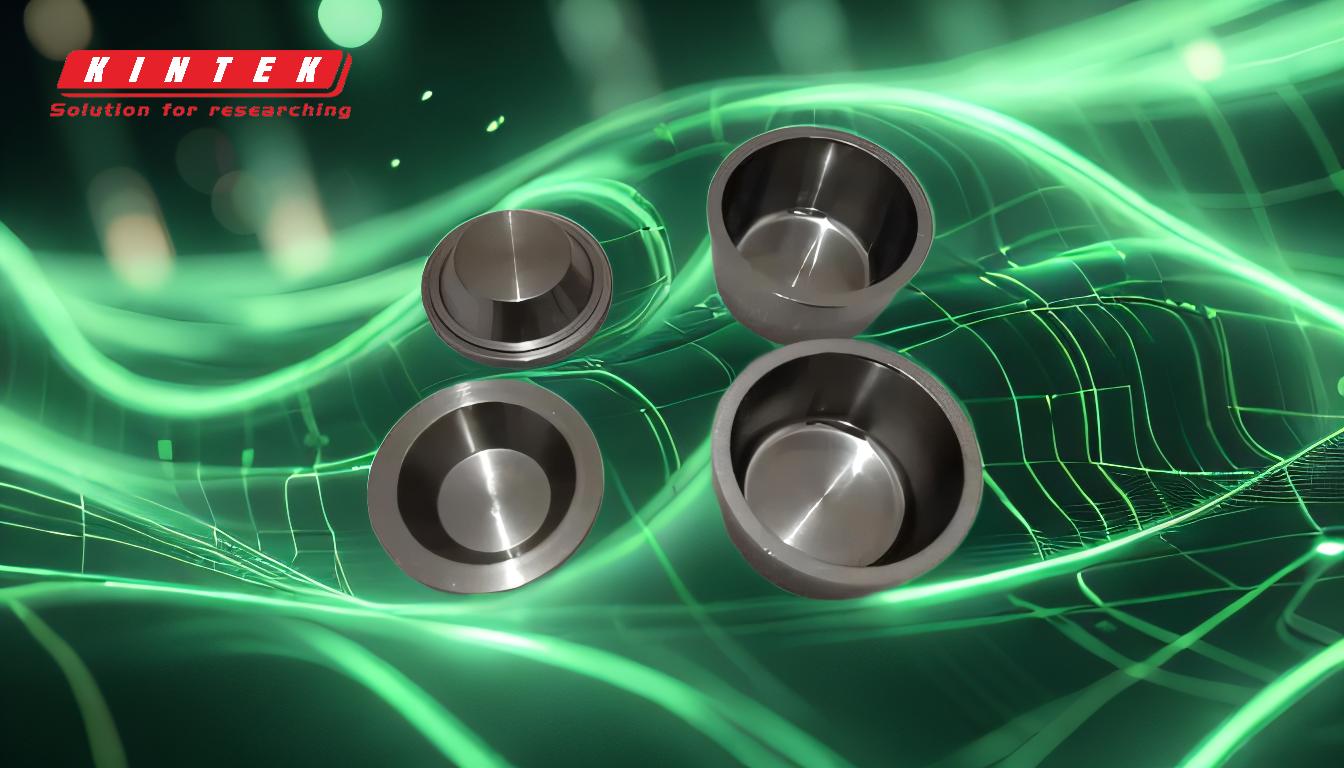
-
Categories of Thin Film Deposition Methods:
- Thin film deposition methods are broadly categorized into chemical and physical techniques.
-
Chemical methods involve chemical reactions to deposit the thin film, such as:
- Chemical Vapor Deposition (CVD): A process where a substrate is exposed to volatile precursors, which react and decompose on the substrate surface to form the desired thin film.
- Plasma-Enhanced CVD (PECVD): A variant of CVD that uses plasma to enhance chemical reactions, allowing deposition at lower temperatures.
- Atomic Layer Deposition (ALD): A precise method where thin films are deposited one atomic layer at a time, offering excellent control over film thickness and uniformity.
-
Physical methods rely on physical processes to deposit the thin film, such as:
-
Physical Vapor Deposition (PVD): A technique where the material is vaporized from a solid source and then condensed onto the substrate. Common PVD methods include:
- Sputtering: A process where atoms are ejected from a solid target material due to bombardment by energetic ions, which then deposit onto the substrate.
- Thermal Evaporation: A method where the material is heated to its vaporization point in a vacuum, and the vapor condenses on the substrate.
- Electron Beam Evaporation: Similar to thermal evaporation, but an electron beam is used to heat the material, allowing for higher melting point materials to be deposited.
- Pulsed Laser Deposition (PLD): A technique where a high-power laser pulse is used to vaporize the target material, which then deposits onto the substrate.
-
Physical Vapor Deposition (PVD): A technique where the material is vaporized from a solid source and then condensed onto the substrate. Common PVD methods include:
-
Chemical Deposition Techniques:
-
Chemical Vapor Deposition (CVD):
- Process: Involves the chemical reaction of gaseous precursors on a heated substrate surface, leading to the formation of a solid thin film.
- Applications: Widely used in semiconductor manufacturing, coatings for tools, and optical devices.
- Advantages: High-quality films with good uniformity and conformality.
- Limitations: Requires high temperatures and precise control of gas flow and pressure.
-
Plasma-Enhanced CVD (PECVD):
- Process: Similar to CVD but uses plasma to enhance the chemical reactions, allowing deposition at lower temperatures.
- Applications: Used in the production of thin-film solar cells, microelectronics, and protective coatings.
- Advantages: Lower deposition temperatures, faster deposition rates.
- Limitations: More complex equipment and process control compared to standard CVD.
-
Atomic Layer Deposition (ALD):
- Process: A sequential, self-limiting process where alternating precursor gases are introduced to the substrate, forming one atomic layer at a time.
- Applications: Ideal for depositing ultra-thin, highly uniform films in semiconductor devices, MEMS, and nanotechnology.
- Advantages: Excellent thickness control, uniformity, and conformality.
- Limitations: Slow deposition rates and high cost.
-
Chemical Vapor Deposition (CVD):
-
Physical Deposition Techniques:
-
Sputtering:
- Process: Atoms are ejected from a solid target material by bombarding it with high-energy ions, which then deposit onto the substrate.
- Applications: Commonly used in the production of thin-film transistors, optical coatings, and decorative coatings.
- Advantages: Good adhesion, high purity films, and the ability to deposit a wide range of materials.
- Limitations: Requires a vacuum environment and can be slower compared to other methods.
-
Thermal Evaporation:
- Process: The material is heated to its vaporization point in a vacuum, and the vapor condenses on the substrate.
- Applications: Used in the production of thin films for solar cells, optical coatings, and electronic devices.
- Advantages: Simple and cost-effective for depositing metals and simple compounds.
- Limitations: Limited to materials with lower melting points and less control over film uniformity.
-
Electron Beam Evaporation:
- Process: Similar to thermal evaporation, but an electron beam is used to heat the material, allowing for higher melting point materials to be deposited.
- Applications: Used in the production of high-quality optical coatings, semiconductor devices, and wear-resistant coatings.
- Advantages: Can deposit high melting point materials, high deposition rates.
- Limitations: Requires complex equipment and precise control of the electron beam.
-
Pulsed Laser Deposition (PLD):
- Process: A high-power laser pulse is used to vaporize the target material, which then deposits onto the substrate.
- Applications: Used in the production of complex oxide films, superconductors, and thin-film materials for research.
- Advantages: Can deposit complex materials with precise stoichiometry.
- Limitations: Limited to small-area deposition and requires precise control of laser parameters.
-
Sputtering:
-
Choosing the Right Deposition Method:
- The choice of deposition method depends on several factors, including:
- Material Properties: The type of material to be deposited (e.g., metal, oxide, semiconductor).
- Substrate Compatibility: The material and thermal stability of the substrate.
- Film Thickness and Uniformity: The required thickness and uniformity of the thin film.
- Deposition Rate: The speed at which the film needs to be deposited.
- Cost and Complexity: The budget and available equipment for the deposition process.
- For example:
- CVD and ALD are preferred for highly uniform and conformal films, especially in semiconductor applications.
- Sputtering and Evaporation are commonly used for depositing metals and simple compounds in optical and electronic applications.
- PLD is ideal for depositing complex materials with precise stoichiometry, often used in research and development.
- The choice of deposition method depends on several factors, including:
In conclusion, thin film metal deposition is a versatile process with a wide range of techniques available, each suited to specific applications and material requirements. Understanding the strengths and limitations of each method is crucial for selecting the appropriate technique for a given application.
Summary Table:
Category | Techniques | Applications | Advantages | Limitations |
---|---|---|---|---|
Chemical Methods | CVD, PECVD, ALD | Semiconductor manufacturing, optical devices, thin-film solar cells | High-quality films, precise control, lower temperatures (PECVD) | High cost (ALD), complex equipment (PECVD) |
Physical Methods | Sputtering, Thermal Evaporation, Electron Beam Evaporation, PLD | Optical coatings, electronic devices, research on complex materials | Good adhesion, high purity, ability to deposit high melting point materials | Requires vacuum, slower deposition rates, limited to small areas (PLD) |
Need help selecting the right thin film deposition method for your application? Contact our experts today!